OEM high precision stainless steel sheet metal parts
Description
Product Type | customized product | |||||||||||
One-Stop Service | Mold development and design-submit samples-batch production-inspection-surface treatment-packaging-delivery. | |||||||||||
Process | stamping,bending,deep drawing,sheet metal fabrication,welding,laser cutting etc. | |||||||||||
Materials | carbon steel,stainless steel,aluminum,copper,galvanized steel etc. | |||||||||||
Dimensions | according to customer's drawings or samples. | |||||||||||
Finish | Spray painting, electroplating, hot-dip galvanizing, powder coating, electrophoresis, anodizing, blackening, etc. | |||||||||||
Application Area | Auto parts, agricultural machinery parts, engineering machinery parts, construction engineering parts, garden accessories, environmentally friendly machinery parts, ship parts, aviation parts, pipe fittings, hardware tool parts, toy parts, electronic parts, etc. |
Advantages
1. More than 10 years of overseas trade expertise.
2. Provide one-stop service from mold design to product delivery.
3. Fast delivery time, about 30-40 days. In stock within one week.
4. Strict quality management and process control (ISO certified manufacturer and factory).
5. More reasonable prices.
6. Professional, our factory has more than 10 years of history in the field of metal stamping sheet metal.
Quality management
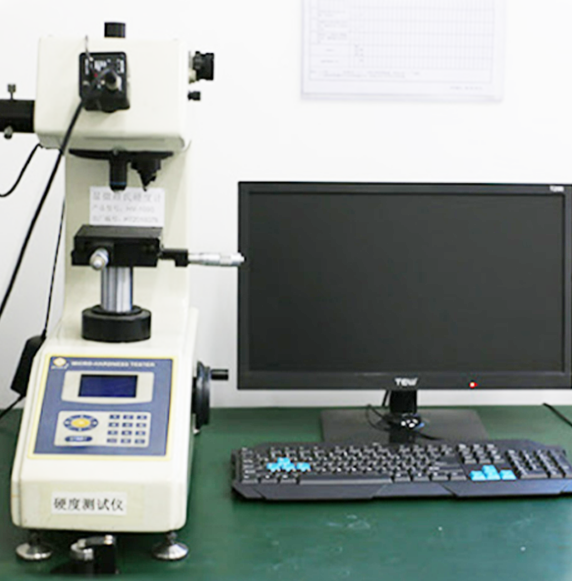
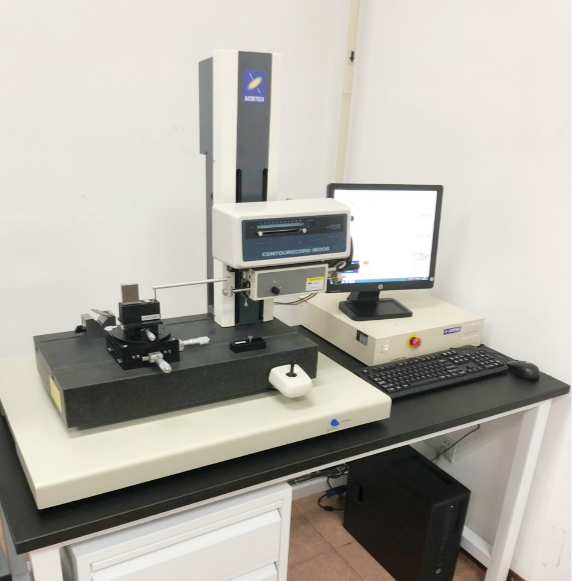
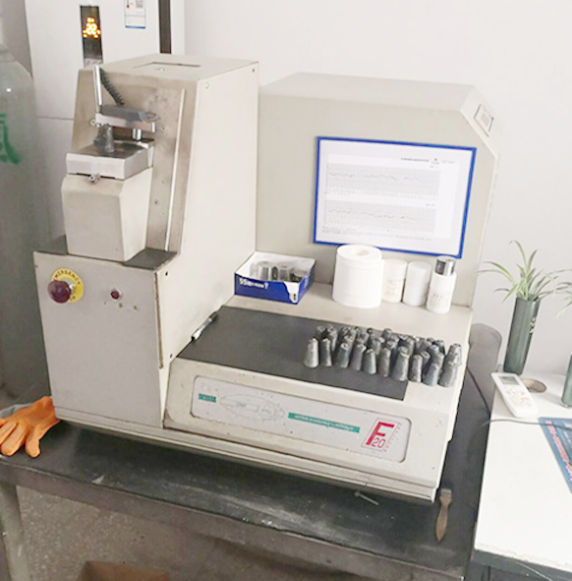
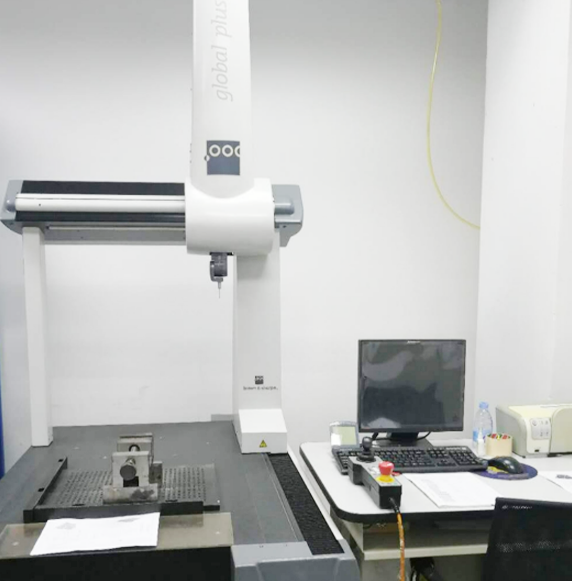
Vickers hardness instrument.
Profile measuring instrument.
Spectrograph instrument.
Three coordinate instrument.
Shipment Picture
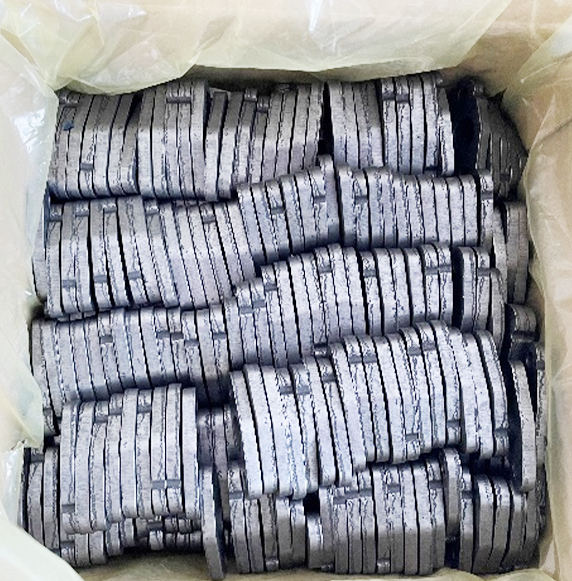
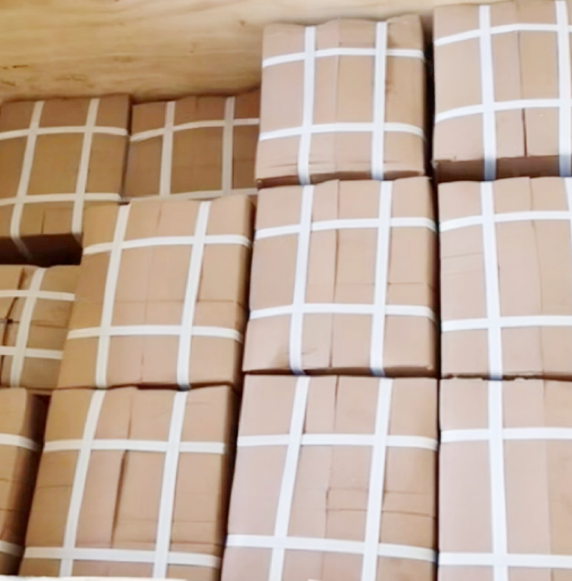
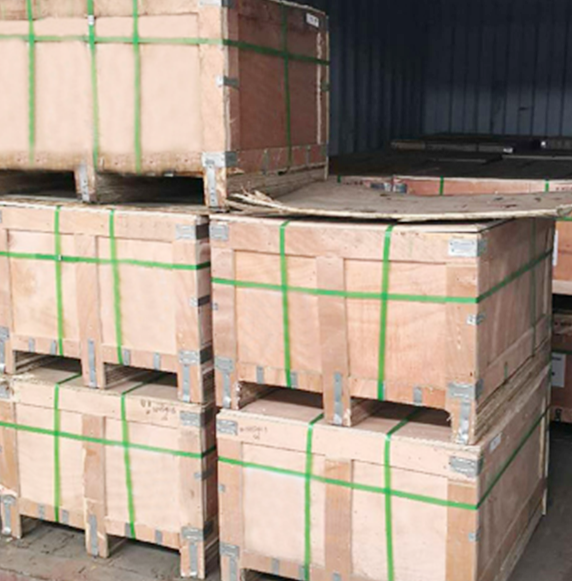
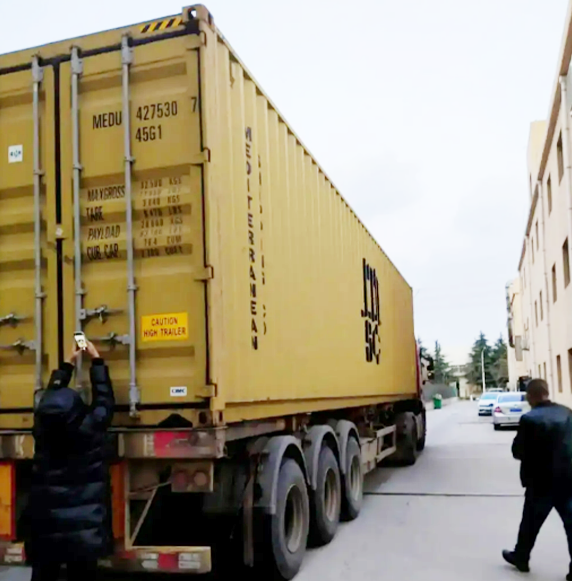
Production Process
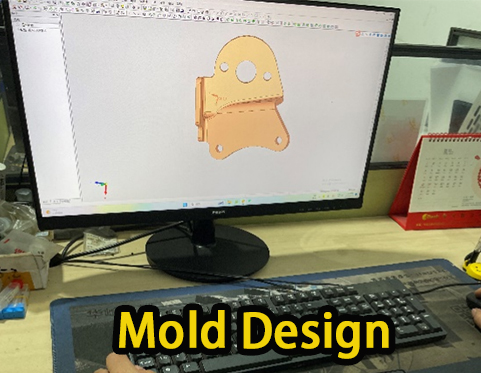
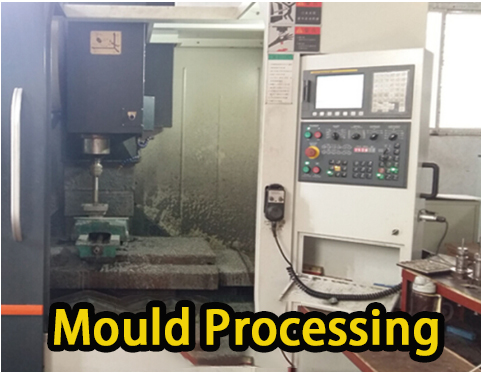
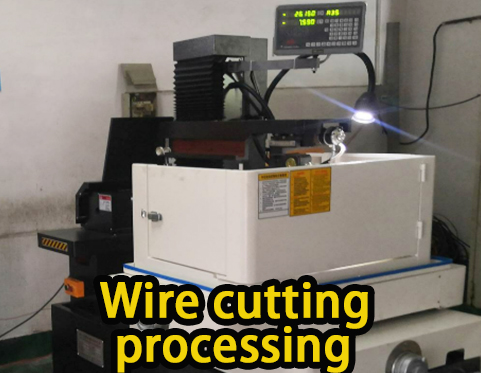
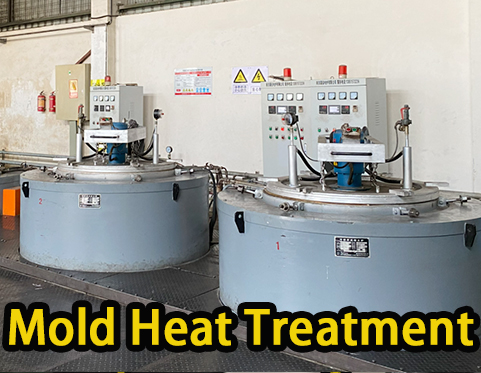
01. Mold design
02. Mould Processing
03. Wire cutting processing
04. Mold heat treatment
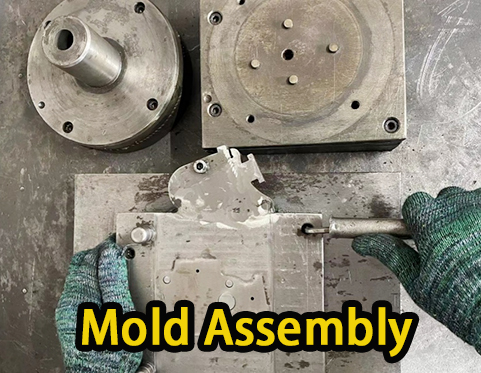
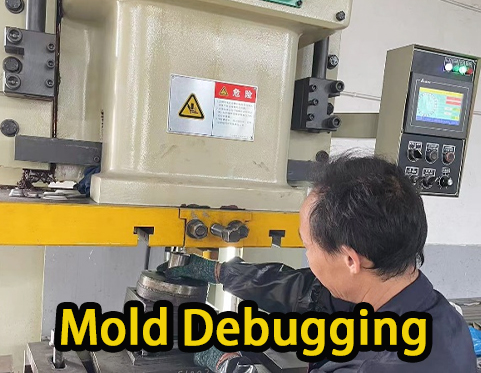
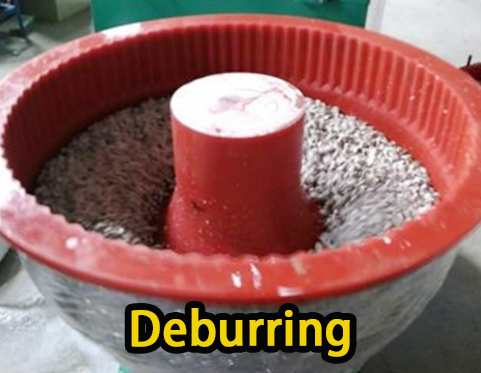

05. Mold assembly
06. Mold debugging
07. Deburring
08. electroplating
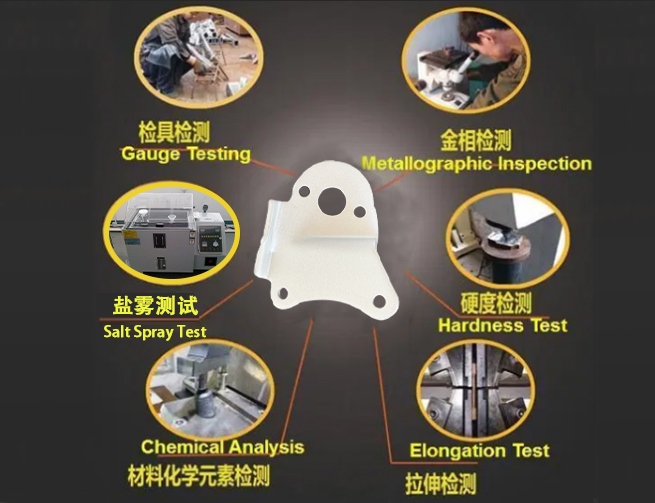
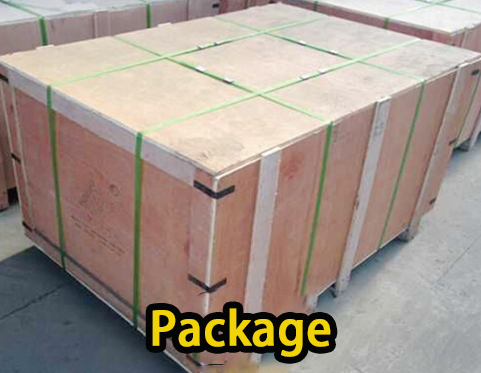
09. Product Testing
10. Package
Electrophoretic coating
The electrophoretic coating process is a coating method that uses an external electric field to make the pigments and resin particles suspended in the electrophoretic liquid migrate in a directional manner and deposit on the surface of the substrate of one of the electrodes. Let's take a look at its basic process flow:
Process principle
Electrophoretic coating is mainly based on electrophoresis and electrodeposition. During the electrophoretic coating process, the paint particles (resins and pigments) move toward the cathode under the action of the electric field, while the negatively charged particles move toward the anode. When the positively charged particles (resins and pigments) reach the surface of the cathode (the object to be coated), they obtain electrons and react with hydroxide ions to become water-insoluble substances, which are deposited on the cathode (the object to be coated) to form a uniform coating film.
Process composition
The electrophoretic coating process generally consists of the following four main processes:
1. Pretreatment before coating: including pre-cleaning, degreasing, rust removal, neutralization, water washing, phosphating, passivation and other processes. These pretreatment processes are crucial to the quality and performance of the coating. They ensure that the surface of the coated object is free of oil and rust, and that the phosphate film is densely and evenly crystallized.
2. Electrophoretic coating: After the pretreatment is completed, the workpiece is immersed in the electrophoretic tank and electrophoretic coating is performed by direct current. In this process, the paint particles migrate directionally under the action of the electric field and deposit on the surface of the workpiece.
3. Post-electrophoretic cleaning: After the electrophoretic coating is completed, the workpiece needs to be cleaned to remove the tank liquid and other impurities attached to the surface. The cleaning process generally includes steps such as tank cleaning and ultrafiltration water washing.
4. Drying of electrophoretic coating: Finally, the workpiece coated with the electrophoretic coating is dried to solidify it into a hard coating. The drying temperature and time depend on the type of coating used and the requirements of the workpiece.
Process characteristics
The coating is plump, uniform, flat, and smooth, with good decorative and protective properties.
The coating hardness, adhesion, corrosion resistance, impact performance, and penetration performance are significantly better than other coating processes.
The use of water-soluble paint, with water as the dissolving medium, saves a lot of organic solvents, reduces air pollution and environmental hazards.
The coating efficiency is high, the coating loss is small, and the coating utilization rate can reach 90%~95%.
Process parameter management
The electrophoretic coating process conditions include parameters such as the composition of the bath liquid, solid content, ash content, MEQ (the number of millimoles of acid required per 100 grams of solid content of paint) and organic solvent content. The management of these parameters is crucial to ensure the quality and performance of the coating. At the same time, it is also necessary to pay attention to the influence of factors such as the selection of the filtration system and the size of the circulation volume on the stability of the bath liquid and the quality of the paint film.
Precautions
During the electrophoretic coating process, the power supply should be stable to avoid the influence of voltage fluctuations on the coating quality.
Regularly check the status of the electrophoretic tank and equipment to ensure their normal operation.
Strictly control the electrophoretic coating process parameters to ensure that the quality and performance of the coating meet the requirements.
Pay attention to safe operation to avoid accidents such as electric shock and fire during the electrophoretic coating process.
WHY CHOOSE US
1.Professional metal stamping parts and sheet metal fabrication for over 10 years.
2.We pay more attention to high standard in production.
3.Excellent service at 24/7.
4.Fast delivery time within one month.
5.Strong technology team back up and support R&D development.
6.Offer OEM cooperation.
7.Good feedback and rare complains among our customers.
8.All products are in good durability and good mechanical property.
9.reasonable and competitive price.