OEM Hardware Custom Galvanized Steel Stamped Support Bracket
Description
Product Type | customized product | |||||||||||
One-Stop Service | Mold development and design-submit samples-batch production-inspection-surface treatment-packaging-delivery. | |||||||||||
Process | stamping,bending,deep drawing,sheet metal fabrication,welding,laser cutting etc. | |||||||||||
Materials | carbon steel,stainless steel,aluminum,copper,galvanized steel etc. | |||||||||||
Dimensions | according to customer's drawings or samples. | |||||||||||
Finish | Spray painting, electroplating, hot-dip galvanizing, powder coating, electrophoresis, anodizing, blackening, etc. | |||||||||||
Application Area | Auto parts, agricultural machinery parts, engineering machinery parts, construction engineering parts, garden accessories, environmentally friendly machinery parts, ship parts, aviation parts, pipe fittings, hardware tool parts, toy parts, electronic parts, etc. |
Advantags
1. More than 10 years of overseas trade expertise.
2. Provide one-stop service from mold design to product delivery.
3. Fast delivery time, about 30-40 days. In stock within one week.
4. Strict quality management and process control (ISO certified manufacturer and factory).
5. More reasonable prices.
6. Professional, our factory has more than 10 years of history in the field of metal stamping sheet metal.
Quality management
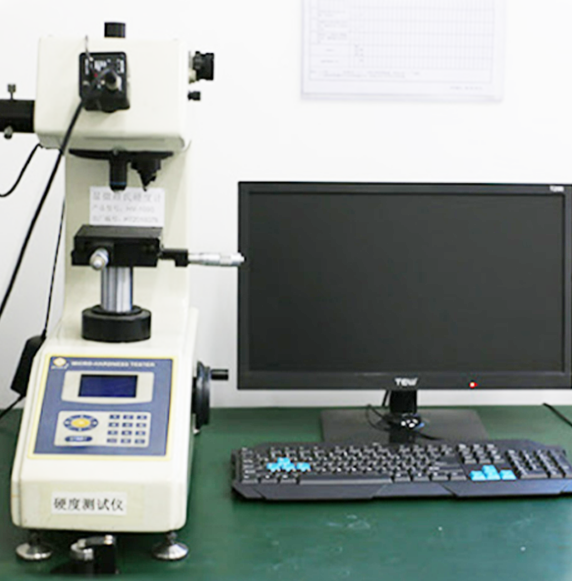
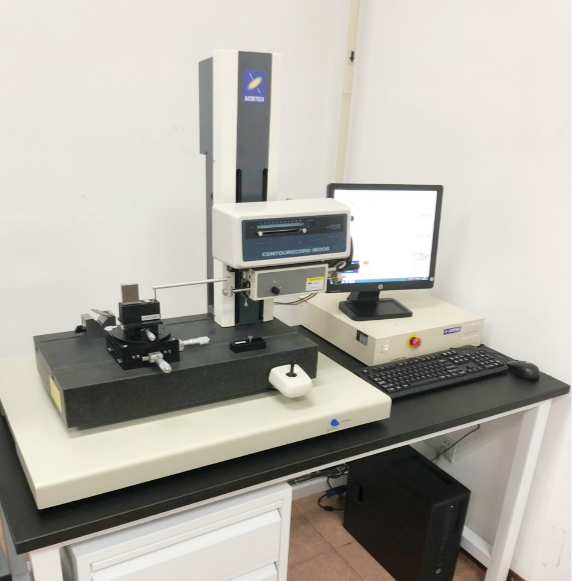
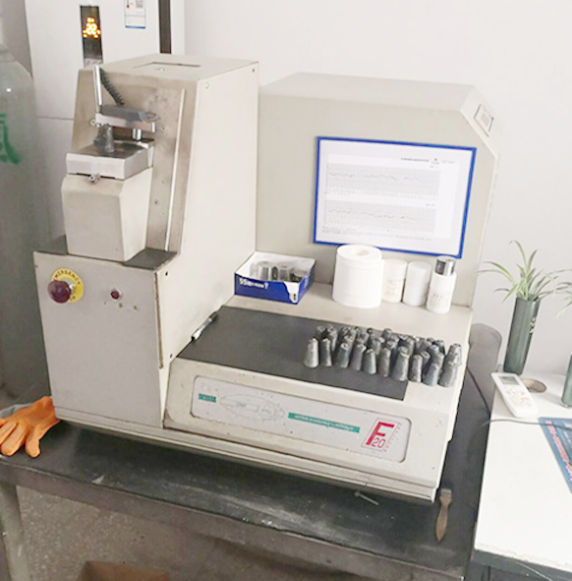
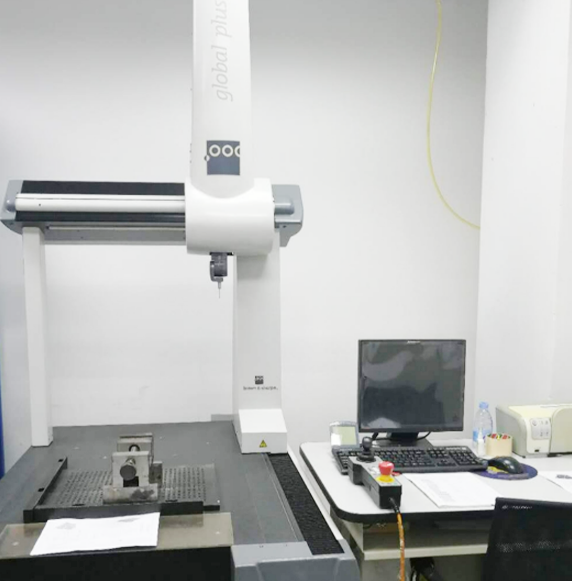
Vickers hardness instrument.
Profile measuring instrument.
Spectrograph instrument.
Three coordinate instrument.
Shipment Picture
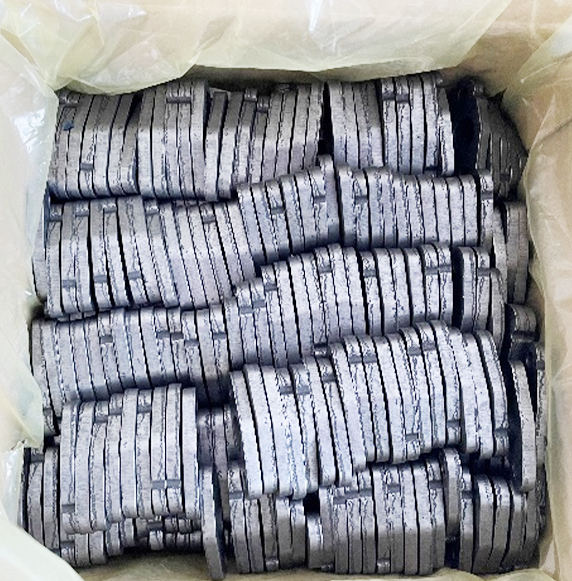
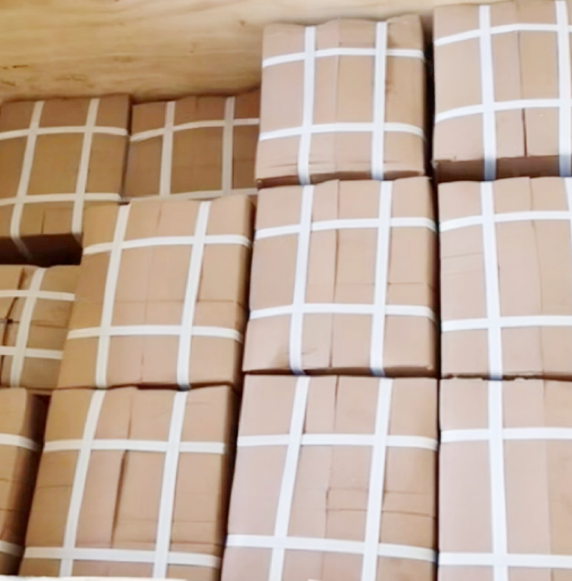
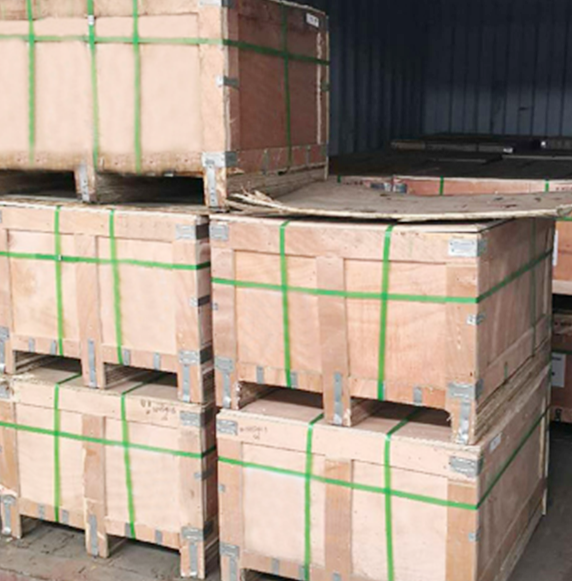
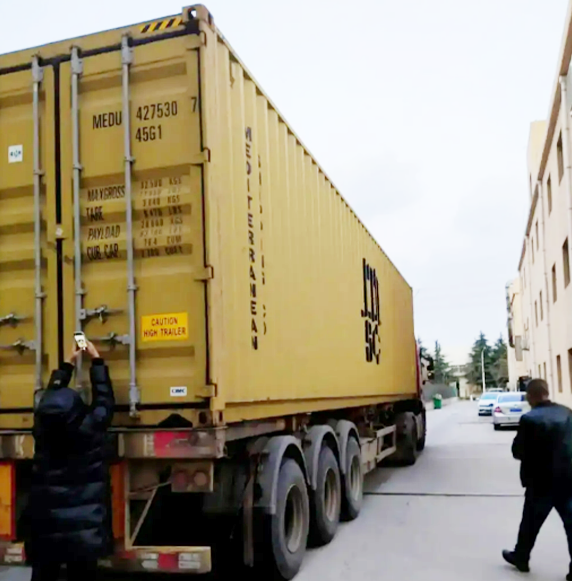
Production Process
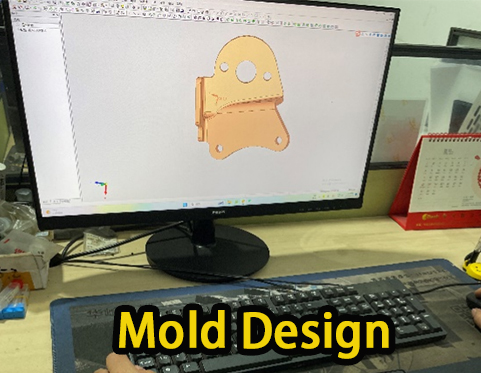
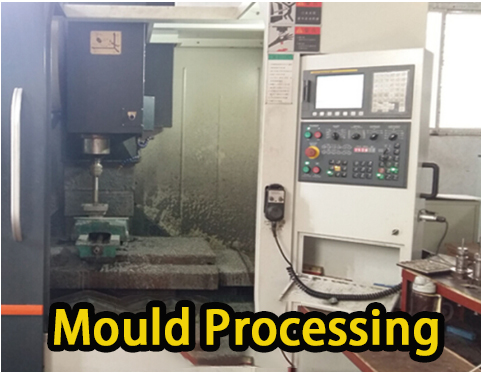
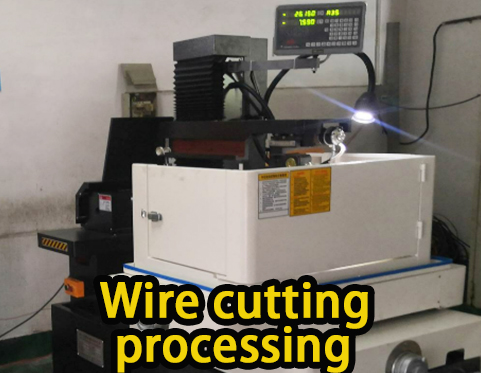
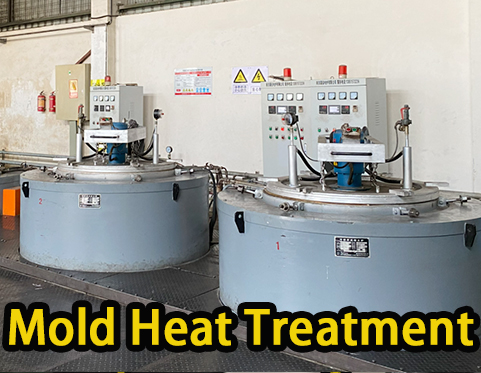
01. Mold design
02. Mould Processing
03. Wire cutting processing
04. Mold heat treatment
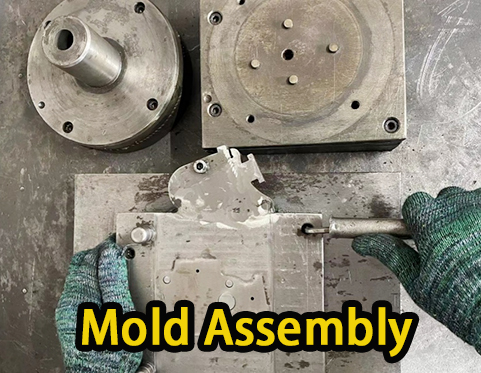
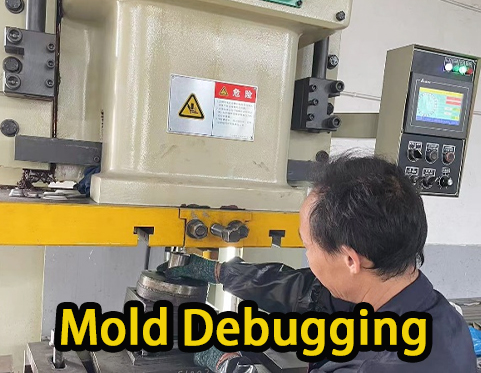
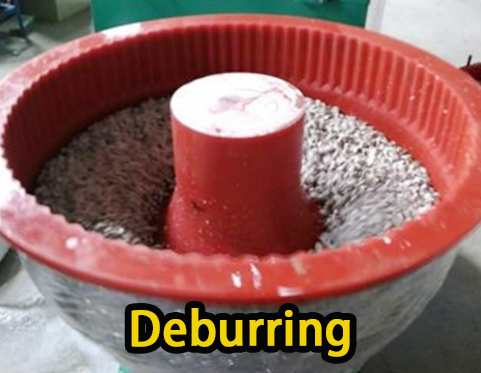

05. Mold assembly
06. Mold debugging
07. Deburring
08. electroplating
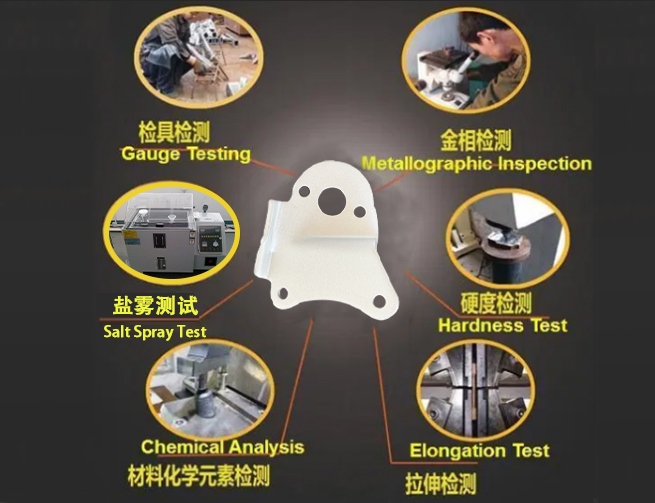
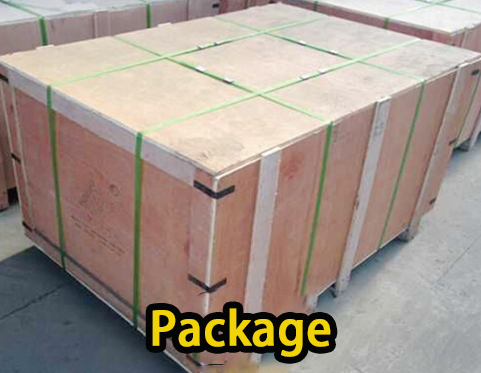
09. Product Testing
10. Package
company advantage
The lowest cost materials—which should not be confused with the lowest quality—along with a production system that maximizes efficiency to eliminate as much non-value labor as possible while ensuring that the process produces products of 100% quality—are the starting points for every product and process.
Verify that each item satisfies the necessary tolerances, surface polish, and requirements. Watch the progress of the machining. For our quality control system, we have received ISO 9001:2015 and ISO 9001:2000 quality system certification.
In 2016, the business began exporting goods abroad in addition to providing OEM and ODM services. Over a hundred local and foreign clients have trusted it since then, and it has built strong working relationships with them.
To produce a finished product of the highest caliber, we provide all surface treatments, including sandblasting, polishing, anodizing, electroplating, electrophoresis, laser etching, and painting.
Introduction to galvanizing
The process of "galvanizing" metal, alloys, or other materials to prevent corrosion and improve their visual appeal involves coating the surface of the substance with a layer of zinc. The primary procedure is hot dip galvanizing.
Zinc is referred to be an amphoteric metal because of its high solubility in both acids and alkalis. In dry air, zinc does not vary much. On the zinc surface, a thick layer of basic zinc carbonate will develop in humid air. Zinc has a low corrosion resistance in sulfur dioxide, hydrogen sulfide, and marine atmospheres. The galvanized coating is easily corroded, especially in environments with high temperatures, high humidity, and organic acid.
Zinc has a typical electrode potential of -0.76 V. Anodic coatings like galvanizing are applied to steel substrates. mostly employed to stop the corrosion of steel. Its ability to protect is directly correlated with the coating's thickness. The galvanized layer's decorative and protective qualities can be greatly enhanced by passivating, dying, or applying a gloss protectant coating.