High Precision Aluminum Stainless Steel SPHC SPCC Sheet Metal Stamping Part
Description
Product Type | customized product | |||||||||||
One-Stop Service | Mold development and design-submit samples-batch production-inspection-surface treatment-packaging-delivery. | |||||||||||
Process | stamping,bending,deep drawing,sheet metal fabrication,welding,laser cutting etc. | |||||||||||
Materials | carbon steel,stainless steel,aluminum,copper,galvanized steel etc. | |||||||||||
Dimensions | according to customer's drawings or samples. | |||||||||||
Finish | Spray painting, electroplating, hot-dip galvanizing, powder coating, electrophoresis, anodizing, blackening, etc. | |||||||||||
Application Area | Auto parts, agricultural machinery parts, engineering machinery parts, construction engineering parts, garden accessories, environmentally friendly machinery parts, ship parts, aviation parts, pipe fittings, hardware tool parts, toy parts, electronic parts, etc. |
Advantags
1. More than 10 years of overseas trade expertise.
2. Provide one-stop service from mold design to product delivery.
3. Fast delivery time, about 30-40 days. In stock within one week.
4. Strict quality management and process control (ISO certified manufacturer and factory).
5. More reasonable prices.
6. Professional, our factory has more than 10 years of history in the field of metal stamping sheet metal.
Quality management
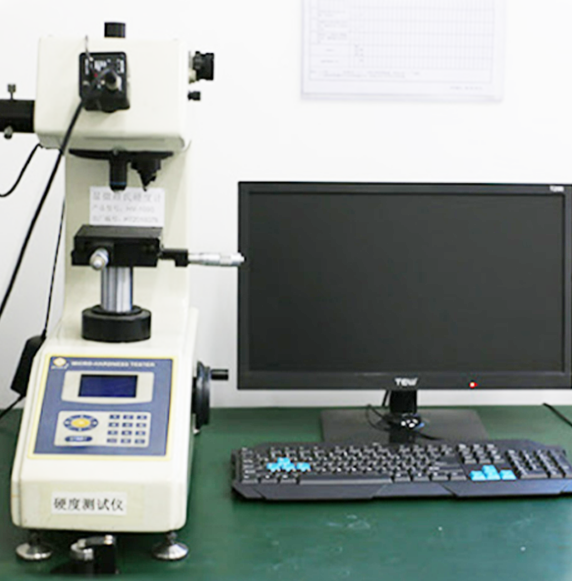
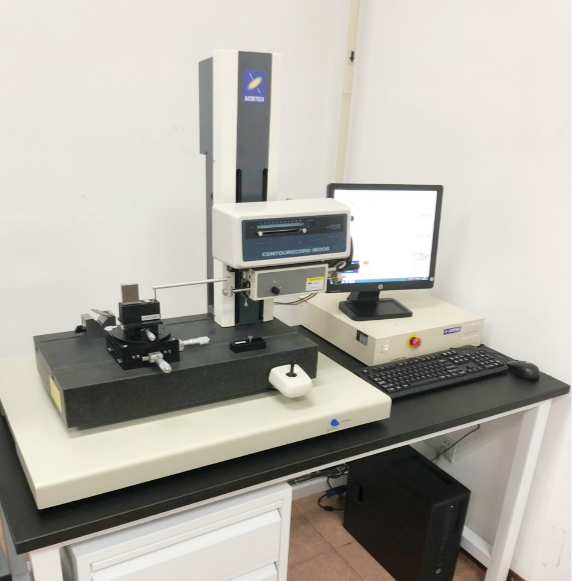
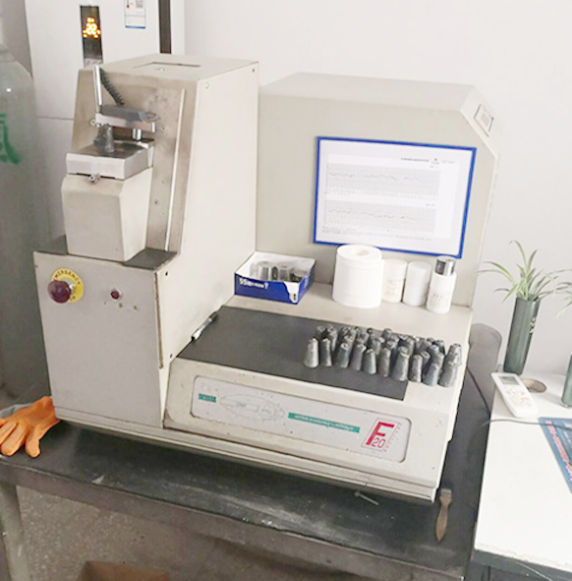
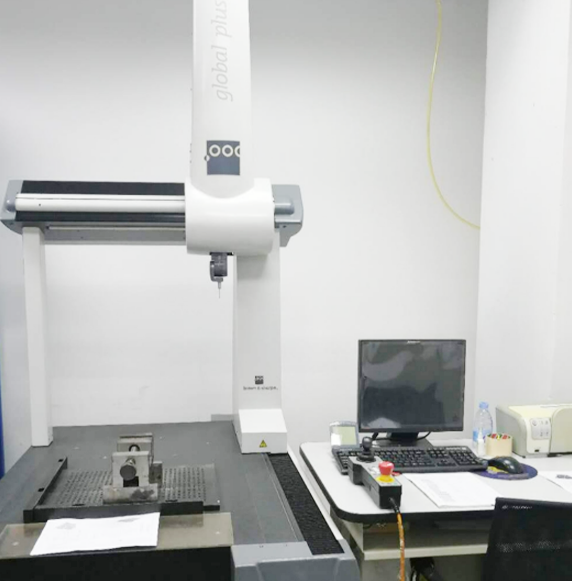
Vickers hardness instrument.
Profile measuring instrument.
Spectrograph instrument.
Three coordinate instrument.
Shipment Picture
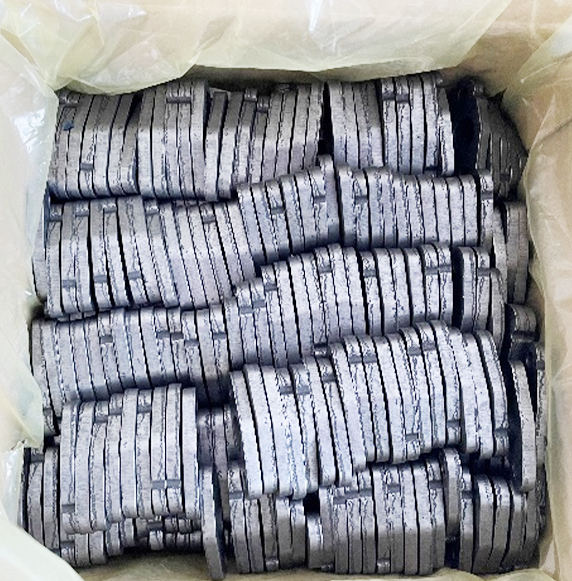
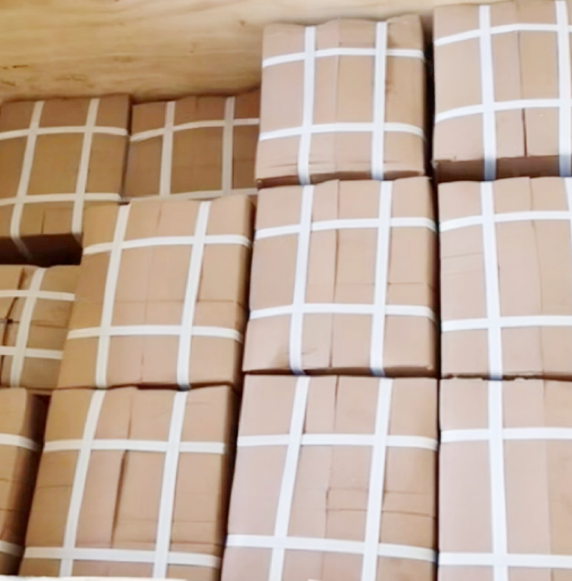
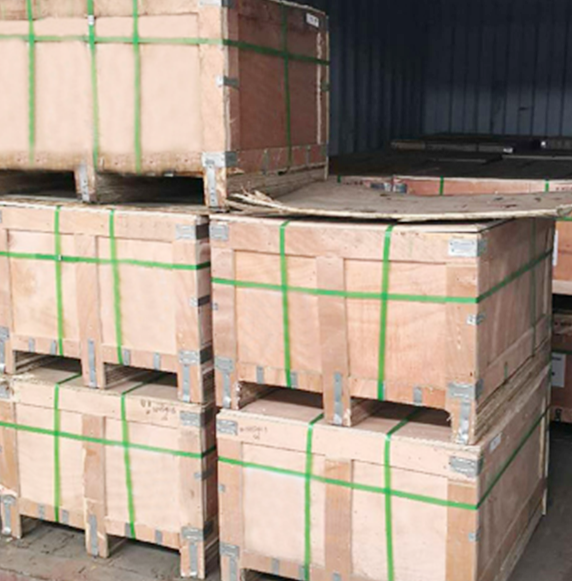
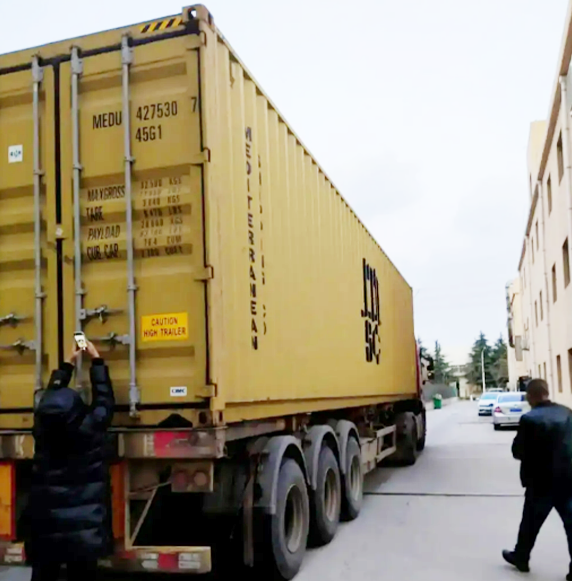
Production Process
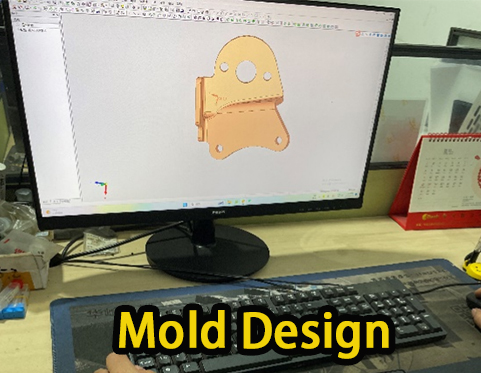
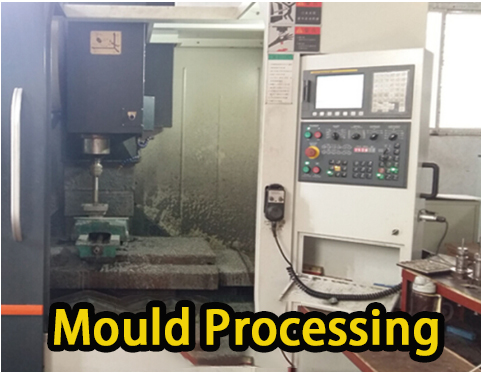
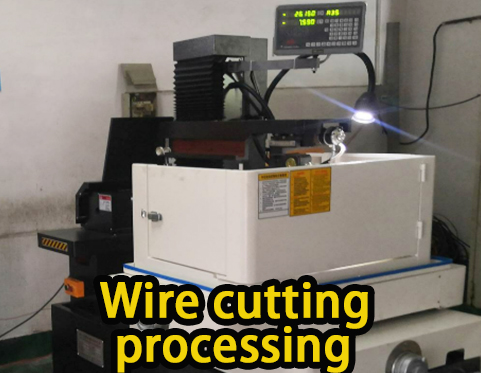
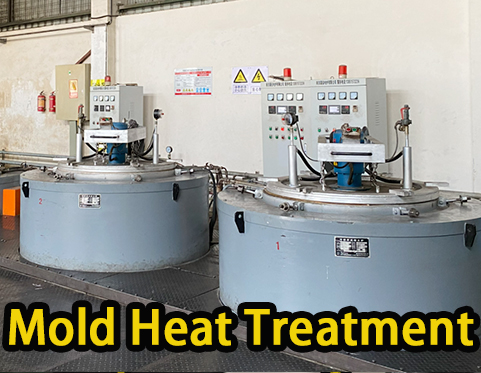
01. Mold design
02. Mould Processing
03. Wire cutting processing
04. Mold heat treatment
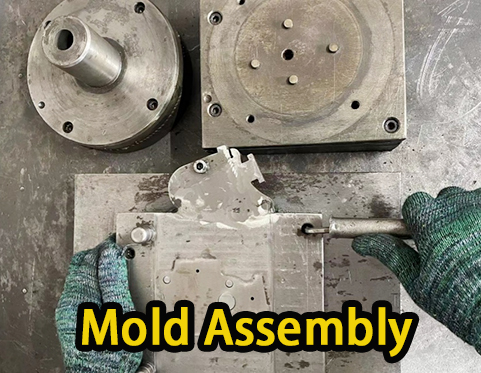
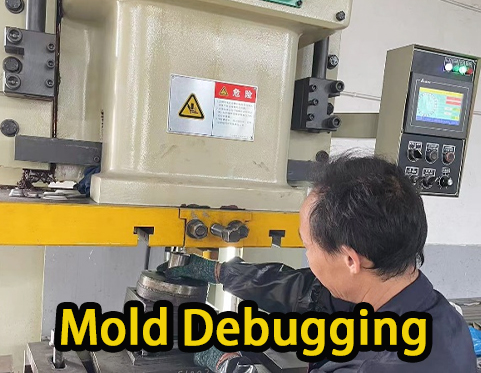
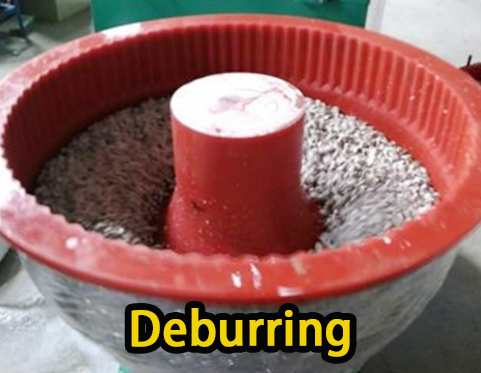

05. Mold assembly
06. Mold debugging
07. Deburring
08. electroplating
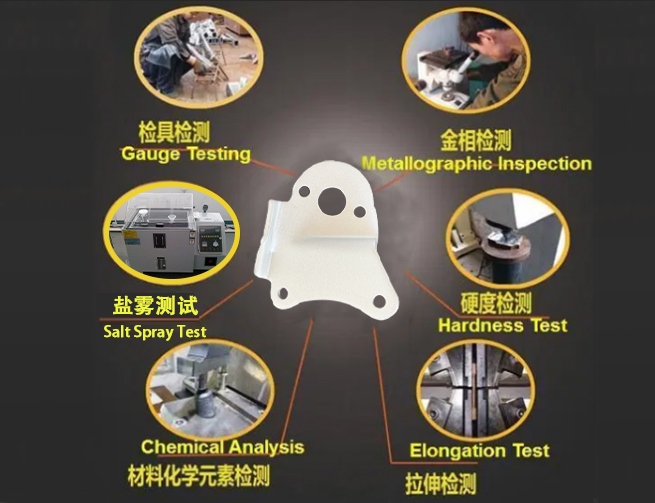
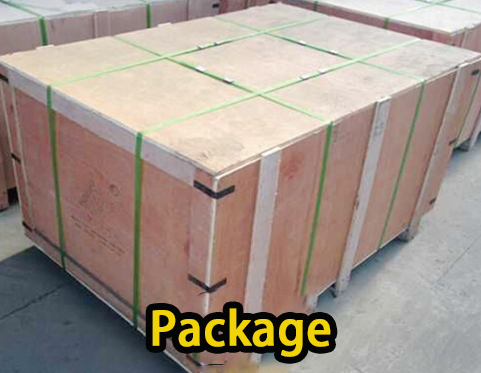
09. Product Testing
10. Package
Oxidation process of metal stamping parts
The following steps are often included in the oxidation process:
1. Raw material feeding: Use pipes to provide the raw materials to the reactor in order to maintain the proper balance of raw materials within.
2. Reaction: To carry out the oxidation reaction, add oxygen to the reactor and regulate the reaction parameters (such as temperature, pressure, and reaction time).
3. Product separation: Use an air cooler to chill the reacted product, turn it from a gaseous state into a liquid or solid form, and then use a separator to separate the products originating from various components.
4. Purification: To ensure that the reaction product reaches the necessary purity, purify it.
5. Packaging: After the products are purified, they are packaged in accordance with guidelines and standards before being either sold to clients or sent on to the next stage of processing.
In certain specialized applications, like semiconductor wafer fabrication, the oxidation process additionally includes applying heat energy and oxidants (such oxygen and water) to the silicon substrate in order to generate a silicon dioxide (SiO2) coating. This oxide film serves as an anti-etching layer to shield the wafer from inadvertent etching during the etching process, stops diffusion during the ion implantation process, and stops leakage current from passing across circuits.
OUR SERVICE
1. Professional R&D team - Our engineers provide unique designs for your products to support your business.
2. Quality Supervision Team - All products are strictly tested before being sent to ensure that all products run well.
3. Efficient logistics team - customized packaging and timely tracking ensure safety until you receive the product.
4. Independent after-sales team-providing timely professional services to customers 24 hours a day.
5. Professional sales team - the most professional knowledge will be shared with you to help you do business better with customers.