Elevator Parts Lift T Type Guide Rails Elevator Guide Rail
Description
Product Type | customized product | |||||||||||
One-Stop Service | Mold development and design-submit samples-batch production-inspection-surface treatment-packaging-delivery. | |||||||||||
Process | stamping,bending,deep drawing,sheet metal fabrication,welding,laser cutting etc. | |||||||||||
Materials | carbon steel,stainless steel,aluminum,copper,galvanized steel etc. | |||||||||||
Dimensions | according to customer's drawings or samples. | |||||||||||
Finish | Spray painting, electroplating, hot-dip galvanizing, powder coating, electrophoresis, anodizing, blackening, etc. | |||||||||||
Application Area | Auto parts, agricultural machinery parts, engineering machinery parts, construction engineering parts, garden accessories, environmentally friendly machinery parts, ship parts, aviation parts, pipe fittings, hardware tool parts, toy parts, electronic parts, etc. |
Process introduction
The manufacturing process of elevator guide rails is a complex process involving multiple links. The following process flow is briefly introduced:
1. Material preparation:
The main raw material of elevator guide rails is high-quality carbon structural steel. Choose the right steel material to ensure the strength and durability of your guide rails.
Steel needs to be pre-treated, including degreasing, cleaning, pickling, etc., to remove surface impurities and oxide layers.
2. Mold making:
According to the design drawings, make the mold of the guide rail. The accuracy and quality of the mold directly affect the forming accuracy and surface quality of the guide rail.
3. Heat treatment:
The guide rail is heat treated under high temperature conditions to change its structure and performance. The heat treatment process may include steps such as tempering, quenching, and normalizing.
4. Forming processing:
Using injection molding, casting or other processes, pre-treated steel is placed into a mold and formed. Ensure the dimensional accuracy, surface finish and uniformity of the metal structure of the mold.
5. Machining:
Precision turning: The guide rail is turned on a precision lathe to ensure the shape accuracy, surface quality and position tolerance of the guide rail.
Grinding process: Grind the guide rail through grinding wheels, superhard grinding heads and other tools to control dimensional tolerances, positional tolerances and surface roughness.
Grinding and polishing: Grind and polish the ground guide rail to improve the surface finish and flatness.
6. Welding process:
Welding is a critical step in joining the various parts of the rail together. During the welding process, the welding temperature, time and technology need to be controlled to ensure the firmness of the welding points and the overall quality of the guide rail.
7. Surface treatment:
The guide rails are surface treated to increase their corrosion and wear resistance and extend their service life. Common surface treatment methods include hot dip galvanizing and spraying. Hot-dip galvanizing is to put the guide rail into molten zinc liquid for galvanizing, which can effectively prevent oxidation corrosion; spray coating is to spray a special coating on the surface of the guide rail to prevent corrosion and reduce friction.
8. Inspection and testing:
Conduct comprehensive quality inspection on the manufactured guide rails, including dimensional measurement, appearance inspection, material performance testing, etc., to ensure that they meet the design requirements.
9. Packaging and storage:
Pack qualified rails to prevent damage or contamination during transportation and storage.
Guide rails should be stored in a dry, ventilated environment to avoid moisture and corrosion.
Specific manufacturing processes may vary due to different materials, design requirements and manufacturing standards. During the actual manufacturing process, adjustments and optimization should be made according to specific conditions to ensure the best quality and performance of the elevator guide rails. At the same time, relevant safety operating procedures should be strictly followed during the manufacturing process to ensure the safety of operators.
Quality management
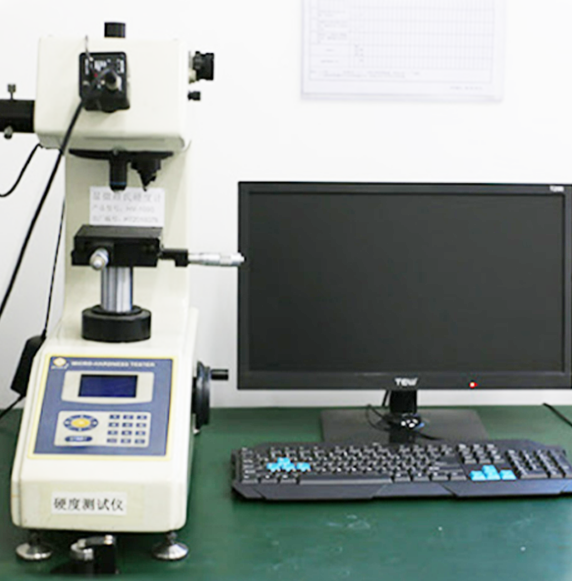
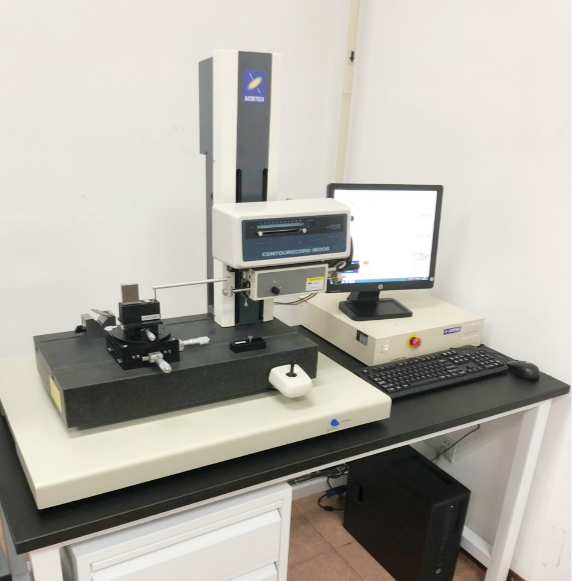
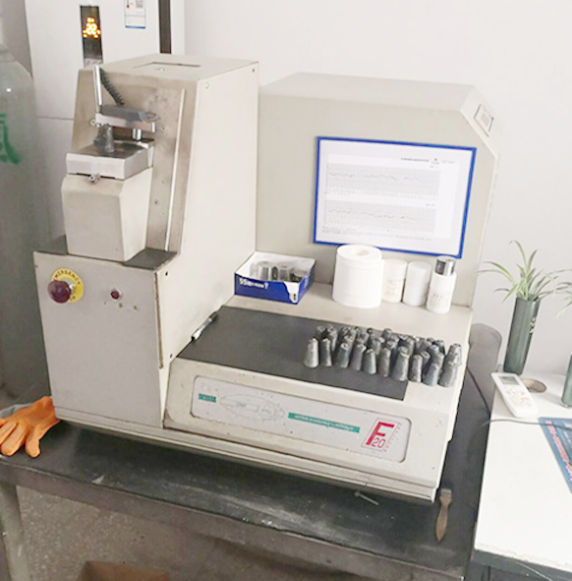
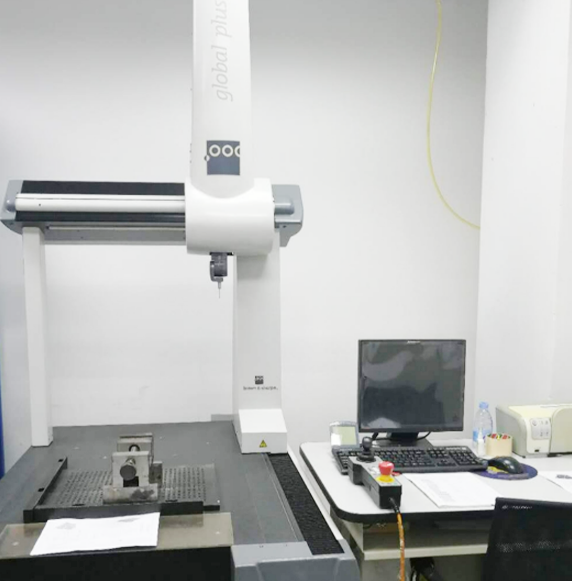
Vickers hardness instrument.
Profile measuring instrument.
Spectrograph instrument.
Three coordinate instrument.
Shipment Picture
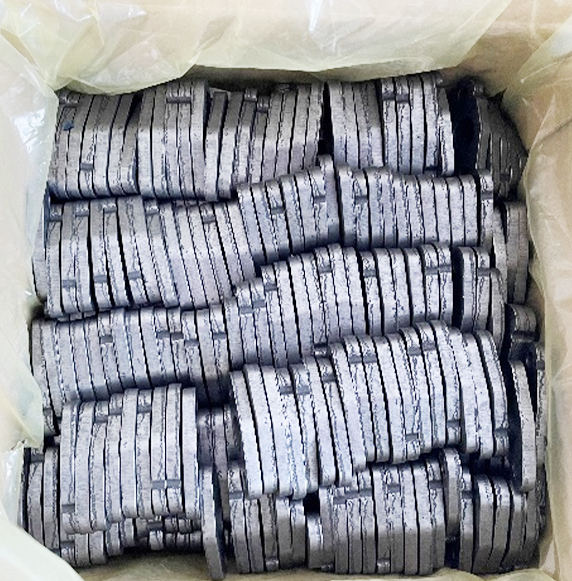
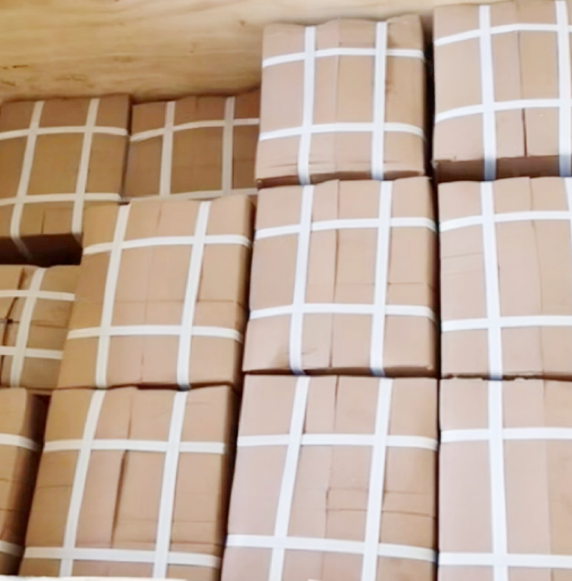
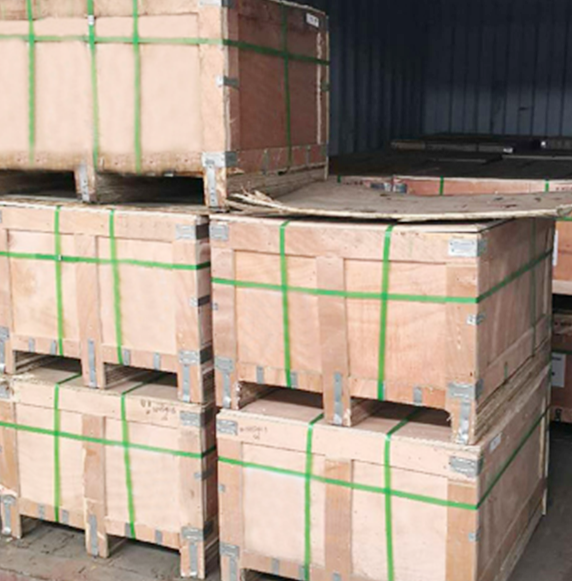
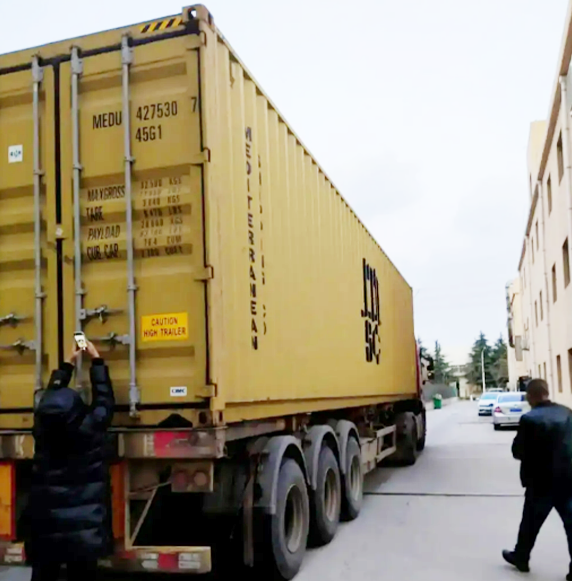
Production Process
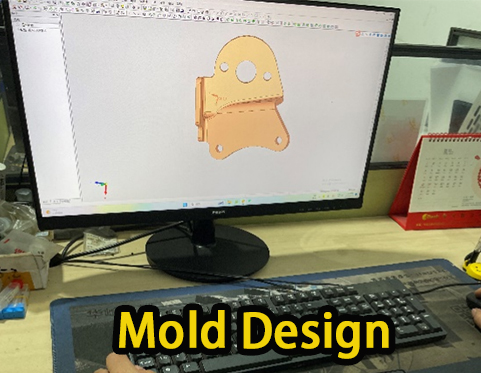
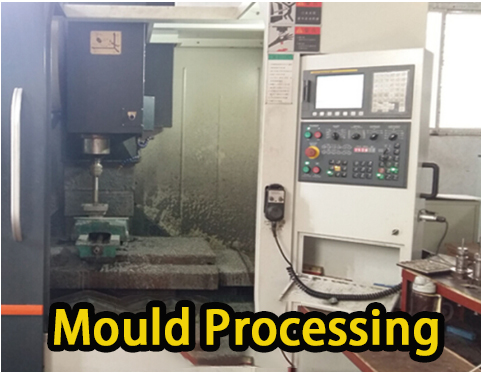
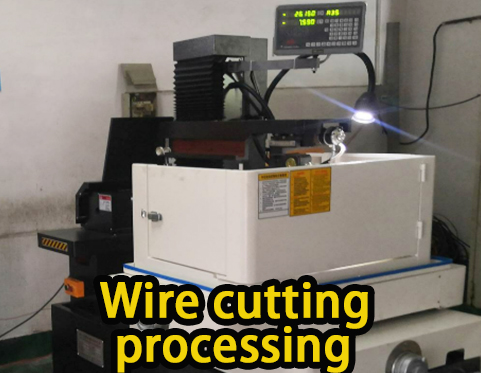
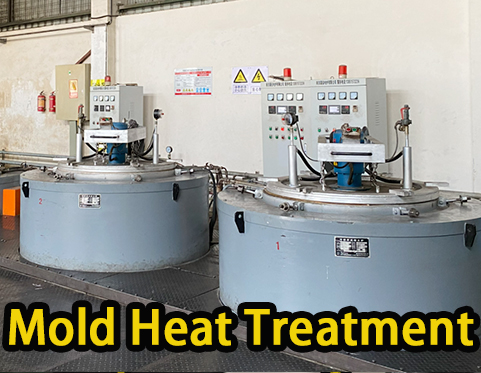
01. Mold design
02. Mould Processing
03. Wire cutting processing
04. Mold heat treatment
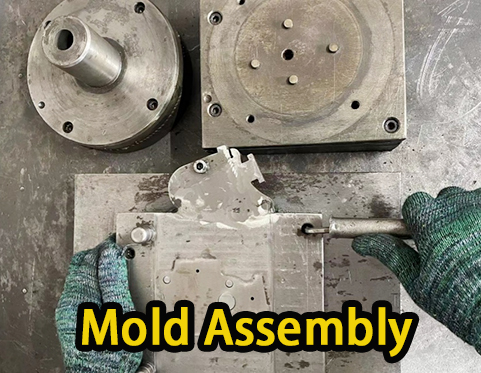
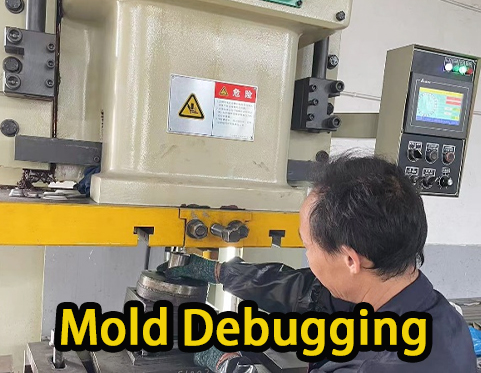
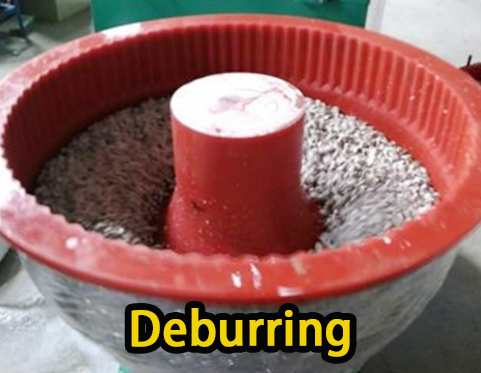

05. Mold assembly
06. Mold debugging
07. Deburring
08. electroplating
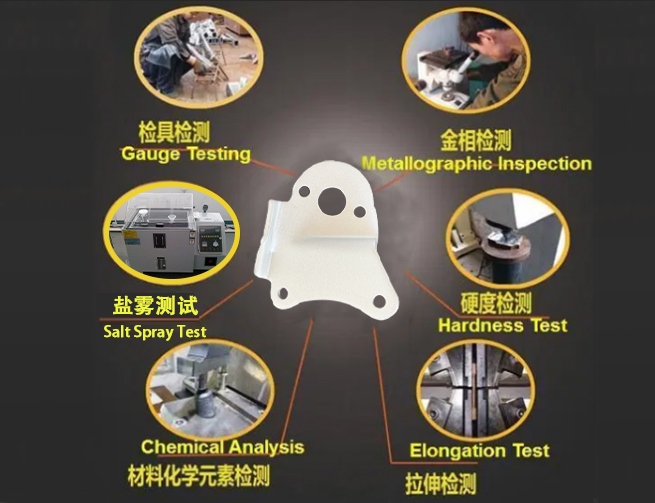
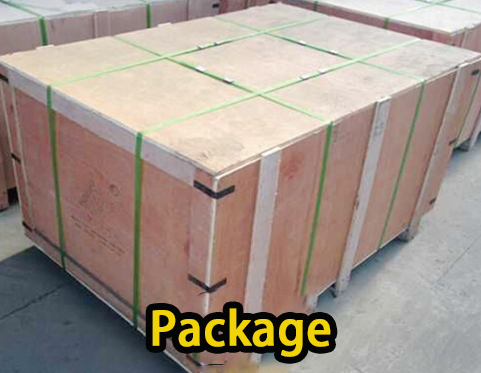
09. Product Testing
10. Package
Our service
1. Expert R&D team: To help your business, our engineers create innovative designs for your items.
2. Quality Supervision Team: Every product is rigorously checked to make sure it functions properly before it is shipped.
3. A proficient logistics crew - personalized packing and prompt tracking guarantee the product's safety till it reaches you.
4. A self-contained post-purchase staff that offers clients prompt, expert assistance around-the-clock.
A proficient sales crew will impart the most expert knowledge to you to enable you to conduct company with customers more effectively.
FAQ
Q: Are you a trading company or manufacturer?
A: We are manufacturer.
Q: How to get the quote?
A: Please send your drawings (PDF, stp, igs, step...) to us by email , and tell us the material, surface treatment and quantities, then we will make a quotation to you.
Q: Can I order just 1 or 2 pcs for testing?
A: Yes, of course.
Q. Can you produce according to the samples?
A: Yes, we can produce by your samples.
Q: How long is your delivery time?
A: 7~ 15 days, depends on the order quantities and product process.
Q. Do you test all your goods before delivery?
A: Yes, we have 100% test before delivery.
Q: How do you make our business long-term and good relationship?
A:1. We keep good quality and competitive price to ensure our customers benefit ;
2. We respect every customer as our friend and we sincerely do business and make friends with them, no matter where they come from.