Elevator guide rail non-standard hollow guide rail pressure plate
Description
Product Type | customized product | |||||||||||
One-Stop Service | Mold development and design-submit samples-batch production-inspection-surface treatment-packaging-delivery. | |||||||||||
Process | stamping,bending,deep drawing,sheet metal fabrication,welding,laser cutting etc. | |||||||||||
Materials | carbon steel,stainless steel,aluminum,copper,galvanized steel etc. | |||||||||||
Dimensions | according to customer's drawings or samples. | |||||||||||
Finish | Spray painting, electroplating, hot-dip galvanizing, powder coating, electrophoresis, anodizing, blackening, etc. | |||||||||||
Application Area | Auto parts, agricultural machinery parts, engineering machinery parts, construction engineering parts, garden accessories, environmentally friendly machinery parts, ship parts, aviation parts, pipe fittings, hardware tool parts, toy parts, electronic parts, etc. |
Product technology
The manufacturing process of elevator guide rail pressure plates is a precise process involving multiple links to ensure that the quality and performance of the pressure plates meet the requirements of the elevator system. The following is the basic process flow for making elevator guide rail pressure plates:
1. Material selection and preparation:
- According to the design requirements of the elevator guide rail pressure plate, select appropriate materials, such as carbon structural steel, stainless steel or composite materials, etc.
- Check the quality of selected materials to ensure they comply with relevant standards and specifications.
2. Cutting and blanking:
- Use professional cutting equipment, such as laser cutting machines or CNC punch presses, to accurately cut raw materials according to design drawings.
- Ensure that the size and shape of the blanks are accurate to meet the needs of subsequent processing.
3. Forming processing:
- According to the design requirements, perform shaping processing on the cut materials, such as bending, stamping, etc.
- Use special molds and tools to ensure that the shape and size of the platen meet the design requirements.
4. Welding and connection:
- If the pressure plate needs to be composed of multiple parts, welding or joining operations are required.
- Choose appropriate welding methods, such as arc welding, laser welding, etc., to ensure reliable welding quality.
5. Surface treatment:
- Perform necessary surface treatment on the pressure plate, such as grinding, spraying, etc., to improve its appearance quality and corrosion resistance.
- Hot dip galvanizing or other anti-corrosion treatments can also be carried out if required.
6. Inspection and testing:
- Conduct quality inspection on the completed elevator guide rail pressure plate, including dimensional inspection, appearance inspection, etc.
- Conduct necessary performance tests, such as strength test, wear resistance test, etc., to ensure that the pressure plate meets relevant standards and requirements.
7. Packaging and storage:
- Pack qualified elevator guide rail pressure plates to prevent damage during transportation and storage.
- Store the pressure plate in a dry, ventilated environment to avoid moisture and corrosion.
Specific manufacturing processes may vary due to different materials, design requirements and manufacturing standards. Therefore, during the actual production process, adjustments and optimization should be made according to specific conditions to ensure that the quality and performance of the elevator guide rail pressure plate are optimal. At the same time, we will strictly abide by relevant safety operating procedures during the production process to ensure the safety of operators.
Quality management
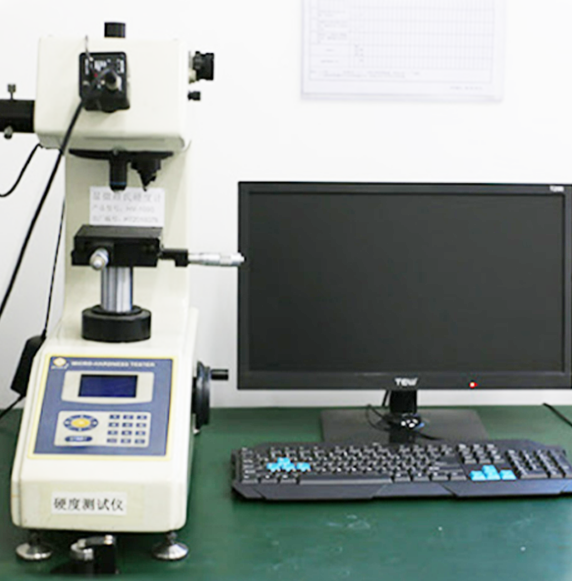
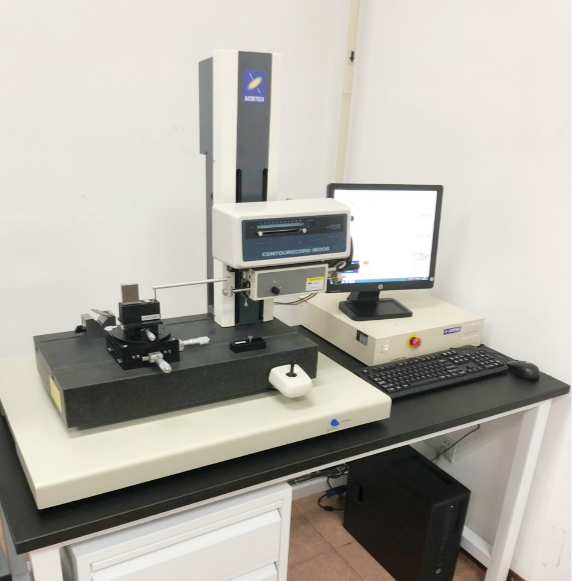
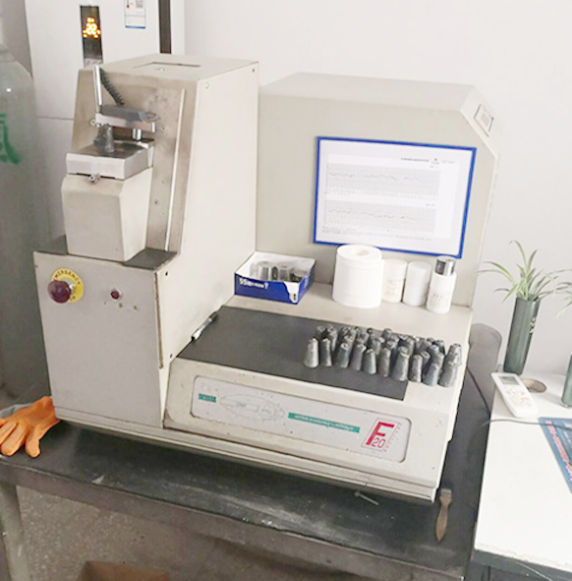
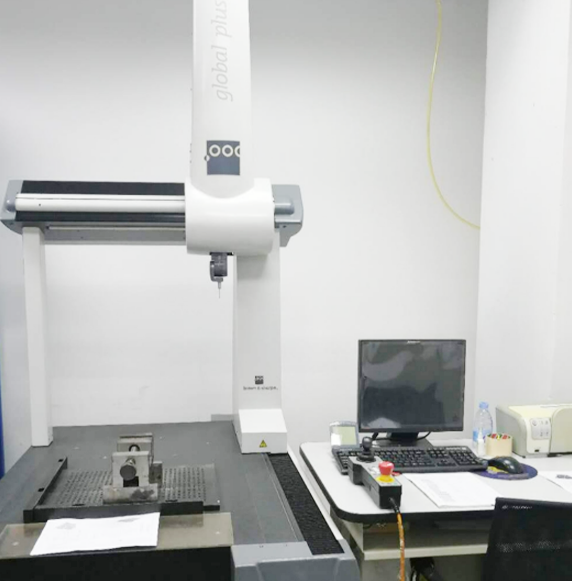
Vickers hardness instrument.
Profile measuring instrument.
Spectrograph instrument.
Three coordinate instrument.
Shipment Picture
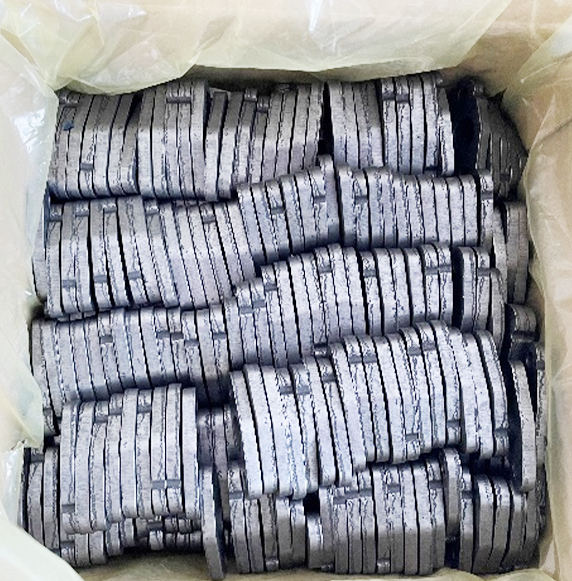
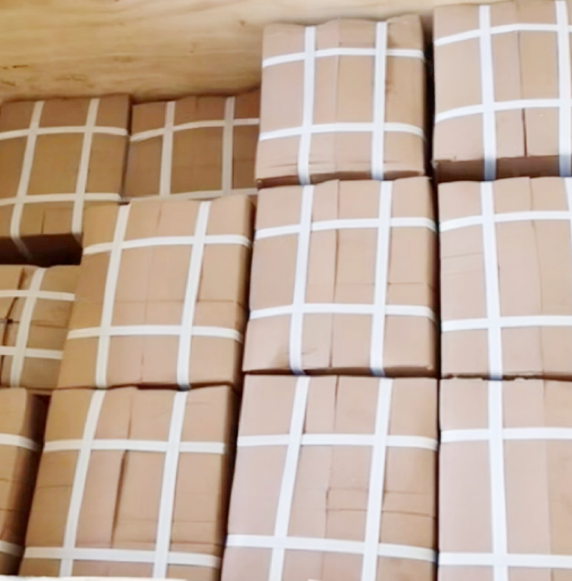
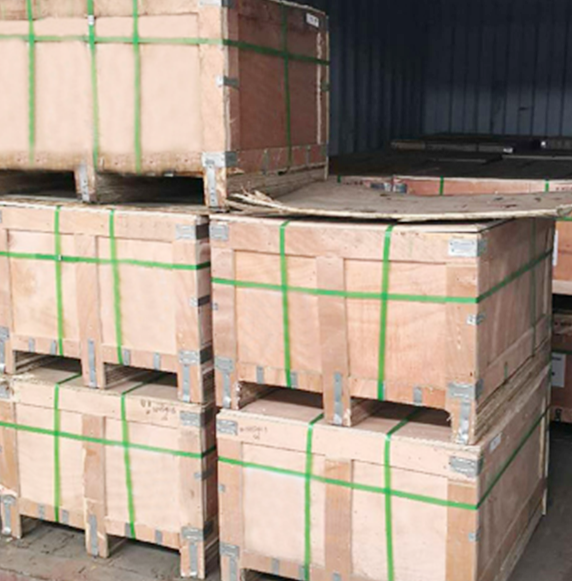
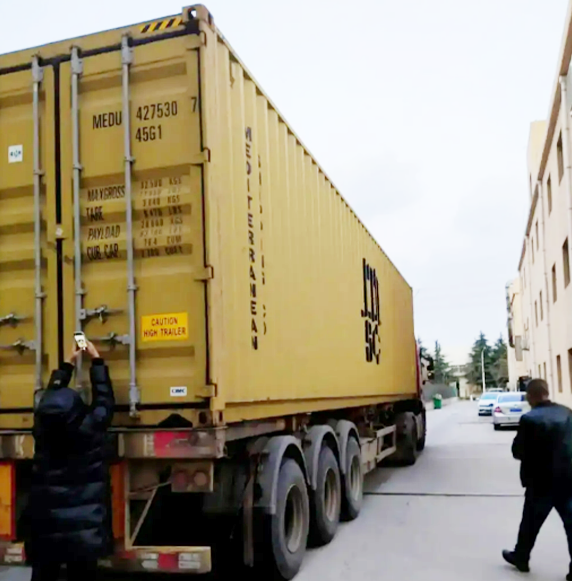
Production Process
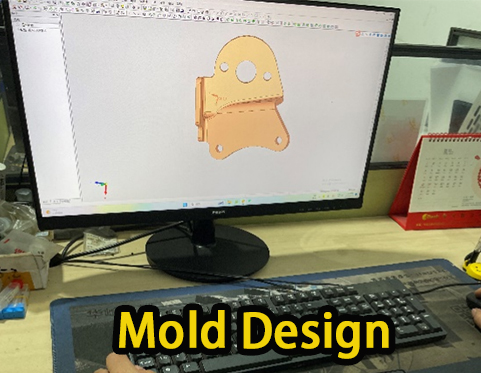
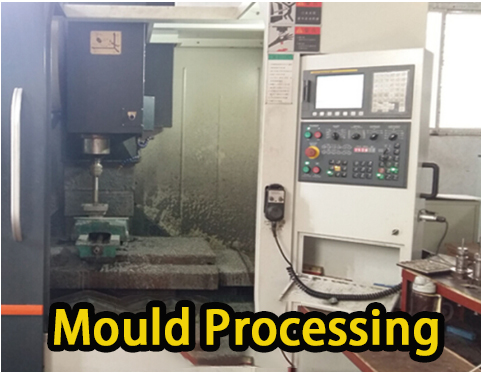
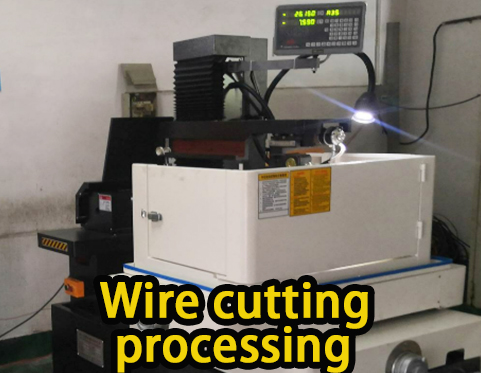
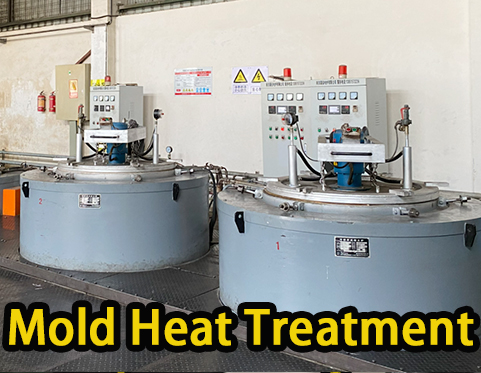
01. Mold design
02. Mould Processing
03. Wire cutting processing
04. Mold heat treatment
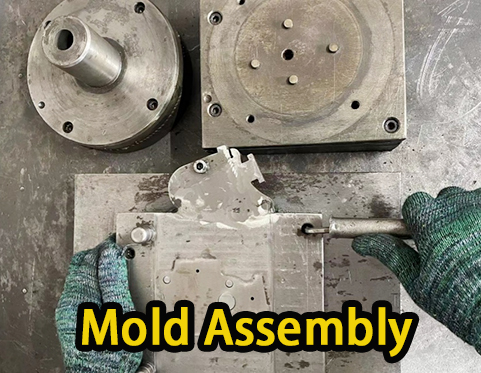
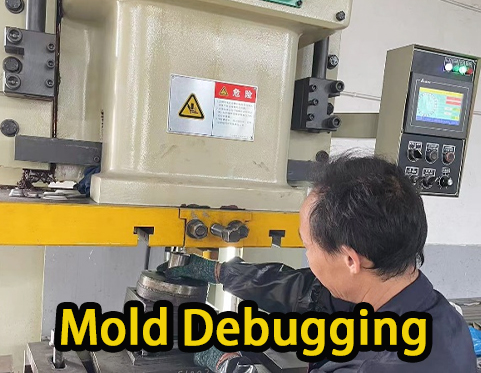
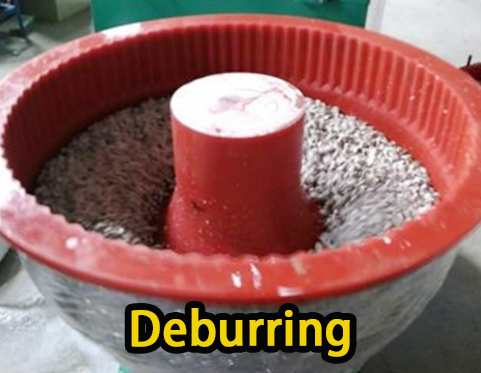

05. Mold assembly
06. Mold debugging
07. Deburring
08. electroplating
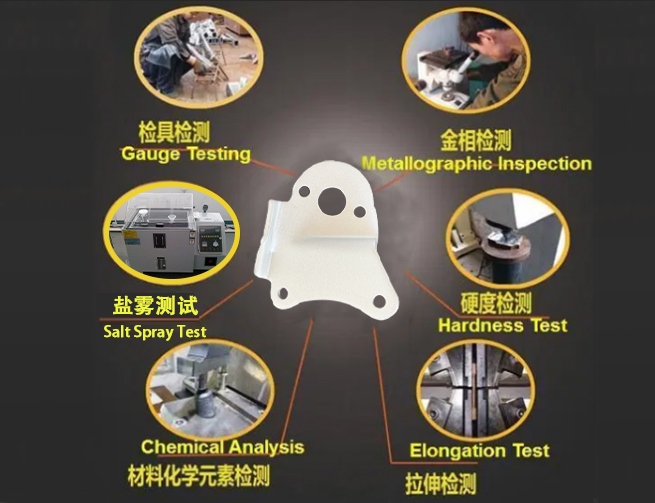
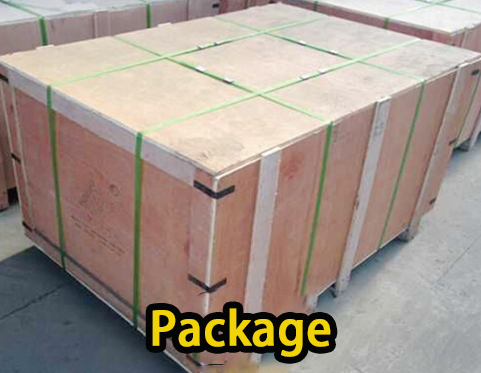
09. Product Testing
10. Package
Precision Metal Forming
Xinzhe Metal Stampings is proud of its capacity to create even the most intricate shapes with dies and tools made in-house.
In the past ten years, we have developed tools to make over 8,000 distinct pieces, including several difficult shapes in addition to some easy ones. Xinzhe Metal Stampings frequently accepts jobs that others have declined because they are too challenging or "impossible" to complete. We provide a variety of secondary services to add to your sheet metal fabrication project in addition to working with a wide range of materials.
One of our more recent additions is a Komatsu Servo Punch Press that is state of the art for precision metal forming operations. This press allows us greater flexibility in relation to the number of operations required to achieve extensive metal forming.
Saving you money by providing innovative, cost-effective precision metal forming solutions is our specialty. It’s no surprise that customers have trusted Xinzhe Metal Stampings for their metal forming needs.
FAQ
Q: Are you a trading company or manufacturer?
A: We are manufacturer.
Q: How to get the quote?
A: Please send your drawings (PDF, stp, igs, step...) to us by email , and tell us the material, surface treatment and quantities, then we will make a quotation to you.
Q: Can I order just 1 or 2 pcs for testing?
A: Yes, of course.
Q. Can you produce according to the samples?
A: Yes, we can produce by your samples.
Q: How long is your delivery time?
A: 7~ 15 days, depends on the order quantities and product process.
Q. Do you test all your goods before delivery?
A: Yes, we have 100% test before delivery.
Q: How do you make our business long-term and good relationship?
A:1. We keep good quality and competitive price to ensure our customers benefit ;
2. We respect every customer as our friend and we sincerely do business and make friends with them, no matter where they come from.