Elevator device door head mounting bracket elevator accessories
Description
Product Type | customized product | |||||||||||
One-Stop Service | Mold development and design-submit samples-batch production-inspection-surface treatment-packaging-delivery. | |||||||||||
Process | stamping,bending,deep drawing,sheet metal fabrication,welding,laser cutting etc. | |||||||||||
Materials | carbon steel,stainless steel,aluminum,copper,galvanized steel etc. | |||||||||||
Dimensions | according to customer's drawings or samples. | |||||||||||
Finish | Spray painting, electroplating, hot-dip galvanizing, powder coating, electrophoresis, anodizing, blackening, etc. | |||||||||||
Application Area | Auto parts, agricultural machinery parts, engineering machinery parts, construction engineering parts, garden accessories, environmentally friendly machinery parts, ship parts, aviation parts, pipe fittings, hardware tool parts, toy parts, electronic parts, etc. |
Advantags
1. Over ten years of experience in international trade.
2. Offer a one-stop shop for everything from product delivery to mold design.
3. Quick delivery, taking between 30 and 40 days. within a week's supply.
4. Strict process control and quality management (manufacturer and factory with ISO certification).
5. More affordable costs.
6. Skilled: With over a decade of experience, our plant has been stamping sheet metal.
Quality management
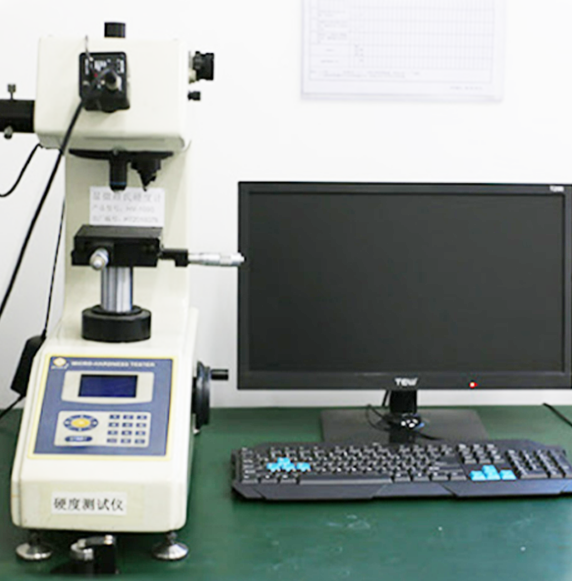
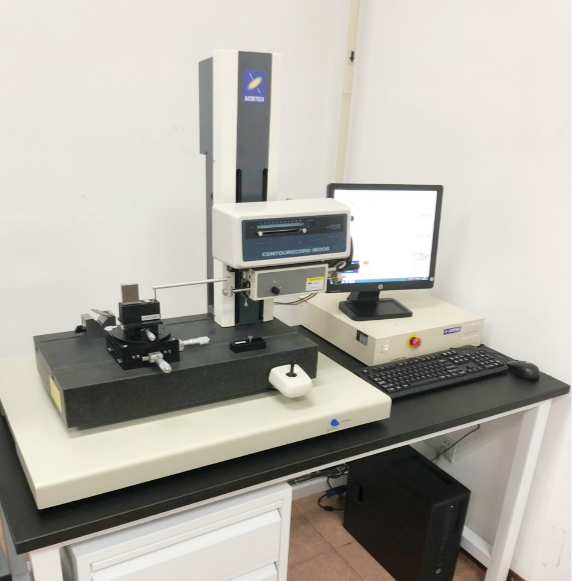
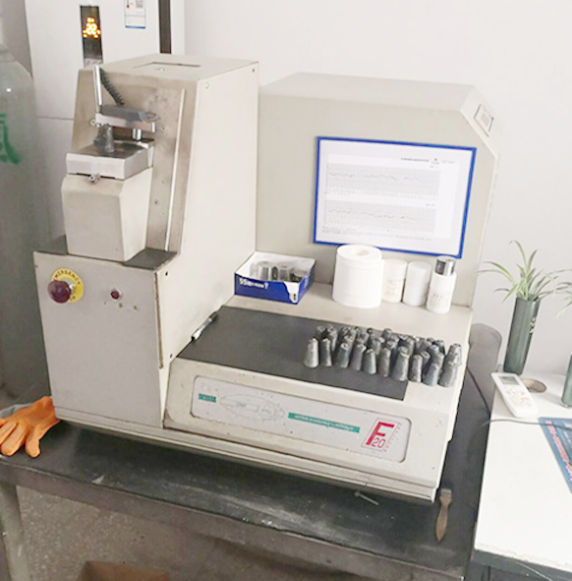
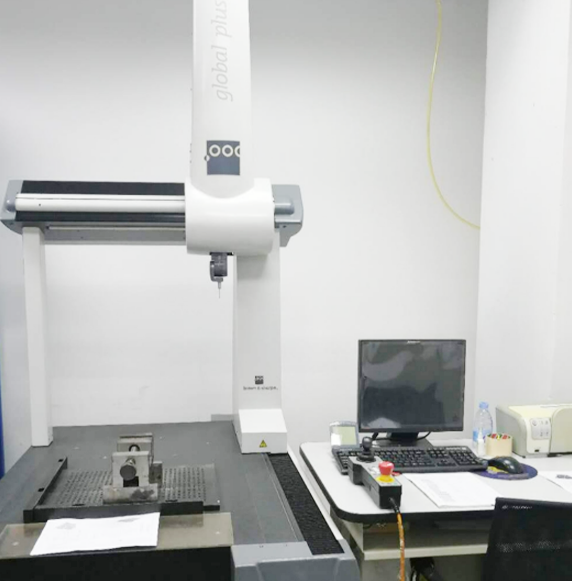
Vickers hardness instrument.
Profile measuring instrument.
Spectrograph instrument.
Three coordinate instrument.
Shipment Picture
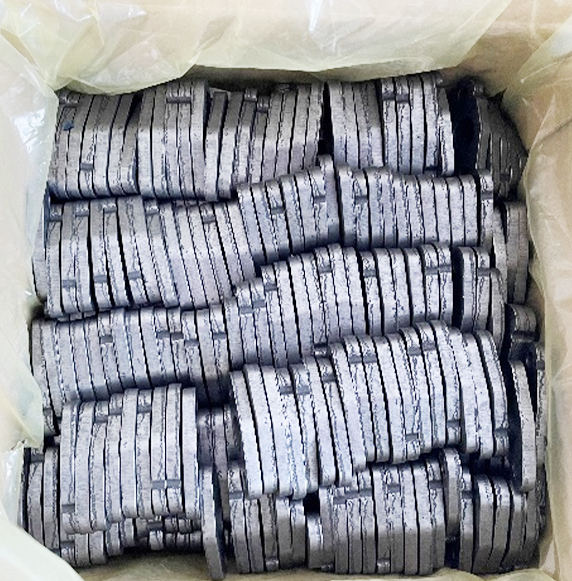
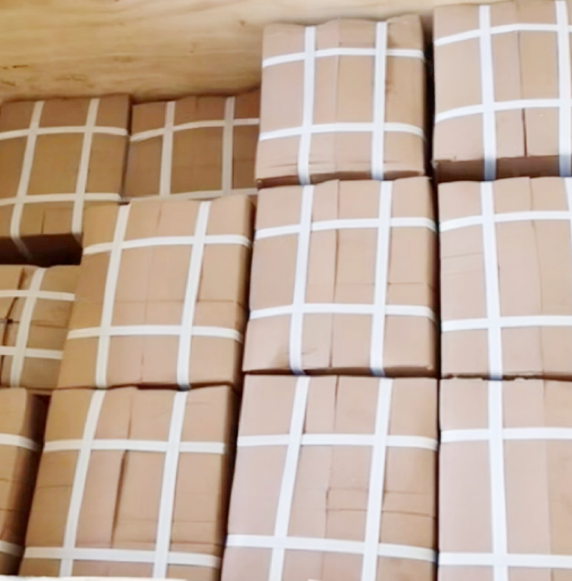
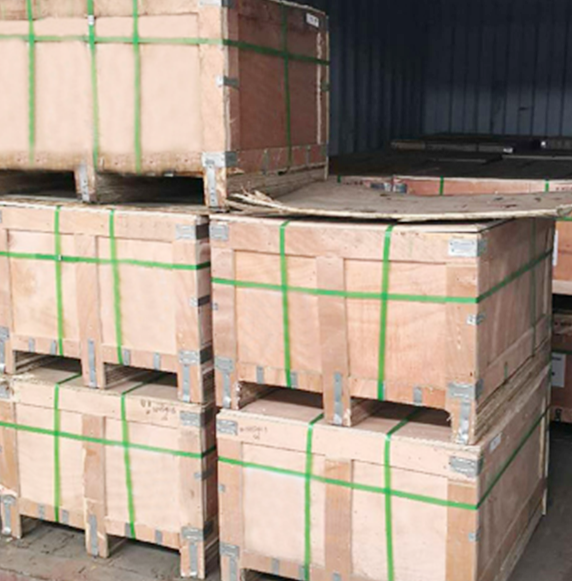
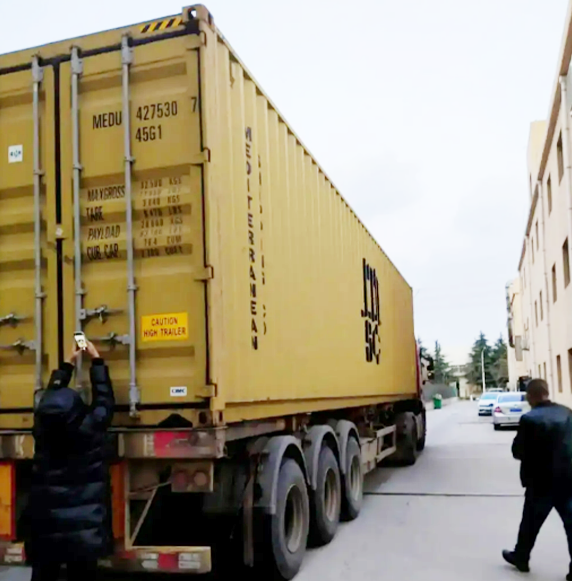
Production Process
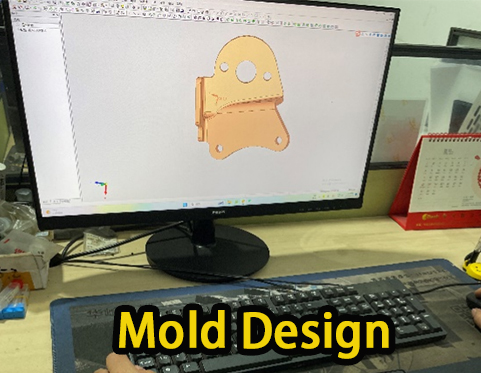
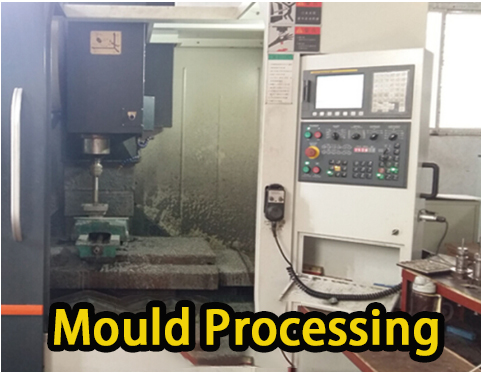
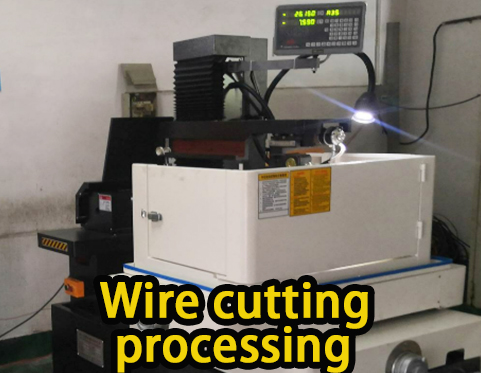
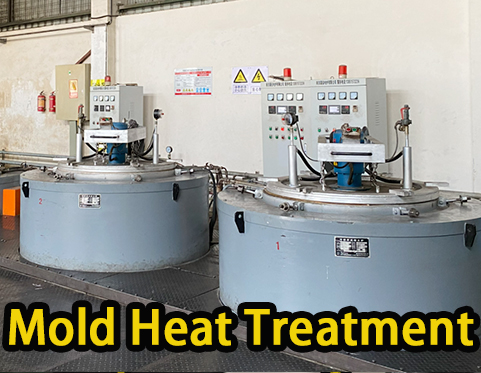
01. Mold design
02. Mould Processing
03. Wire cutting processing
04. Mold heat treatment
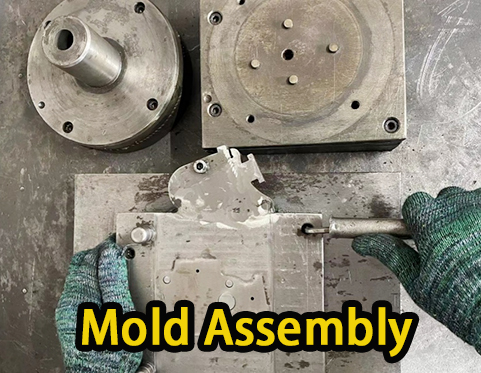
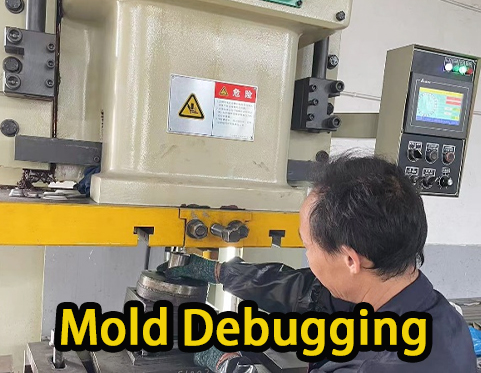
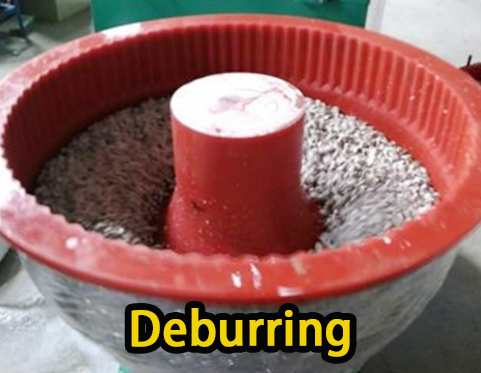

05. Mold assembly
06. Mold debugging
07. Deburring
08. electroplating
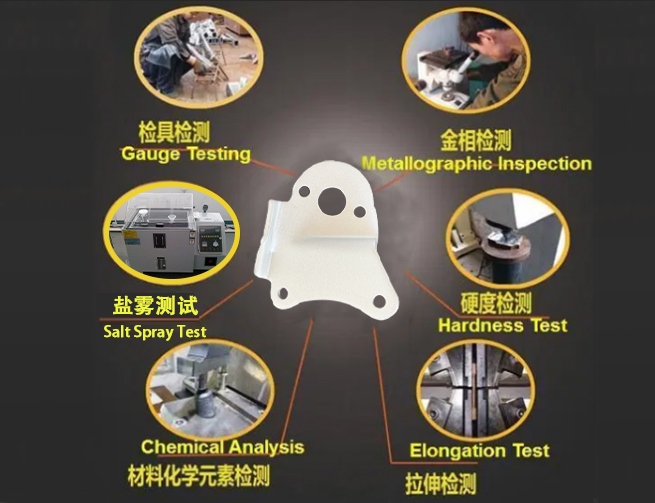
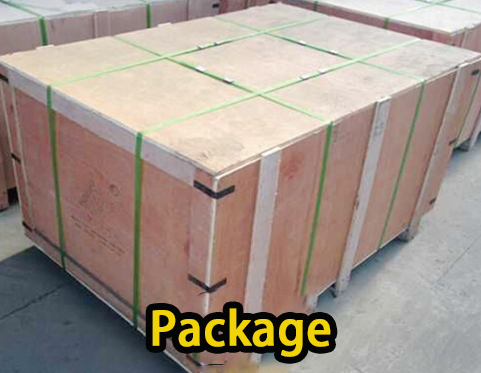
09. Product Testing
10. Package
The Stamping Process
Metal stamping process is an important metal processing method and is widely used in various fields of manufacturing:
1. Definition and principle: Metal stamping process is a processing method that uses pressure to deform metal sheets in a mold. The basic principle is to use punches and dies to exert pressure on metal sheets to cause plastic deformation, thereby obtaining metal parts with the required shape, size and performance.
2. Mold design: Mold is a key part of the metal stamping process, and its design directly affects product quality and production efficiency. Mold design needs to consider the shape, size, accuracy requirements of the product, as well as the performance and deformation rules of the material.
3. Stamping equipment and selection: Stamping equipment mainly includes punches, presses, hydraulic presses, etc. Choosing appropriate stamping equipment requires comprehensive consideration based on factors such as product size, thickness, material, and production batch.
4. Stamping process and classification: Metal stamping process usually includes blanking, punching, bending, deep drawing, trimming and other processes. Depending on different product requirements and material properties, different stamping process combinations can be selected.
5. Process parameters and optimization: Process parameters include stamping speed, pressure, temperature, etc. The selection and optimization of these parameters are of great significance for improving product quality, reducing energy consumption and improving production efficiency.
6. Common defects and solutions: During the metal stamping process, some common defects may occur, such as breaks, uneven plastic deformation, wrinkles, burrs, etc. To address these defects, corresponding solutions need to be taken, such as optimizing mold design, adjusting process parameters, improving material quality, etc.
7. Application fields: Metal stamping technology is widely used in automobiles, electronics, home appliances, aerospace and other fields. It can produce metal parts of various shapes and sizes to meet the needs of different industries.
Metal stamping process is an important metal processing method with wide application prospects. By continuously optimizing mold design, process parameters and production processes, product quality can be improved, production costs reduced, and changing market demands met.
FAQ
1.Q: What is the payment method?
A: We accept TT (Bank Transfer), L/C.
(1. For total amount under US$3000, 100% in advance.)
(2. For total amount above US$3000, 30% in advance, the rest against the copy document.)
2.Q:Where is your factory located?
A:Our factorty is located in Ningbo,Zhejiang.
3.Q:Do you provide free samples?
A:Usually we do not provide free samples. There is a sample cost which can be refund after you place order.
4.Q:What do you usually shipped through?
A:Air freight, Sea freight, express are the most way of shipment due to small weight and size for precise products.
5.Q:I don’t have drawing or picture available for custom products, could you design it?
A:Yes, we can make the best suitable design in accordance with your application.