Customized precision bracket stainless steel sheet metal stamping parts
Description
Product Type | customized product | |||||||||||
One-Stop Service | Mold development and design-submit samples-batch production-inspection-surface treatment-packaging-delivery. | |||||||||||
Process | stamping,bending,deep drawing,sheet metal fabrication,welding,laser cutting etc. | |||||||||||
Materials | carbon steel,stainless steel,aluminum,copper,galvanized steel etc. | |||||||||||
Dimensions | according to customer's drawings or samples. | |||||||||||
Finish | Spray painting, electroplating, hot-dip galvanizing, powder coating, electrophoresis, anodizing, blackening, etc. | |||||||||||
Application Area | Auto parts, agricultural machinery parts, engineering machinery parts, construction engineering parts, garden accessories, environmentally friendly machinery parts, ship parts, aviation parts, pipe fittings, hardware tool parts, toy parts, electronic parts, etc. |
Capabilities
In order to satisfy the needs of the customer, Xinzhe offers a full-service in-house tool room for the design, engineering, and production of various kinds of metal stamping dies, including compound, progressive, draw, and prototype tooling.
Most importantly, our economical, high-quality metal stamping tools reduce production and operating expenses. For the duration of the stamping projects, we also maintain and repair all of our customers' dies at no additional expense to them.
1.Quick tool adjustments to account for changes in engineering.
2. Superior quality equipment.
3. proficiency in tool design.
4. Highly qualified and proficient tooling engineers possessing solid stamping knowledge.
5. Using Advanced Wire EDM, you can precisely and affordably cut your parts.
Quality management
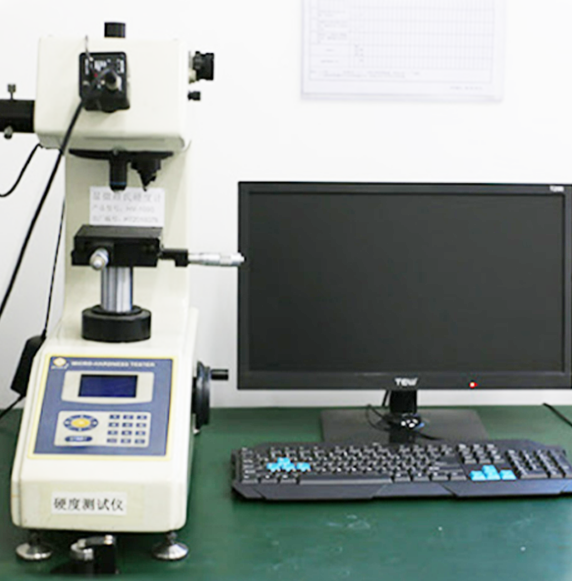
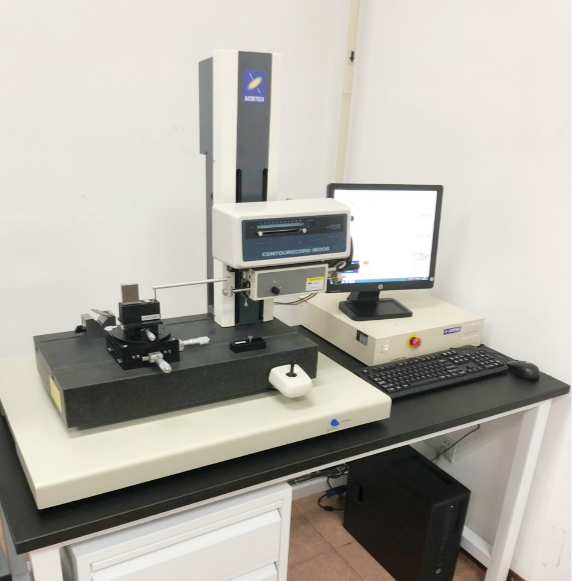
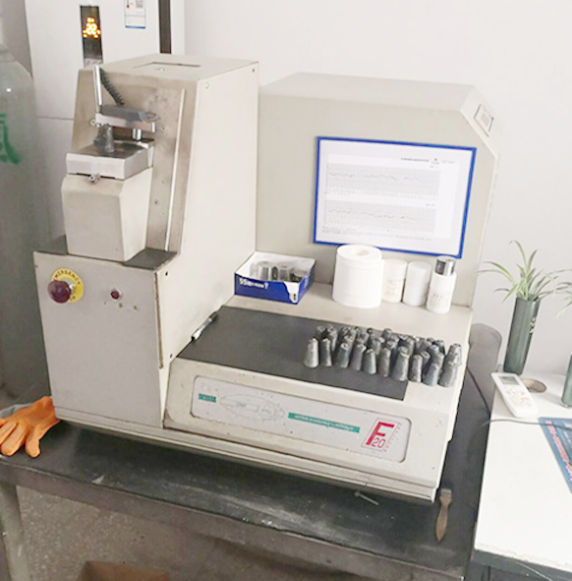
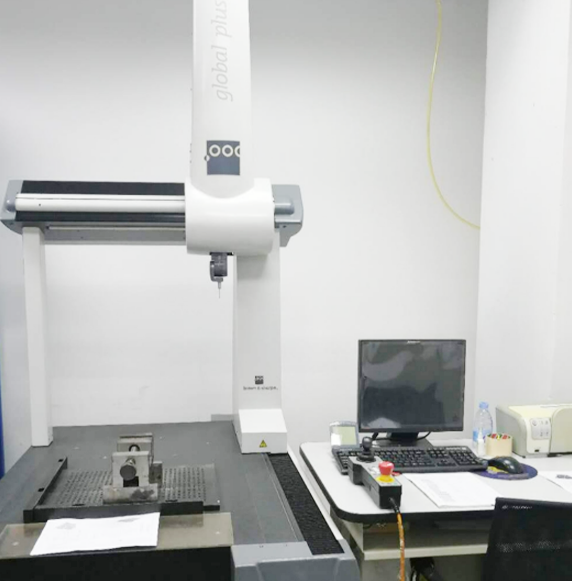
Vickers hardness instrument.
Profile measuring instrument.
Spectrograph instrument.
Three coordinate instrument.
Shipment Picture
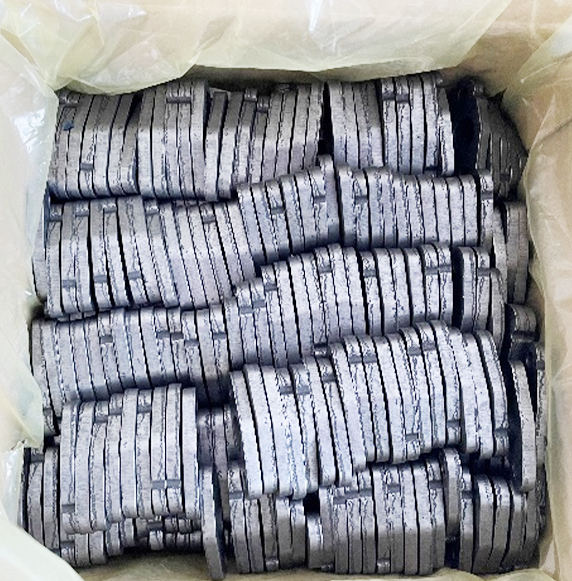
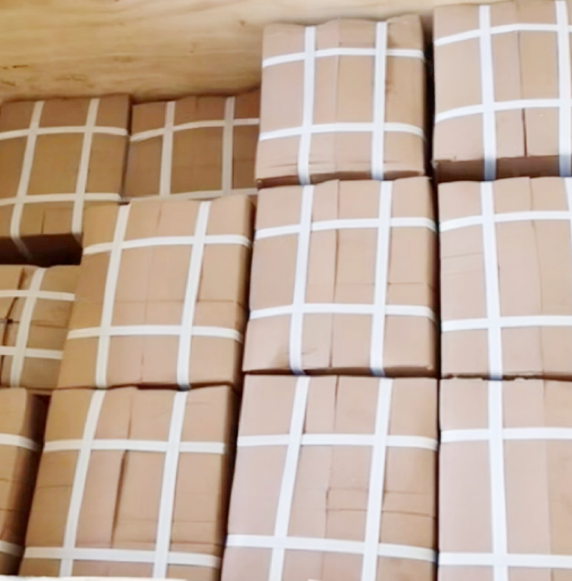
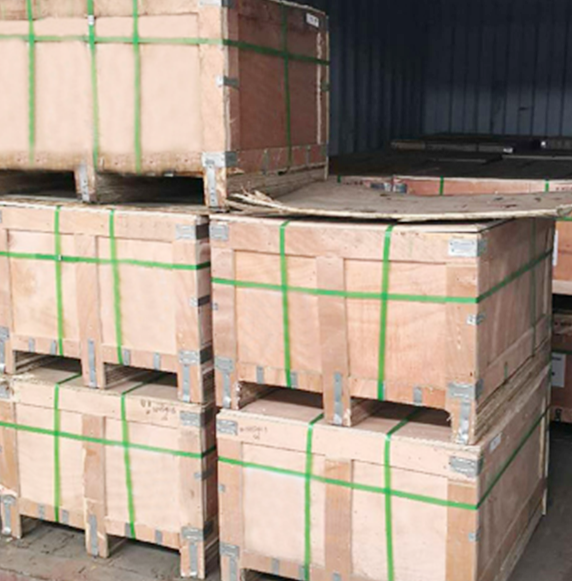
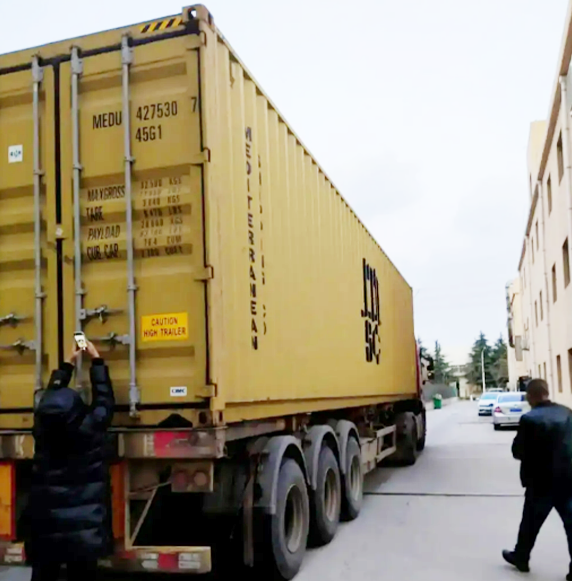
Production Process
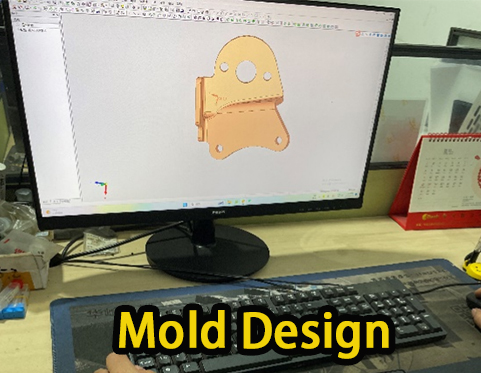
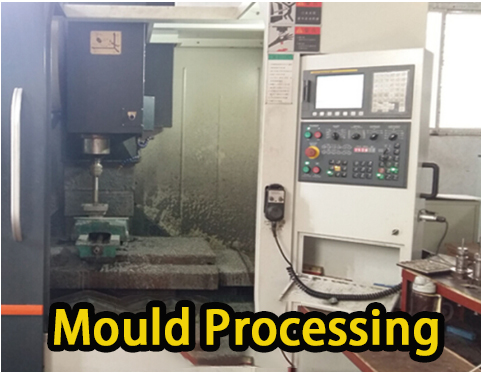
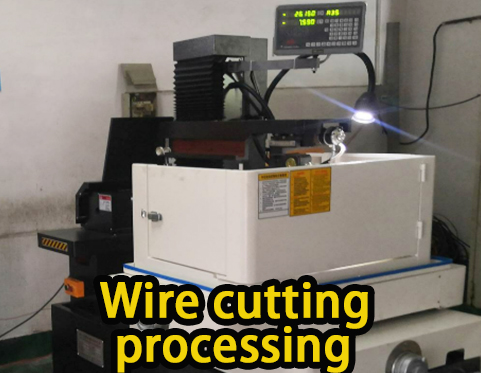
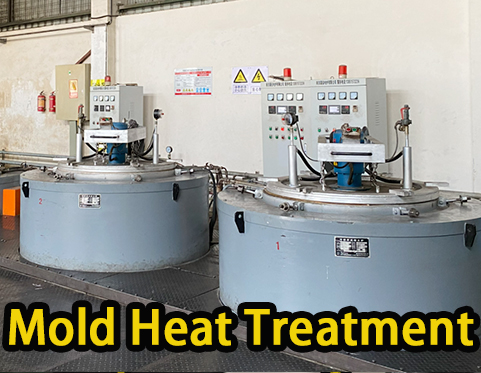
01. Mold design
02. Mould Processing
03. Wire cutting processing
04. Mold heat treatment
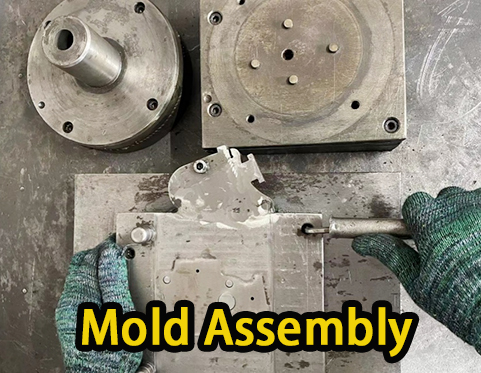
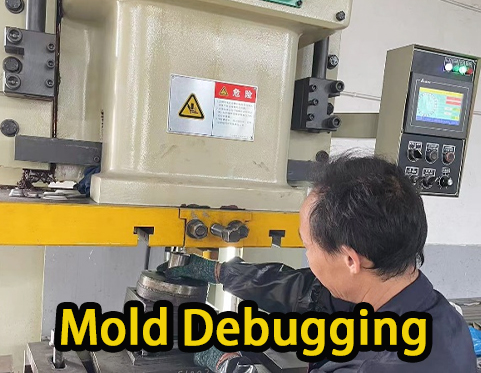
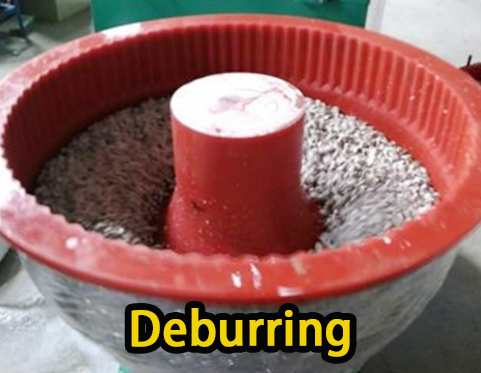

05. Mold assembly
06. Mold debugging
07. Deburring
08. electroplating
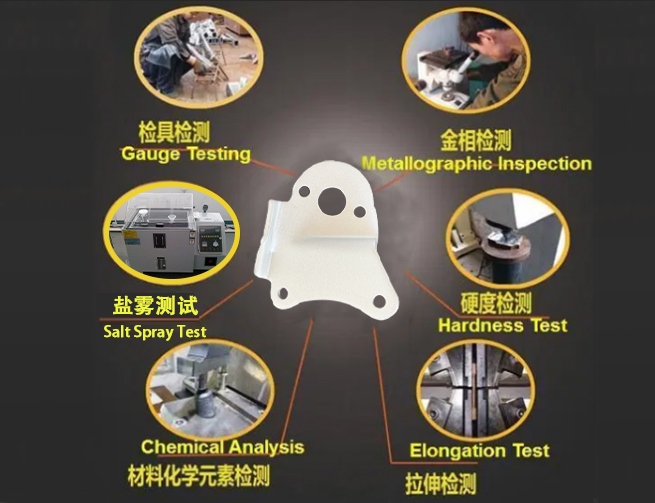
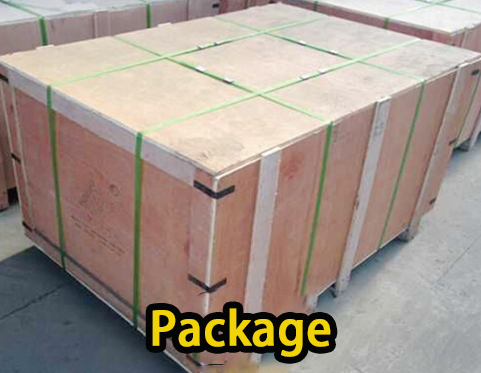
09. Product Testing
10. Package
Electrophoresis process
The electrophoresis process mainly includes the following steps:
1. Sample processing: Choose an appropriate sample extraction method and perform necessary pretreatment steps according to the sample type, such as cell disruption, protein solubilization, etc. Before adding buffer to the sample, it should be centrifuged to remove impurities or precipitates.
2. Preparation of buffer: Buffer plays a role in maintaining pH stability, providing ionic conductivity and diluting samples during electrophoresis experiments. When preparing buffers, reagents need to be accurately weighed and diluted in the correct proportions.
3. Preparation of electrophoresis tank and electrodes: Clean the electrophoresis tank and electrodes to ensure that no impurities remain. Check that the electrodes are in tight contact with the tank walls and that the connecting lines are not broken or short-circuited.
4. Prepare the paint: Dissolve the electrophoretic paint in water to form a uniform and stable suspension. The composition of the coating should be selected according to the requirements of the workpiece and the application field, and usually includes resin, solvent, curing agent, filler, etc. In addition, some additives such as defoaming agents and leveling agents can be added.
5. Set up the electrophoresis tank: Place the electrophoresis tank containing the paint in the electrophoresis equipment, and connect the positive and negative electrodes to the power supply. The positive electrode is connected to the metal plate in the electrophoresis tank, and the negative electrode is connected to the workpiece to generate an electric field under the action of voltage.
6. Adjust paint parameters: According to the requirements of the workpiece and paint, adjust the paint parameters in the electrophoresis tank, such as concentration, pH value, temperature and voltage, etc. Adjustment of these parameters can be determined through trials and experiments.
7. Sample loading: Add the substance to be tested into the prepared electrophoresis tank for separation. When loading samples, care should be taken to avoid air entering the gel to avoid affecting the separation effect. Determine the appropriate loading amount based on sample size and concentration. Too much or too little may affect experimental results.
8. Start electrophoresis: Place the processed workpiece in the electrophoresis tank and ensure that the workpiece is in complete contact with the paint. Turn on the power, causing the charged particles or ions in the paint to move toward and deposit on the surface of the workpiece under the action of an electric field.
9. Coating curing: After the surface coating of the workpiece reaches the required thickness, take the workpiece out of the electrophoresis tank and send it to an oven or air dry to solidify the coating.
The above are the general steps of the electrophoresis process. The specific operations may be adjusted due to different equipment and processes. During the entire electrophoresis process, various parameters and operating steps need to be strictly controlled to ensure product quality and stability.
OUR SERVICE
1. Expert R&D team: To help your business, our engineers create innovative designs for your items.
2. Quality Supervision Team: Every product is rigorously checked to make sure it functions properly before it is shipped.
3. A proficient logistics crew - personalized packing and prompt tracking guarantee the product's safety till it reaches you.
4. A self-contained post-purchase staff that offers clients prompt, expert assistance around-the-clock.
5.A proficient sales crew will impart the most expert knowledge to you to enable you to conduct company with customers more effectively.