Customized new design elevator guide rail brackets lift accessories
Description
Product Type | customized product | |||||||||||
One-Stop Service | Mold development and design-submit samples-batch production-inspection-surface treatment-packaging-delivery. | |||||||||||
Process | stamping,bending,deep drawing,sheet metal fabrication,welding,laser cutting etc. | |||||||||||
Materials | carbon steel,stainless steel,aluminum,copper,galvanized steel etc. | |||||||||||
Dimensions | according to customer's drawings or samples. | |||||||||||
Finish | Spray painting, electroplating, hot-dip galvanizing, powder coating, electrophoresis, anodizing, blackening, etc. | |||||||||||
Application Area | Auto parts, agricultural machinery parts, engineering machinery parts, construction engineering parts, garden accessories, environmentally friendly machinery parts, ship parts, aviation parts, pipe fittings, hardware tool parts, toy parts, electronic parts, etc. |
Advantags
1. More than 10 years of overseas trade expertise.
2. Provide one-stop service from mold design to product delivery.
3. Fast delivery time, about 30-40 days. In stock within one week.
4. Strict quality management and process control (ISO certified manufacturer and factory).
5. More reasonable prices.
6. Professional, our factory has more than 10 years of history in the field of metal stamping sheet metal.
Quality management
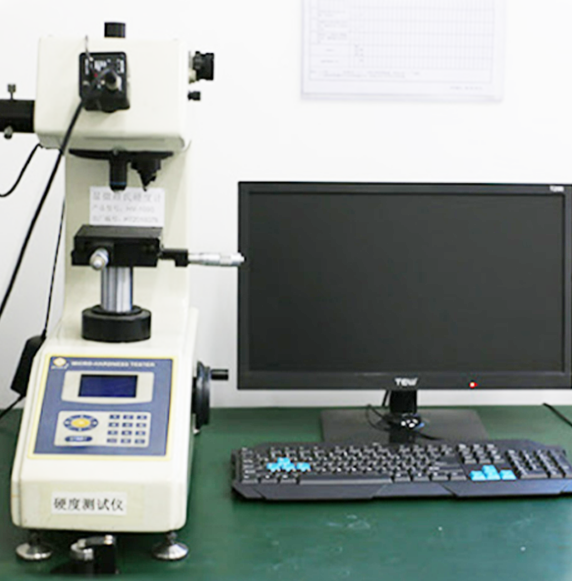
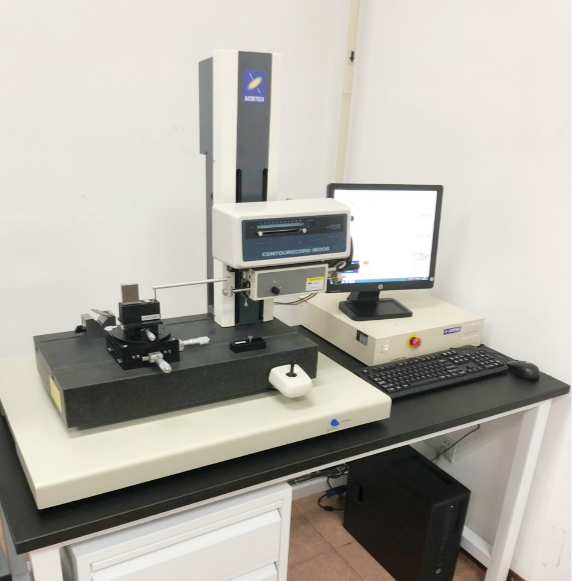
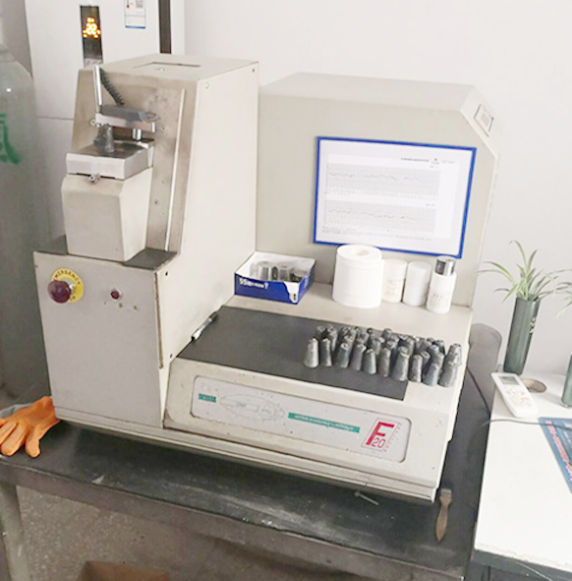
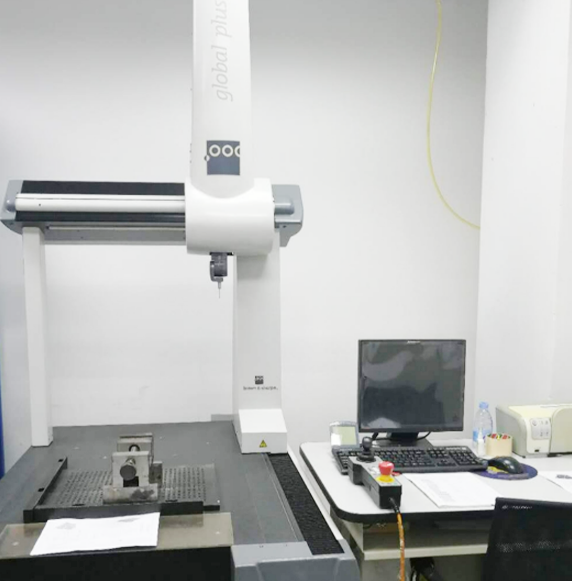
Vickers hardness instrument.
Profile measuring instrument.
Spectrograph instrument.
Three coordinate instrument.
Shipment Picture
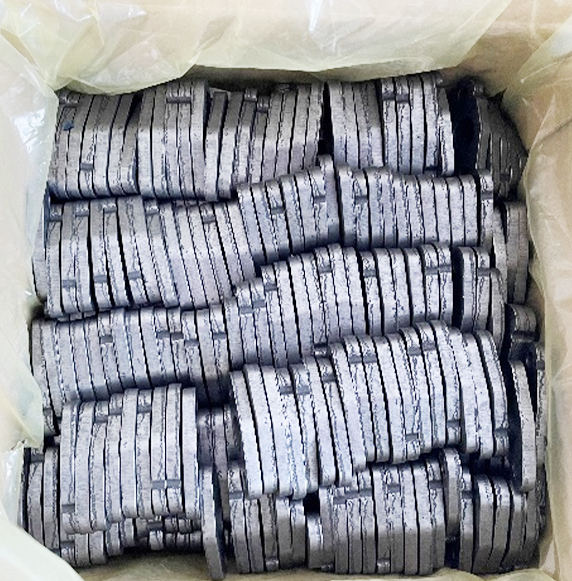
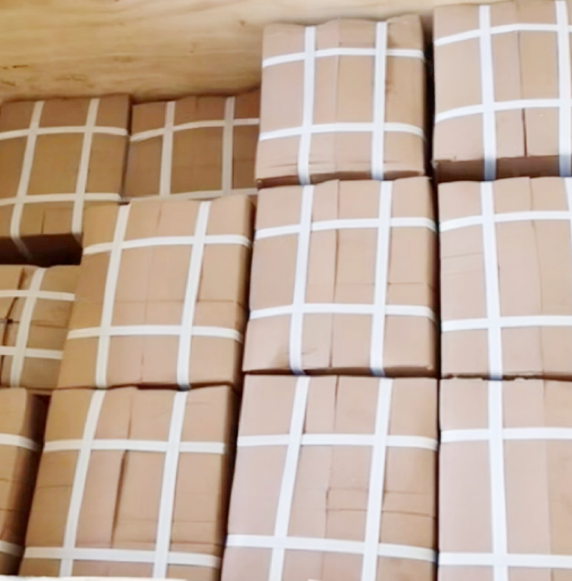
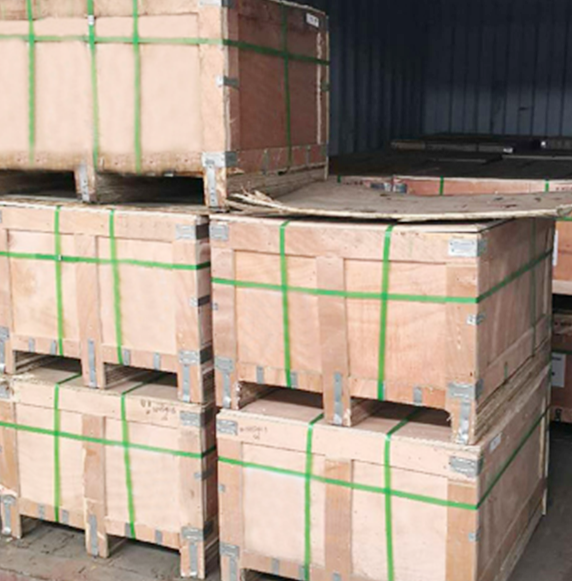
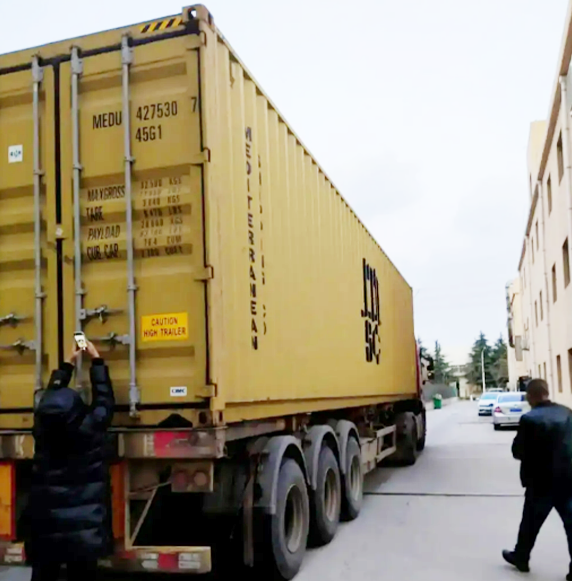
Production Process
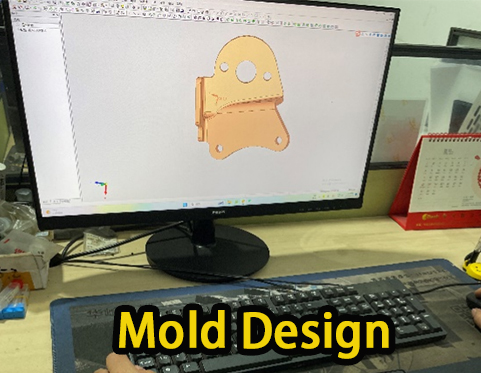
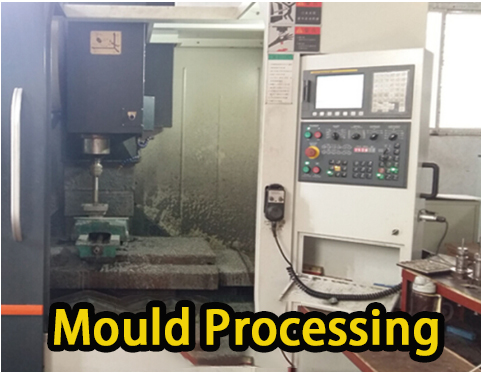
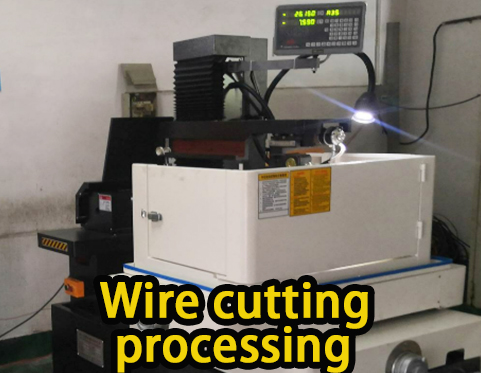
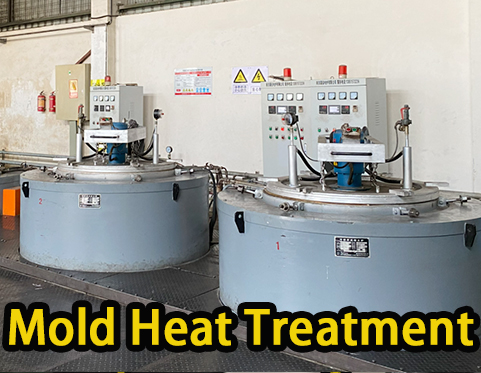
01. Mold design
02. Mould Processing
03. Wire cutting processing
04. Mold heat treatment
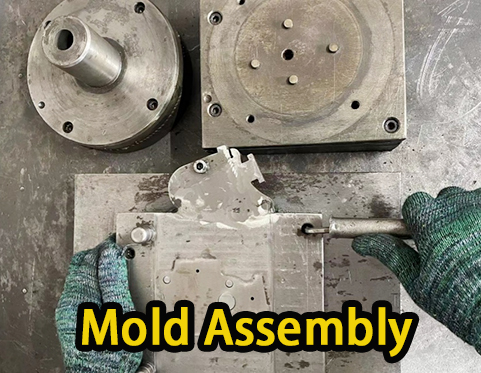
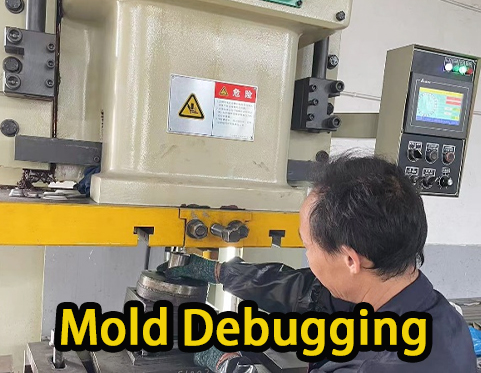
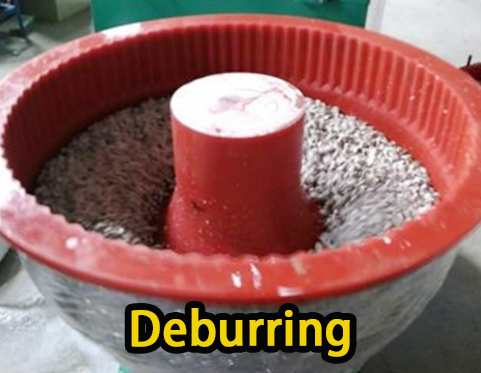

05. Mold assembly
06. Mold debugging
07. Deburring
08. electroplating
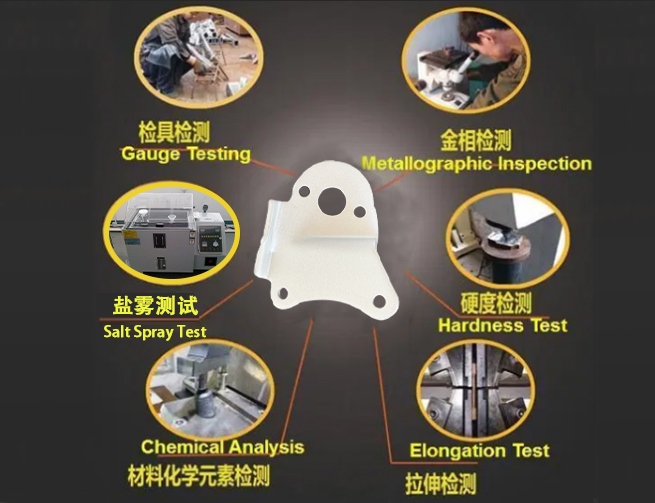
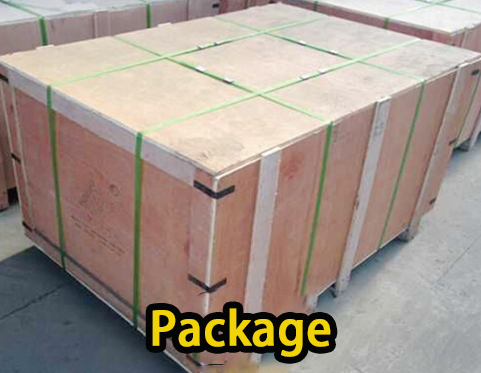
09. Product Testing
10. Package
Metal stamping design process
The intricate process of metal stamping may involve several metal forming techniques, such as punching, bending, blanking, and punching.
Blanking is the process of cutting a product's general shape or outline. This step's goal is to reduce and eliminate burrs, which can raise the part's price and cause a delay in delivery. The hole diameter, geometry/taper, edge to hole spacing, and first punch insertion location are all determined in this stage.
Bending: It's crucial to account for sufficient material when designing bends in stamped metal components. Make sure to account for sufficient material in both the part's design and its blank.
Punching is the process of tapping a stamped metal part's edges to remove burrs or flatten them. This produces smoother edges in the part's cast areas, increases the strength of the part's localized areas, and can be used to forego secondary processing like deburring and grinding.
Precision Metal Forming
Xinzhe Metal Stampings takes pride in its ability to use in-house dies and machines to make even the most complex shapes.
Over the last ten years, we have created tools to create over 8,000 different parts, ranging from simple to complex designs. Xinzhe Metal Stampings often takes on contracts that other companies have turned down because they're too difficult or "impossible" to do. We deal with a wide range of materials and offer a choice of secondary services to complement your sheet metal fabrication project.
A state-of-the-art Komatsu Servo Punch Press, ideal for precise metal forming operations, is one of our more recent additions. We have more options with this press in terms of how many operations are needed to accomplish significant metal shaping.
Our specialization is saving you money with creative, economical precision metal forming solutions. It should come as no surprise that clients who want metal forming have relied on Xinzhe Metal Stampings.