Customized metal bending four-sided mold factory
Description
Product Type | customized product | |||||||||||
One-Stop Service | Mold development and design-submit samples-batch production-inspection-surface treatment-packaging-delivery. | |||||||||||
Process | stamping,bending,deep drawing,sheet metal fabrication,welding,laser cutting etc. | |||||||||||
Materials | carbon steel,stainless steel,aluminum,copper,galvanized steel etc. | |||||||||||
Dimensions | according to customer's drawings or samples. | |||||||||||
Finish | Spray painting, electroplating, hot-dip galvanizing, powder coating, electrophoresis, anodizing, blackening, etc. | |||||||||||
Application Area | Auto parts, agricultural machinery parts, engineering machinery parts, construction engineering parts, garden accessories, environmentally friendly machinery parts, ship parts, aviation parts, pipe fittings, hardware tool parts, toy parts, electronic parts, etc. |
Precision Metal Forming
Xinzhe Metal Stampings is proud of its capacity to create even the most intricate shapes with dies and tools made in-house.
In the past ten years, we have developed tools to make over 8,000 distinct pieces, including several difficult shapes in addition to some easy ones. Xinzhe Metal Stampings frequently accepts jobs that others have declined because they are too challenging or "impossible" to complete. We provide a variety of secondary services to add to your sheet metal fabrication project in addition to working with a wide range of materials.
One of our more recent additions is a Komatsu Servo Punch Press that is state of the art for precision metal forming operations. This press allows us greater flexibility in relation to the number of operations required to achieve extensive metal forming.
Saving you money by providing innovative, cost-effective precision metal forming solutions is our specialty. It’s no surprise that customers have trusted Xinzhe Metal Stampings for their metal forming needs.
Quality management
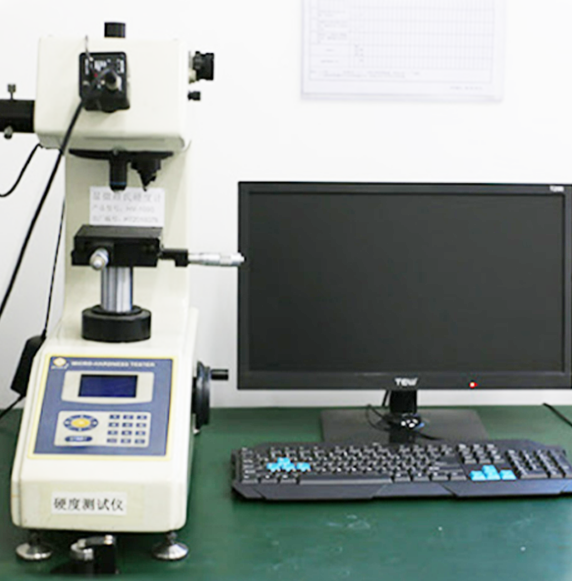
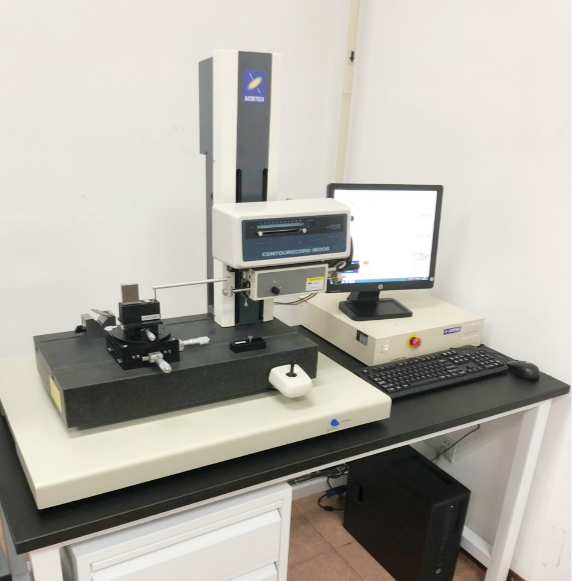
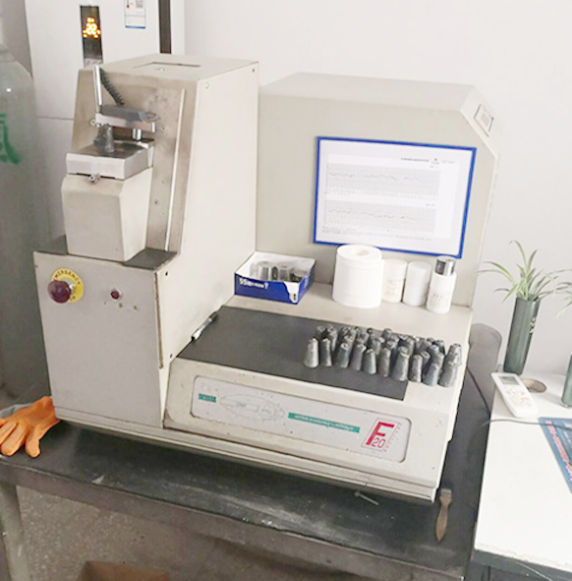
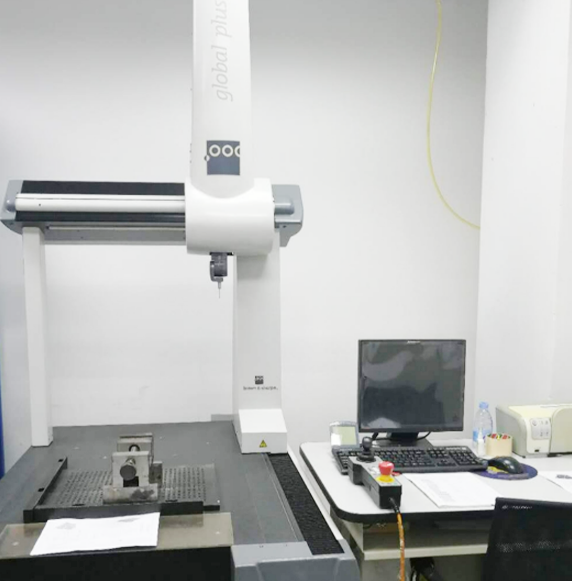
Vickers hardness instrument.
Profile measuring instrument.
Spectrograph instrument.
Three coordinate instrument.
Shipment Picture
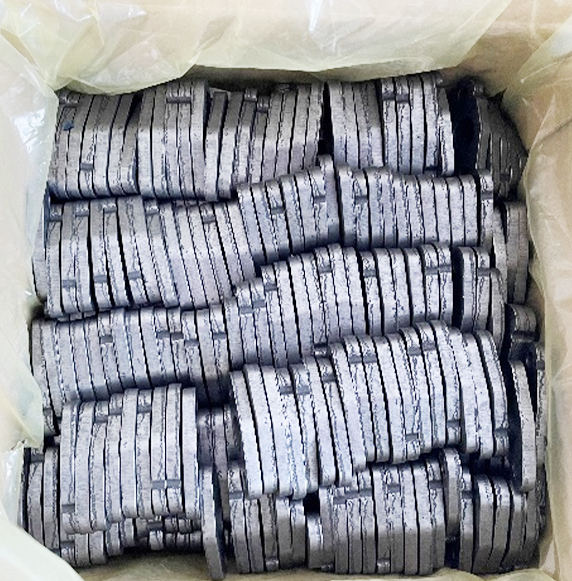
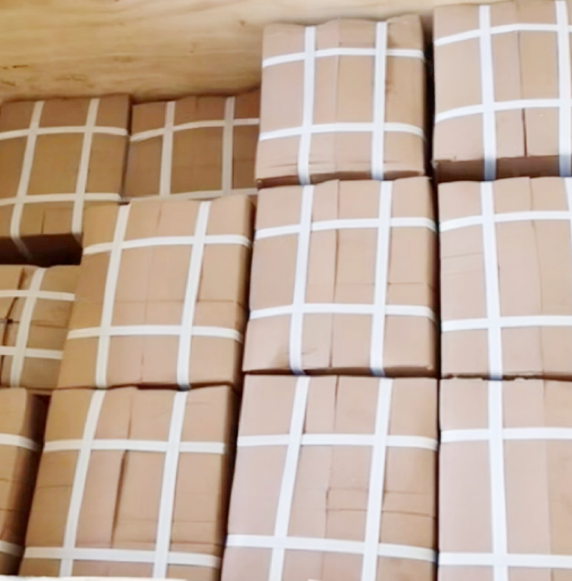
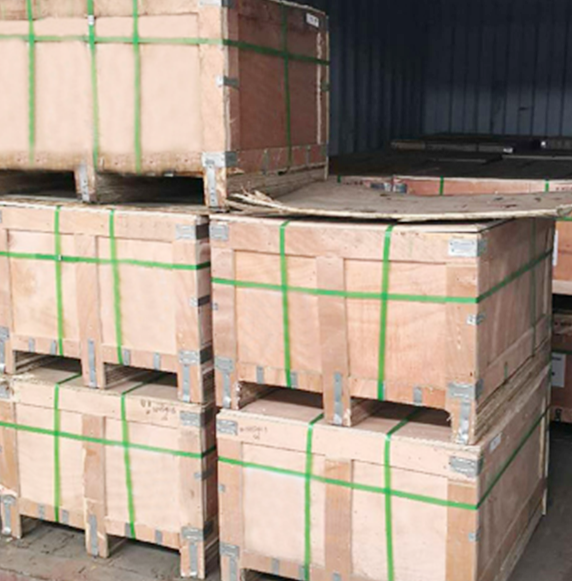
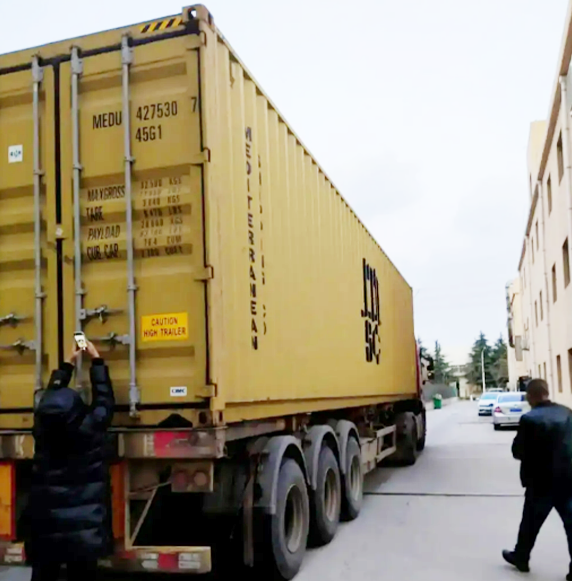
Production Process
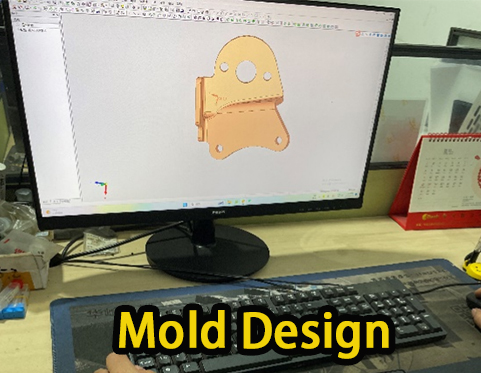
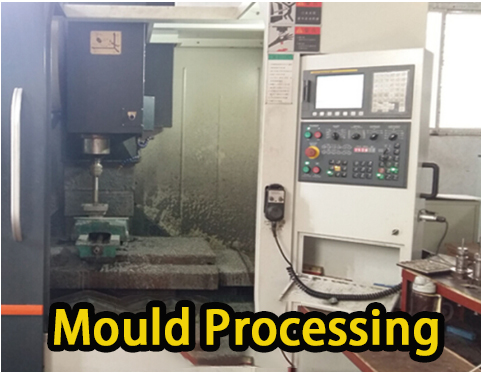
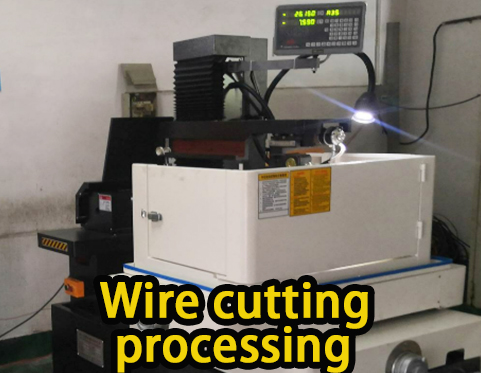
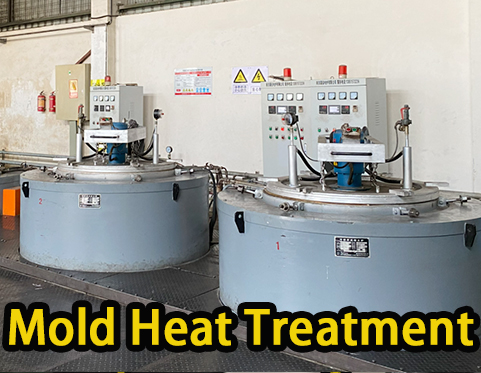
01. Mold design
02. Mould Processing
03. Wire cutting processing
04. Mold heat treatment
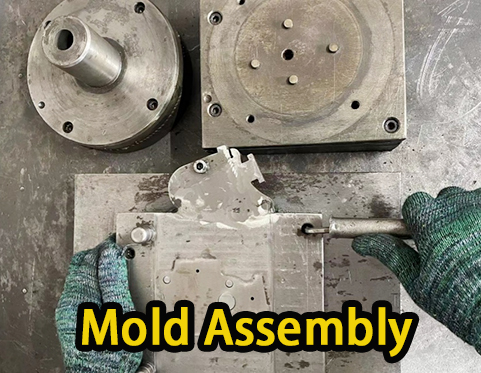
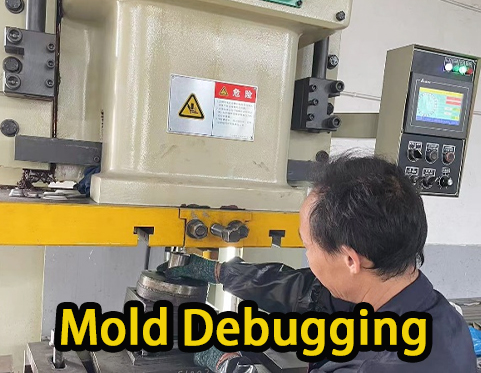
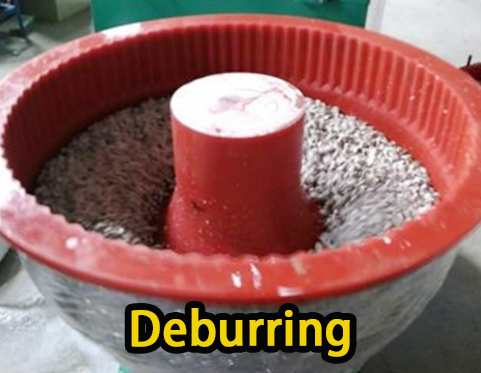

05. Mold assembly
06. Mold debugging
07. Deburring
08. electroplating
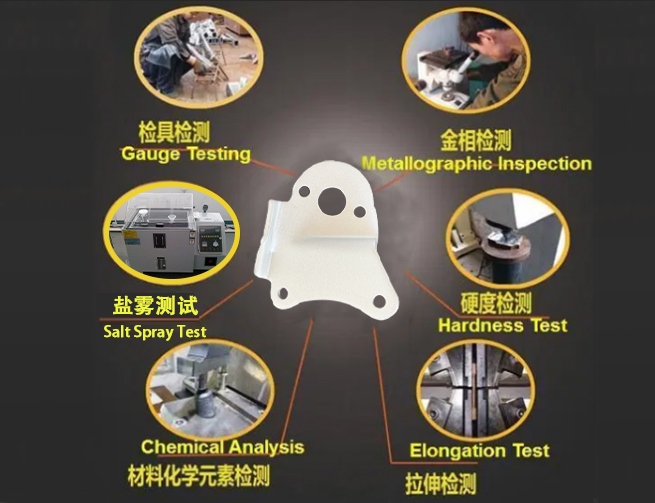
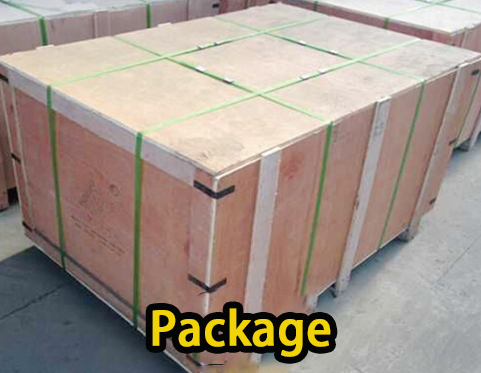
09. Product Testing
10. Package
The Stamping Process
Metal stamping is a manufacturing process in which coils or flat sheets of material are formed into specific shapes. Stamping encompasses multiple forming techniques such as blanking, punching, embossing, and progressive die stamping, to mention just a few. Parts use either a combination of these techniques or independently, depending on the piece’s complexity. In the process, blank coils or sheets get fed into a stamping press which uses tools and dies to form features and surfaces in the metal. Metal stamping is an excellent way to mass-produce various complex parts, from car door panels and gears to small electrical components used in phones and computers. Stamping processes are highly-adopted in automotive, industrial, lighting, medical, and other industries.
Stainless steel stamping
Stainless steel stamping operations include:
blanking
bending
metal forming
punching
casting
Short run production and prototyping
Stainless steel disc stamping
Characteristics of Stamped Stainless Steel Parts
Features and benefits of stainless steel include:
Fire and heat resistance: Stainless steels containing large amounts of chromium and nickel are particularly resistant to thermal stress.
Aesthetics: Consumers appreciate the clean, modern look of stainless steel, which can also be electropolished to improve the finish.
Long-term cost-effectiveness: While stainless steel may cost more initially, it can last for decades without quality or cosmetic damage.
Hygiene: Some stainless steel alloys are trusted by the pharmaceutical and food and beverage industries due to their ease of cleaning and are also considered food grade.
Sustainability: Stainless steel is considered one of the most sustainable alloy options, making it ideal for green manufacturing methods.