Customized high-quality elevator T-shaped guide rail clamp
Description
Product Type | customized product | |||||||||||
One-Stop Service | Mold development and design-submit samples-batch production-inspection-surface treatment-packaging-delivery. | |||||||||||
Process | stamping,bending,deep drawing,sheet metal fabrication,welding,laser cutting etc. | |||||||||||
Materials | carbon steel,stainless steel,aluminum,copper,galvanized steel etc. | |||||||||||
Dimensions | according to customer's drawings or samples. | |||||||||||
Finish | Spray painting, electroplating, hot-dip galvanizing, powder coating, electrophoresis, anodizing, blackening, etc. | |||||||||||
Application Area | Auto parts, agricultural machinery parts, engineering machinery parts, construction engineering parts, garden accessories, environmentally friendly machinery parts, ship parts, aviation parts, pipe fittings, hardware tool parts, toy parts, electronic parts, etc. |
Why choose xinzhe?
You are dealing with a qualified metal stamping specialist when you visit Xinzhe. Serving clients worldwide, we have been specializing in metal stamping for almost a decade. Our mold technicians and design engineers are expert professionals that are committed to their work.
What is the key to our accomplishments? Two words sum up the response: quality assurance and requirements. For us, every project is distinct. It is driven by your vision, and it is our duty to realize that goal. In order to accomplish this, we make an effort to comprehend every aspect of your project.
We'll get to work on developing your idea as soon as we hear it. The process has several checkpoints. This enables us to guarantee that the finished product completely satisfies your needs.
Our team now focuses in the following categories for custom metal stamping services:
Gradual stamping for both small and large quantities.
Secondary stamping in small batches.
tapping inside the mold.
secondary or assembly tabbing.
both machining and forming.
Quality management
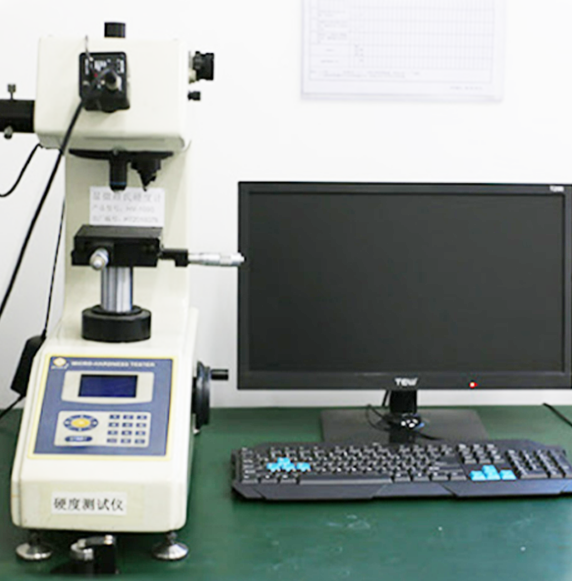
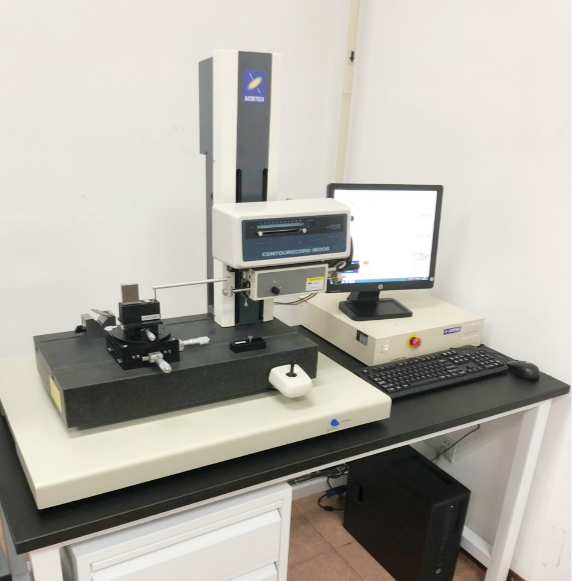
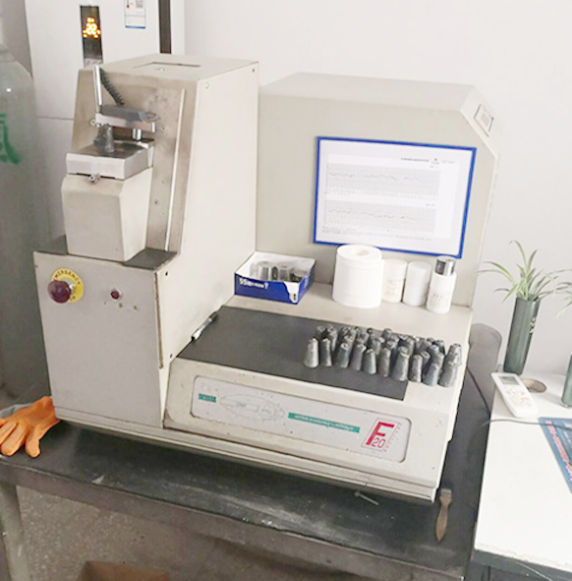
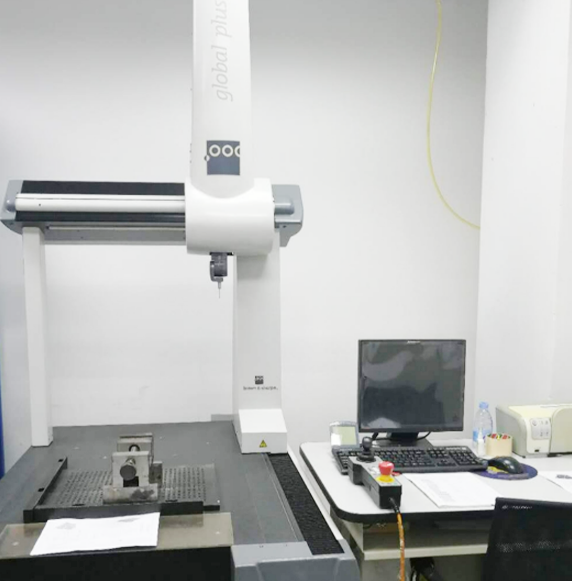
Vickers hardness instrument.
Profile measuring instrument.
Spectrograph instrument.
Three coordinate instrument.
Shipment Picture
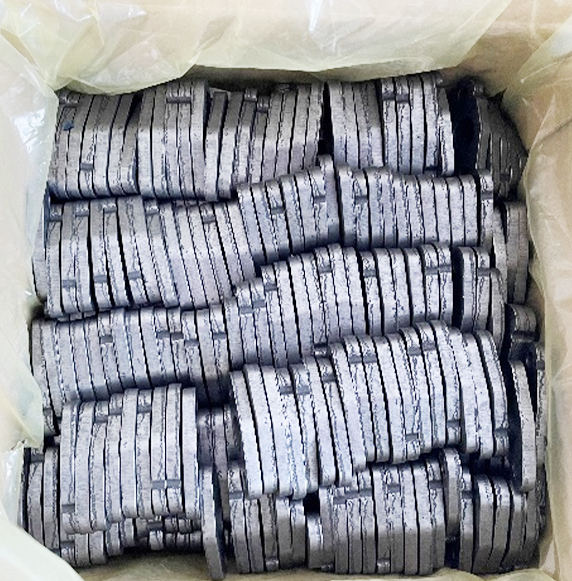
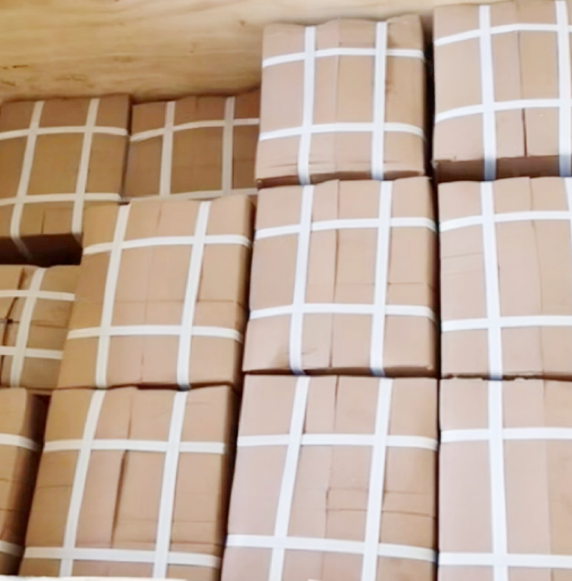
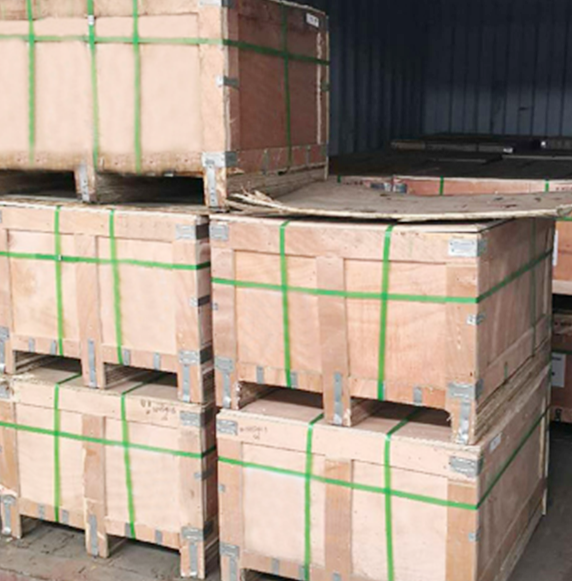
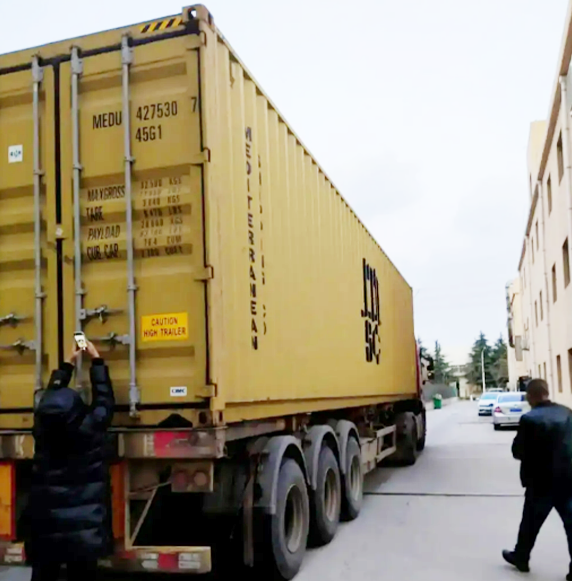
Production Process
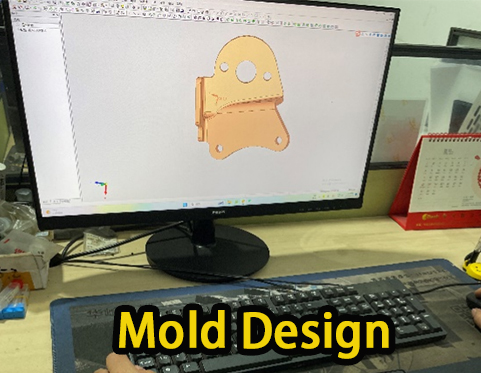
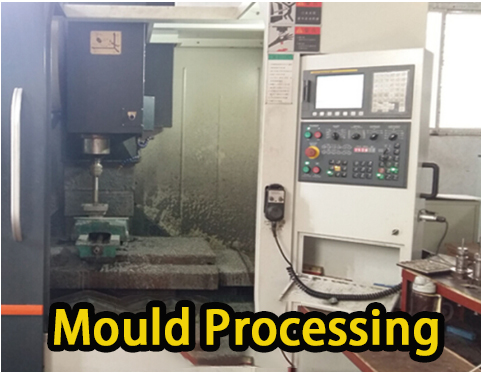
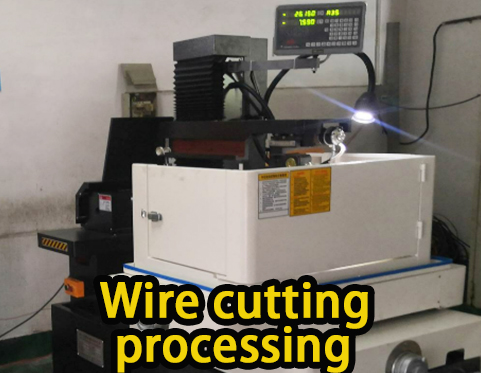
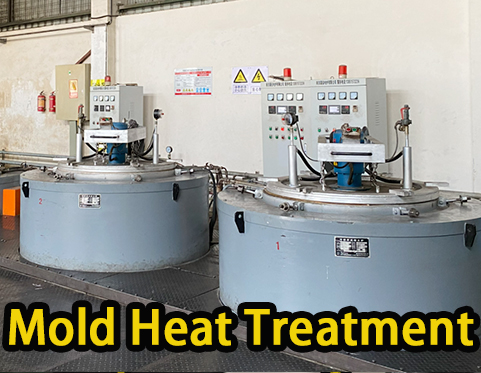
01. Mold design
02. Mould Processing
03. Wire cutting processing
04. Mold heat treatment
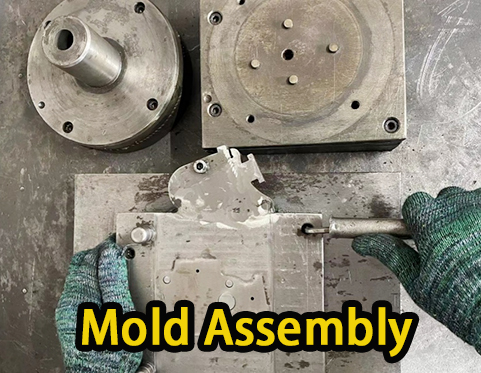
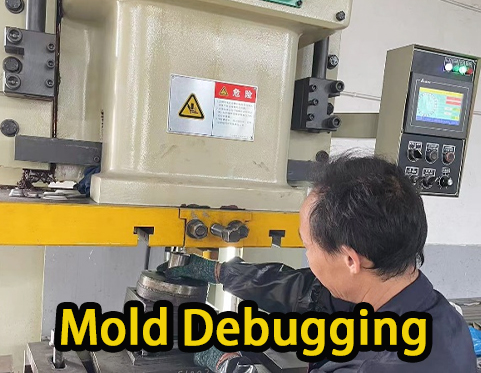
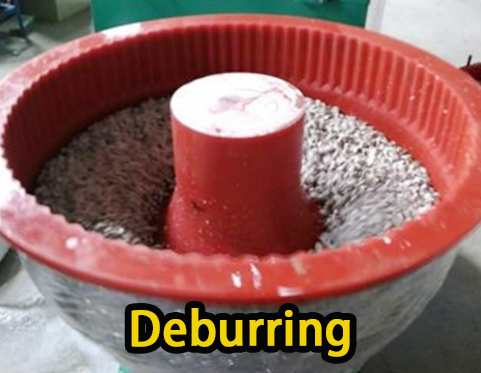

05. Mold assembly
06. Mold debugging
07. Deburring
08. electroplating
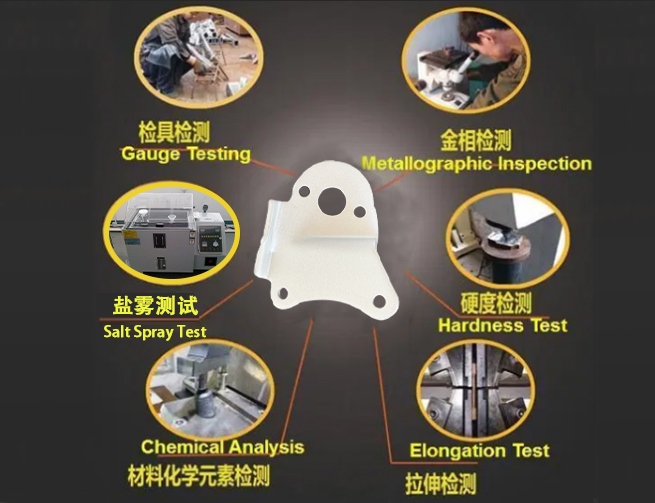
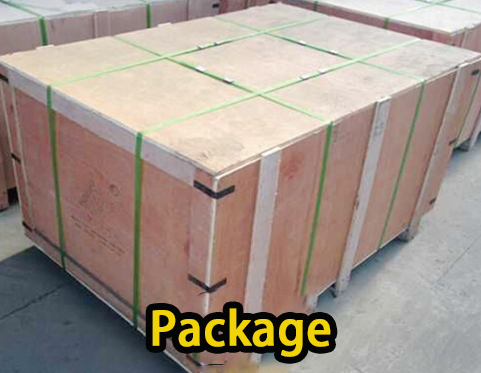
09. Product Testing
10. Package
Advantage
Stamping is suitable for mass, complex part production. More specifically, it offers:
• Complex forms, such as contours
• High volumes (from thousands to millions of parts per year)
• Processes such as fineblanking allow for forming of thick metal sheets.
• Low cost-per-piece prices
Electroplating process
The electroplating process involves multiple steps to ensure the final coating quality and performance are as expected. The following is the basic process flow of electroplating:
1. Hanging: Fix the parts to be electroplated on the conductive tool to form a closed loop with the power source to prepare for the electroplating process.
2. Degreasing and degreasing: Clean the surface of parts and remove impurities such as grease, dust, etc. These impurities will affect the subsequent plating effect and the appearance of the part surface.
3. Water washing: Clean away the chemical substances and impurities remaining on the surface of the parts during the degreasing and oil removal process.
4. Pickling activation: Through the corrosive effect of acid solution, the oxide scale and rust on the metal surface are removed, ensuring the cleanliness and activity of the surface of the parts, and providing a good base for electroplating.
5. Electroplating: In the electroplating tank, the parts serve as cathodes and are immersed in the plating solution together with the anode (plated metal). After energization, the metal ions of the coating are reduced on the surface of the part to form the required metal coating.
6. Post-processing: Carry out some post-processing as needed, such as passivation, sealing, etc., to enhance the performance and appearance of the coating.
7. Water washing: Clean away the plating solution and impurities remaining on the surface of the parts during the electroplating process.
8. Drying: Dry the parts to ensure that no moisture remains on the surface.
9. Hanging and inspection packaging: Remove the parts from the conductive tools, and conduct quality inspection and packaging to ensure the plating quality and meet customer needs.
During the electroplating process, it is also necessary to pay attention to standardized operations, such as controlling the current density, periodically changing the direction of the current, controlling the temperature of the plating solution, and stirring the plating solution, to ensure the uniformity, flatness and brightness of the coating. In addition, depending on specific needs and material types, special treatments such as pre-plating and nickel bottom plating can also be performed to improve the adhesion and corrosion resistance of the coating.