Customized galvanized bending stamping parts elevator bracket
Description
Product Type | customized product | |||||||||||
One-Stop Service | Mold development and design-submit samples-batch production-inspection-surface treatment-packaging-delivery. | |||||||||||
Process | stamping,bending,deep drawing,sheet metal fabrication,welding,laser cutting etc. | |||||||||||
Materials | carbon steel,stainless steel,aluminum,copper,galvanized steel etc. | |||||||||||
Dimensions | according to customer's drawings or samples. | |||||||||||
Finish | Spray painting, electroplating, hot-dip galvanizing, powder coating, electrophoresis, anodizing, blackening, etc. | |||||||||||
Application Area | Auto parts, agricultural machinery parts, engineering machinery parts, construction engineering parts, garden accessories, environmentally friendly machinery parts, ship parts, aviation parts, pipe fittings, hardware tool parts, toy parts, electronic parts, etc. |
Advantags
1. More than 10 years of overseas trade expertise.
2. Provide one-stop service from mold design to product delivery.
3. Fast delivery time, about 30-40 days. In stock within one week.
4. Strict quality management and process control (ISO certified manufacturer and factory).
5. More reasonable prices.
6. Professional, our factory has more than 10 years of history in the field of metal stamping sheet metal.
Quality management
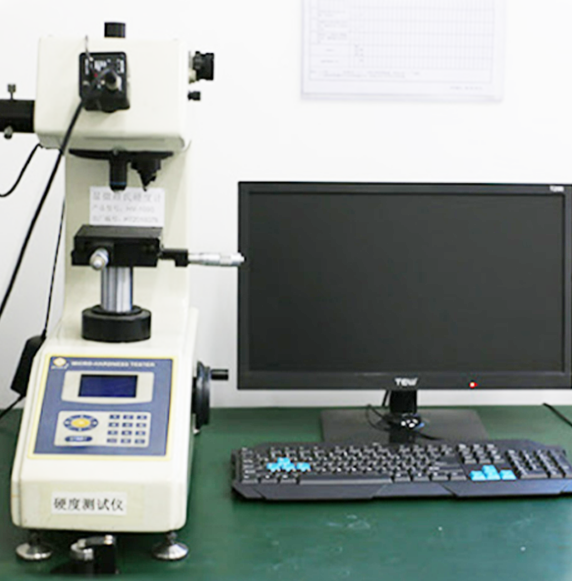
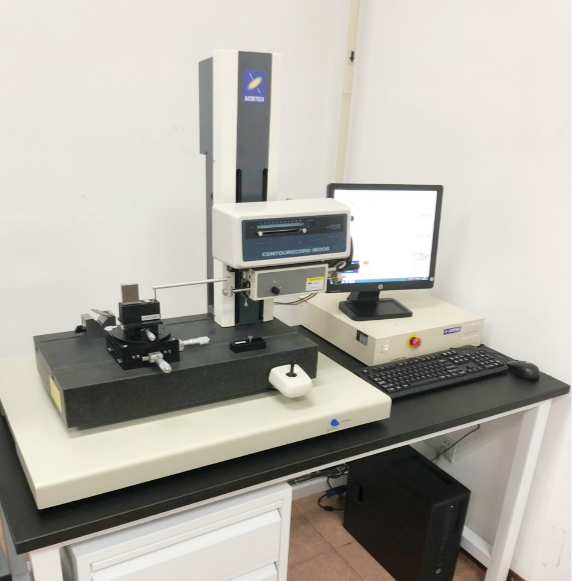
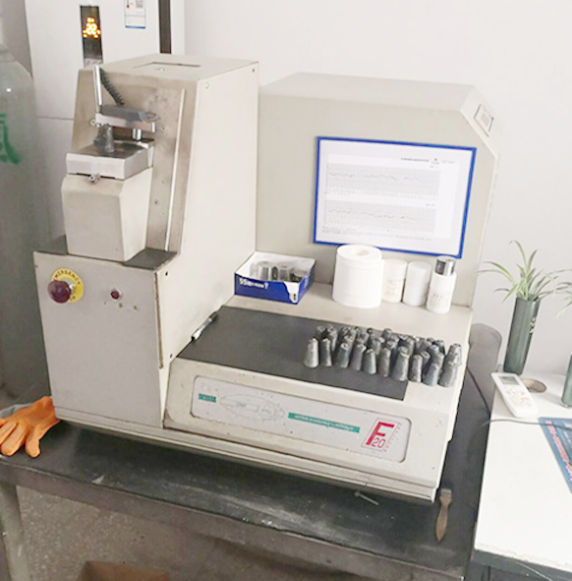
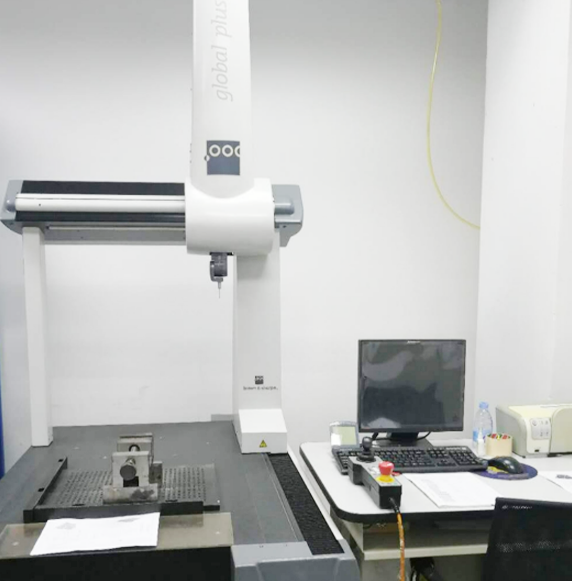
Vickers hardness instrument.
Profile measuring instrument.
Spectrograph instrument.
Three coordinate instrument.
Shipment Picture
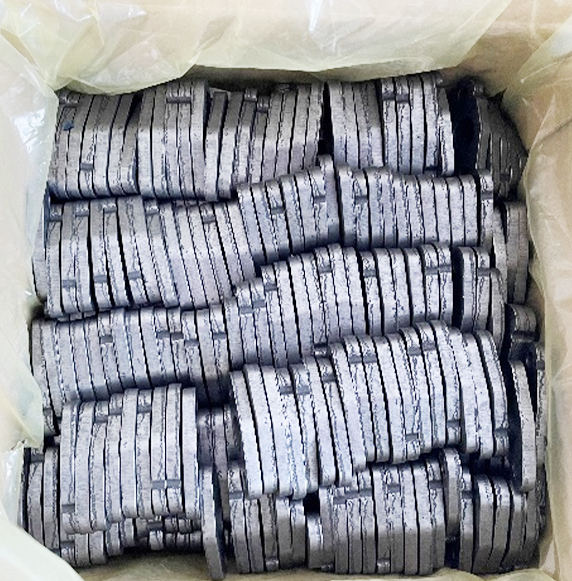
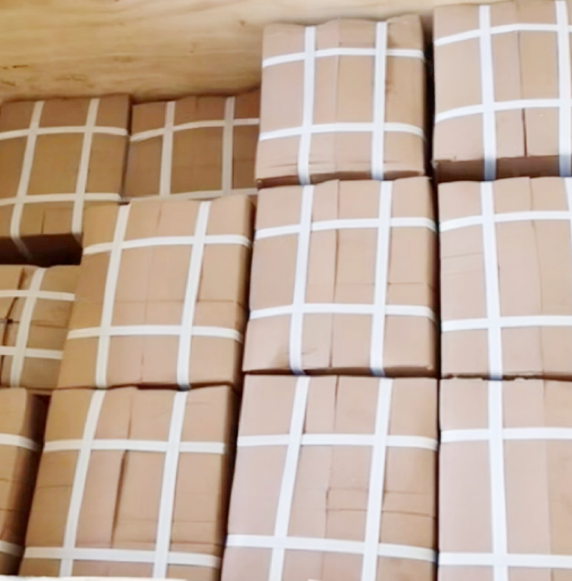
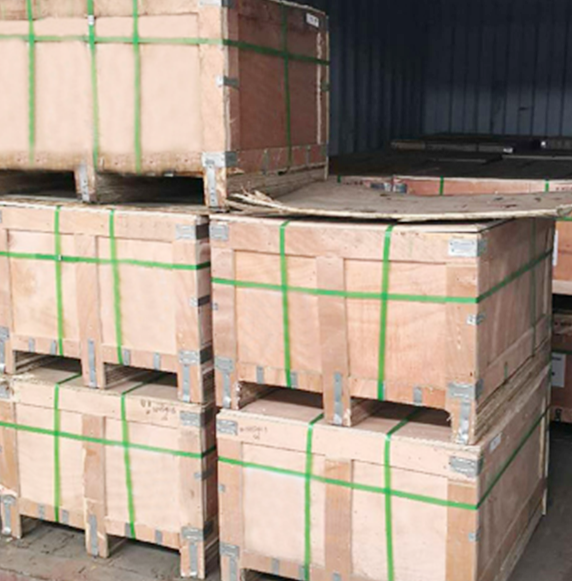
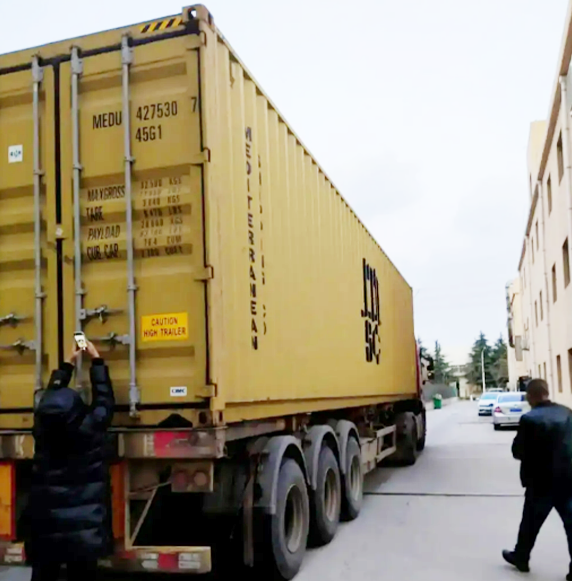
Production Process
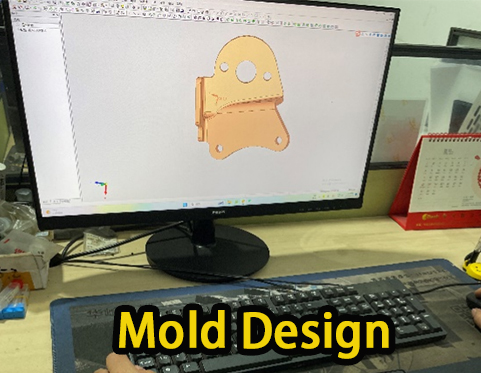
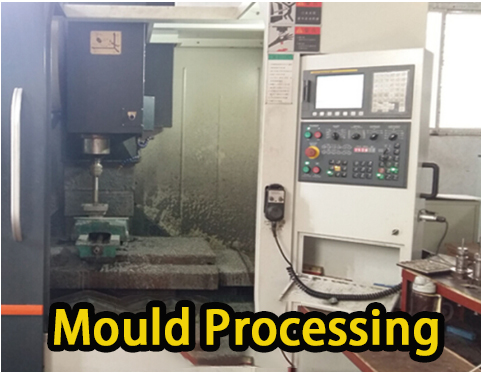
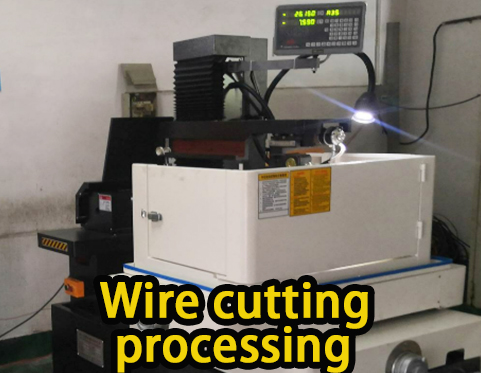
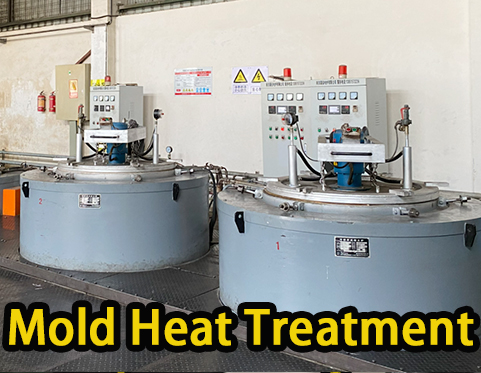
01. Mold design
02. Mould Processing
03. Wire cutting processing
04. Mold heat treatment
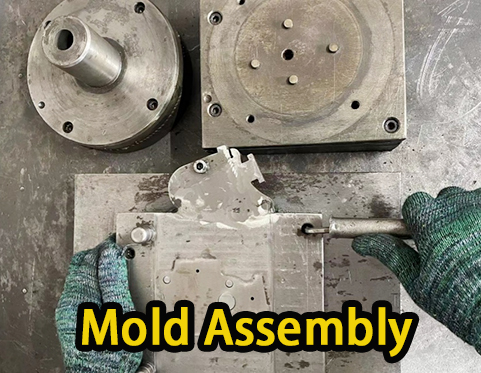
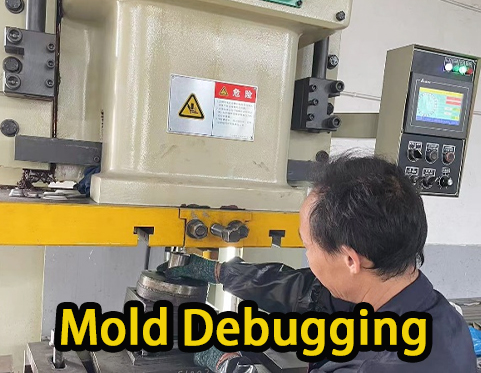
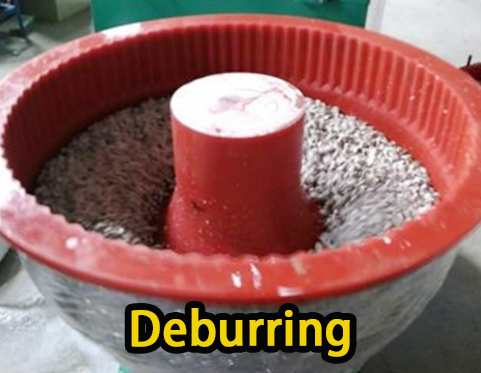

05. Mold assembly
06. Mold debugging
07. Deburring
08. electroplating
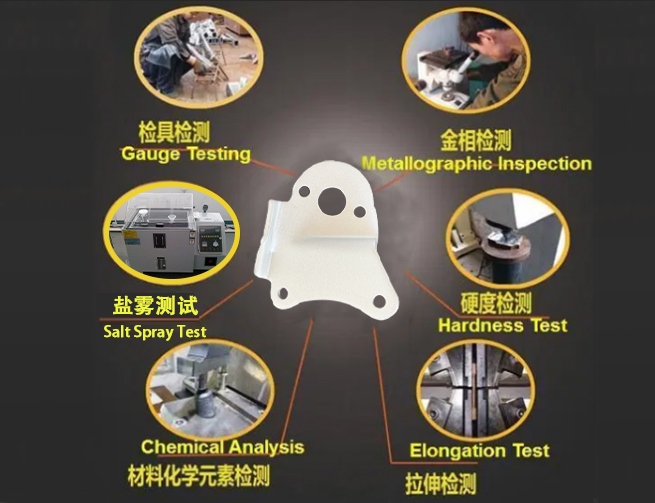
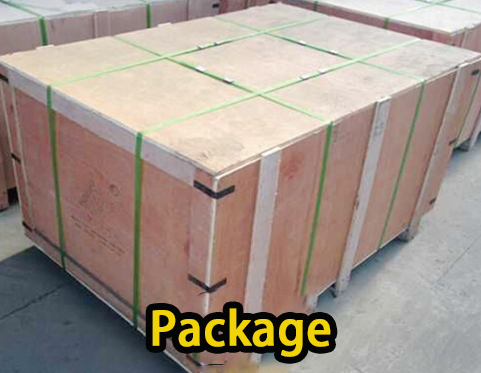
09. Product Testing
10. Package
Galvanizing process
The galvanizing process is a surface treatment technology that coats the surface of steel alloy materials with a layer of zinc for aesthetics and rust prevention. This coating is an electrochemical protective layer that prevents metal corrosion. The galvanizing process mainly uses two methods: hot-dip galvanizing and electro-galvanizing.
Hot-dip galvanizing is to put the workpiece into a hot-dip galvanizing bath and heat it to a certain temperature (usually 440 to 480°C), so that the zinc layer is firmly bonded to the surface of the workpiece at high temperature to form a hot-dip galvanizing layer. Then, the hot-dip galvanized layer is fully solidified after cooling. Hot-dip galvanizing has the advantages of high quality, high yield, low consumption, significant economic benefits, etc., and has a protective effect on the anode. When the coating is complete, it can play an insulating role; if the coating is not too damaged, the coating itself will be eroded due to electrochemical action, thereby protecting the steel from corrosion.
Electro-zinc plating deposits a layer of zinc on the surface of the workpiece through electrolysis. This method is suitable for thinner coatings, and the coating is more uniform.
Galvanized sheets are widely used in construction, home appliances, furniture, transportation, steel and other daily necessities. For example, in the construction industry, galvanized sheets are used in roofs, balcony panels, window sills, warehouses, highway guardrails, etc.; in the home appliance industry, galvanized sheets are used in refrigerators, washing machines, switch cabinets, air conditioners, etc.; in the transportation industry , car roofs, car shells, compartment panels, containers, etc. will also use the galvanizing process.
However, the galvanizing process also has some disadvantages. For example, a galvanized coating can be damaged by mechanical wear, corrosion, or other factors, reducing its ability to protect against corrosion. In high-temperature environments, galvanized coatings may fail because zinc has a low melting point and can easily melt, volatilize, or lose its protective effect at high temperatures. In addition, the production and processing of galvanized coatings consume a large amount of energy and water, thus causing certain environmental impacts. During the production and processing process, some harmful gases and wastewater may also be produced, which may affect human health.
In general, the galvanizing process is an important metal anti-corrosion method with a wide range of applications. However, in practical applications, it is also necessary to consider its possible shortcomings and take corresponding measures to reduce its impact on the environment and human health.
Quality warranty
1. Quality records and inspection data are kept for every product during manufacture and inspection.
2. Before being shipped to our clients, every prepared part is put through a rigorous testing process.
3. We guarantee to replace each element at no cost if any of these are harmed while operating normally.
Because of this, we are certain that every part we sell will function as intended and is covered by a lifetime warranty against flaws.