Customized adjustable elastic stainless steel door closer
Description
Product Type | customized product | |||||||||||
One-Stop Service | Mold development and design-submit samples-batch production-inspection-surface treatment-packaging-delivery. | |||||||||||
Process | stamping,bending,deep drawing,sheet metal fabrication,welding,laser cutting etc. | |||||||||||
Materials | carbon steel,stainless steel,aluminum,copper,galvanized steel etc. | |||||||||||
Dimensions | according to customer's drawings or samples. | |||||||||||
Finish | Spray painting, electroplating, hot-dip galvanizing, powder coating, electrophoresis, anodizing, blackening, etc. | |||||||||||
Application Area | Auto parts, agricultural machinery parts, engineering machinery parts, construction engineering parts, garden accessories, environmentally friendly machinery parts, ship parts, aviation parts, pipe fittings, hardware tool parts, toy parts, electronic parts, etc. |
Types of stamping
To ensure that the best process is used to manufacture your products, we provide deep draw, four-slide, progressive die, single and multistage stamping, and other options. Once your 3D model and technical drawings are submitted, Xinzhe's experts can match your project with the right stamping.
- Deeper pieces can be created than would normally be possible with a single die by using numerous dies and phases in progressive die stamping. As the parts pass through different dies, it also permits numerous geometries for each part. Large, high volume items, like those in the automotive industry, are ideally suited for this approach. A workpiece attached to a metal strip dragged during the entire process is used in progressive die stamping, which is similar to transfer die stamping. The workpiece is taken out and moved along a conveyor in transfer die stamping.
- With deep voids, akin to enclosed rectangles, stampings made with deep draw stamping are produced. Since the metal's structure is compressed into a more crystalline shape by the high deformation, this method produces stiff pieces. Standard draw stamping is also frequently employed, employing shallower dies to form the metal.
- Parts are shaped using four axes rather than just one when using fourslide stamping. Electronics components like phone battery connections and other small, delicate pieces are manufactured using this technique. The automotive, aerospace, medical, and electronics industries all favor fourslide stamping because it provides increased design flexibility, reduced production costs, and quicker manufacturing turnaround times.
- The development of stamping is hydroforming. Sheets are positioned atop a bottom-shaped die, and the upper die is shaped like an oil bladder that fills to a high pressure, forcing the metal into the lower die's shape. Hydroforming can be used to create several components at once. Although hydroforming is a fast and precise process, the components must be cut out of the sheet afterwards using a trim die.
- Blanking is the first process before shaping, where bits are taken out of the sheet. A variation on blanking called fineblanking produces accurate cuts with flat surfaces and smooth edges.
- Another method of blanking that produces tiny spherical workpieces is coining. This eliminates burrs and rough edges from the metal and hardens it since it takes a lot of force to make a little piece.
- In contrast to blanking, which involves removing material to form a workpiece, punching entails removing material from the workpiece.
- By creating a sequence of depressions or raising the design above the surface, embossing gives the metal a three-dimensional appearance.
- One axis of bending is utilized to make profiles that are shaped like U, V, or L. This method involves pressing the metal into or against a die, or clamping one side and bending the other over a die. Bending for tabs or sections of a workpiece rather than the entire piece is known as flanging.
Quality management
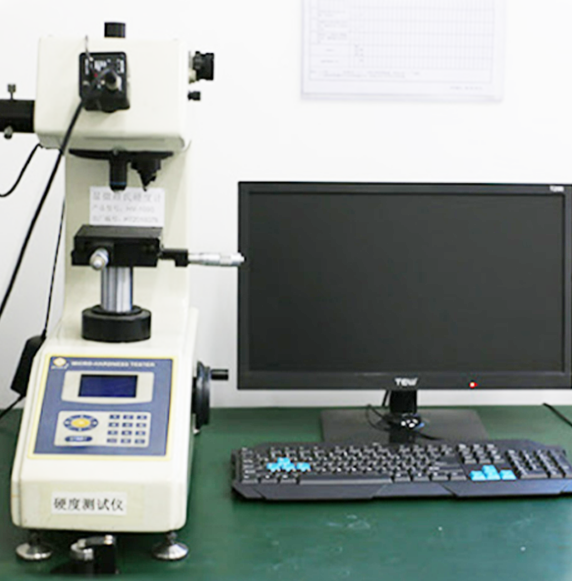
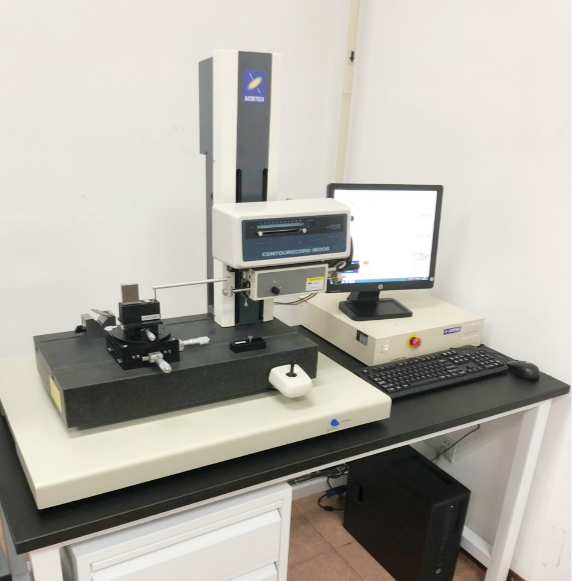
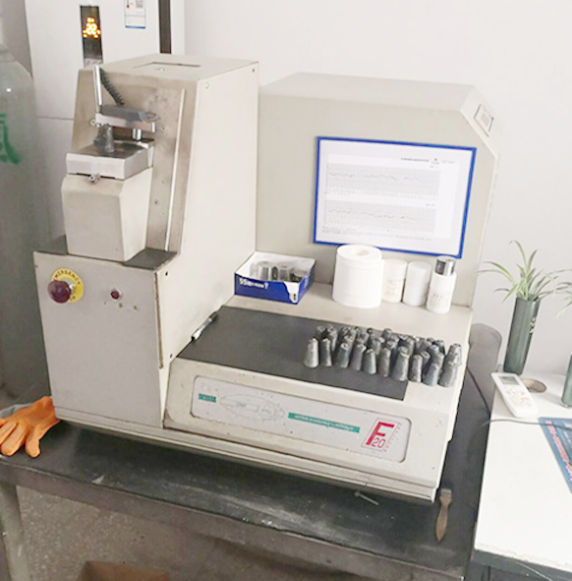
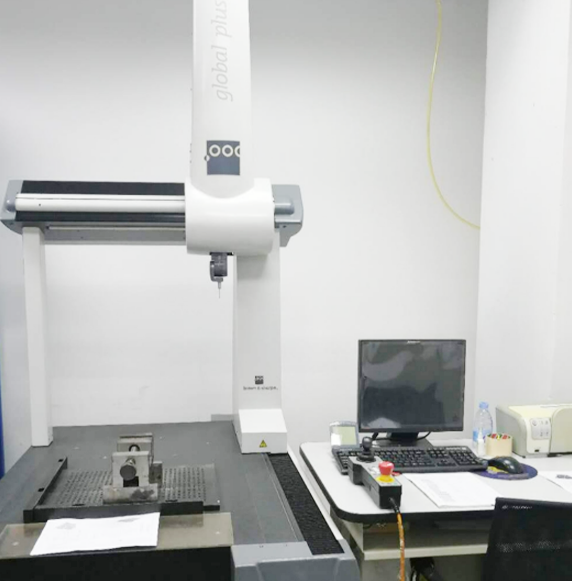
Vickers hardness instrument.
Profile measuring instrument.
Spectrograph instrument.
Three coordinate instrument.
Shipment Picture
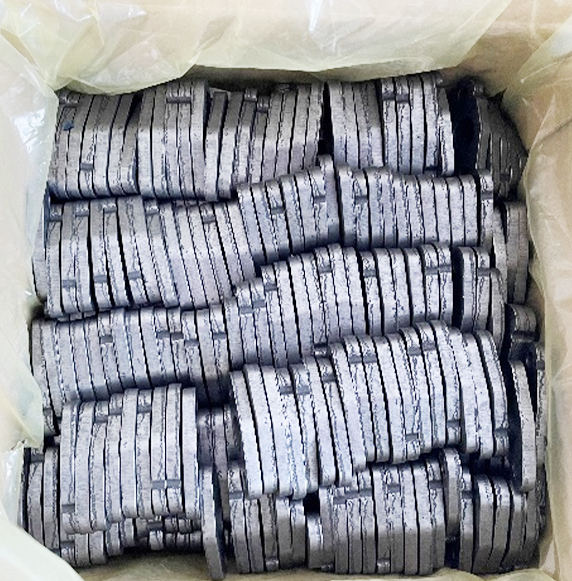
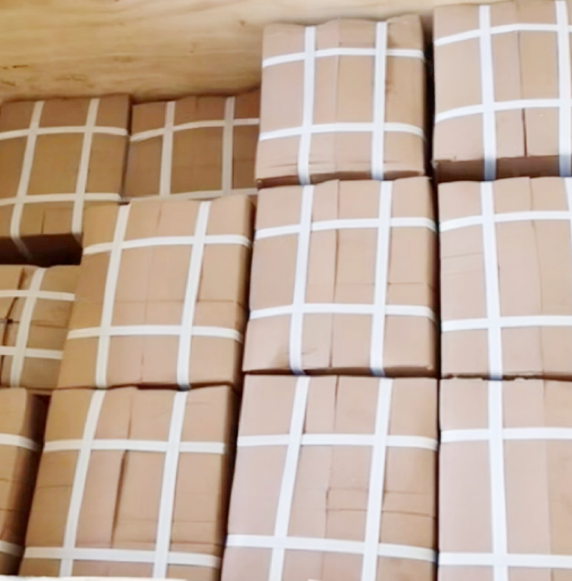
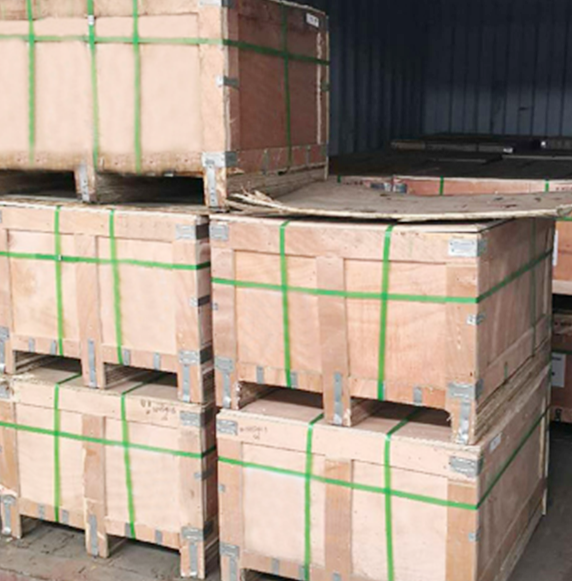
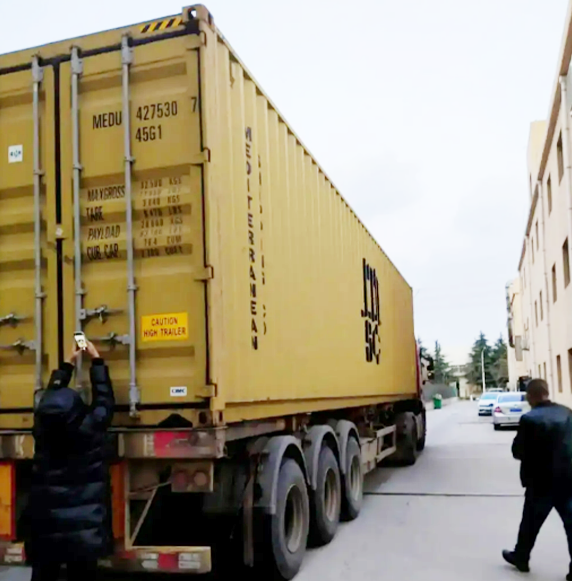
Production Process
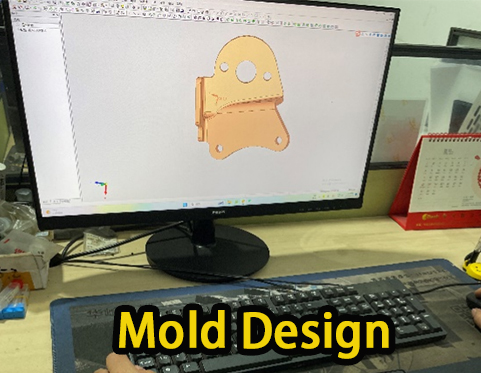
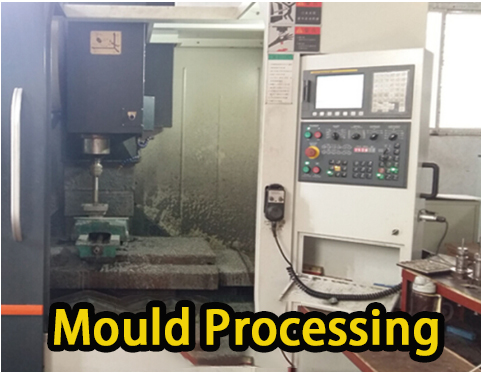
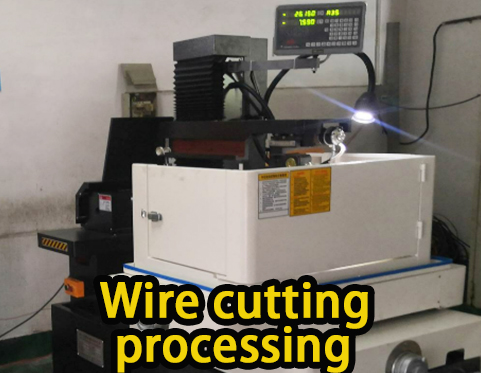
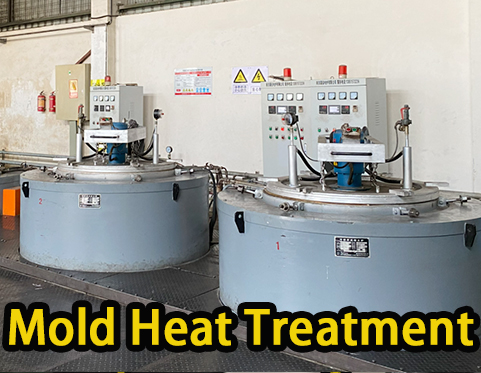
01. Mold design
02. Mould Processing
03. Wire cutting processing
04. Mold heat treatment
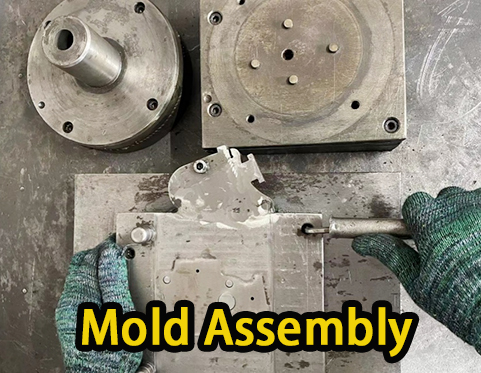
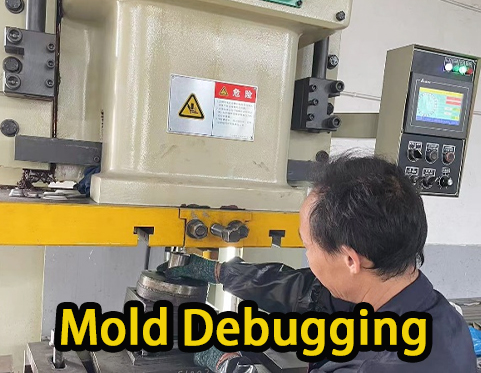
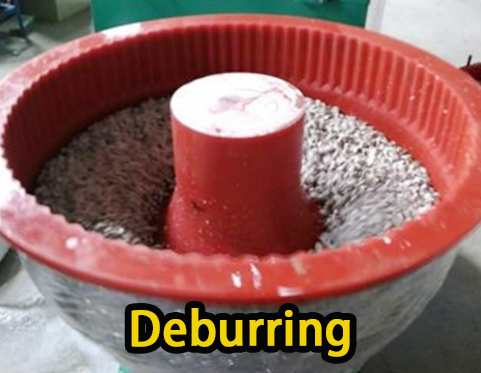

05. Mold assembly
06. Mold debugging
07. Deburring
08. electroplating
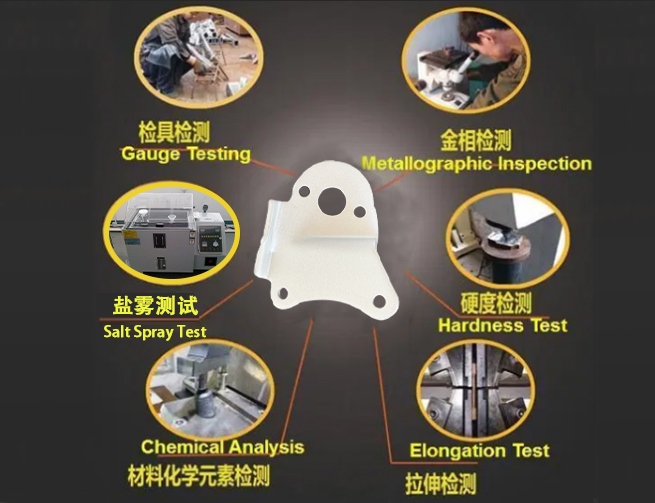
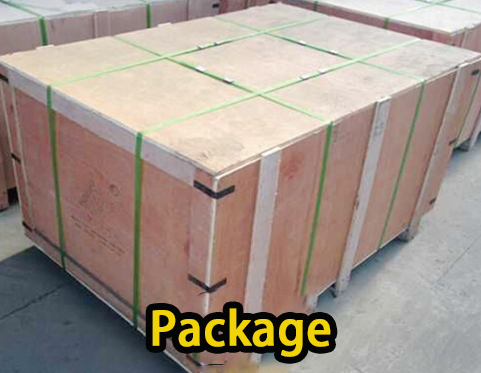
09. Product Testing
10. Package
The Stamping Process
Metal stamping is a manufacturing process in which coils or flat sheets of material are formed into specific shapes. Stamping encompasses multiple forming techniques such as blanking, punching, embossing, and progressive die stamping, to mention just a few. Parts use either a combination of these techniques or independently, depending on the piece’s complexity. In the process, blank coils or sheets get fed into a stamping press which uses tools and dies to form features and surfaces in the metal. Metal stamping is an excellent way to mass-produce various complex parts, from car door panels and gears to small electrical components used in phones and computers. Stamping processes are highly-adopted in automotive, industrial, lighting, medical, and other industries.
FAQ
Q: Are you a trading company or manufacturer?
A: We are manufacturer.
Q: How to get the quote?
A: Please send your drawings (PDF, stp, igs, step...) to us by email , and tell us the material, surface treatment and quantities, then we will make a quotation to you.
Q: Can I order just 1 or 2 pcs for testing?
A: Yes, of course.
Q. Can you produce according to the samples?
A: Yes, we can produce by your samples.
Q: How long is your delivery time?
A: 7~ 15 days, depends on the order quantities and product process.
Q. Do you test all your goods before delivery?
A: Yes, we have 100% test before delivery.
Q: How do you make our business long-term and good relationship?
A:1. We keep good quality and competitive price to ensure our customers benefit ;
2. We respect every customer as our friend and we sincerely do business and make friends with them, no matter where they come from.