Custom sheet metal factory oem sheet metal bending stamping products
Description
Product Type | customized product | |||||||||||
One-Stop Service | Mold development and design-submit samples-batch production-inspection-surface treatment-packaging-delivery. | |||||||||||
Process | stamping,bending,deep drawing,sheet metal fabrication,welding,laser cutting etc. | |||||||||||
Materials | carbon steel,stainless steel,aluminum,copper,galvanized steel etc. | |||||||||||
Dimensions | according to customer's drawings or samples. | |||||||||||
Finish | Spray painting, electroplating, hot-dip galvanizing, powder coating, electrophoresis, anodizing, blackening, etc. | |||||||||||
Application Area | Auto parts, agricultural machinery parts, engineering machinery parts, construction engineering parts, garden accessories, environmentally friendly machinery parts, ship parts, aviation parts, pipe fittings, hardware tool parts, toy parts, electronic parts, etc. |
Quality Warranty
1. All product manufacturing and inspection have quality records and inspection data.
2. All prepared parts undergo strict testing before being exported to our customers.
3. If any of these parts are damaged under normal working conditions, we promise to replace them one by one for free.
That's why we're confident any part we offer will do the job and come with a lifetime warranty against defects.
Quality management
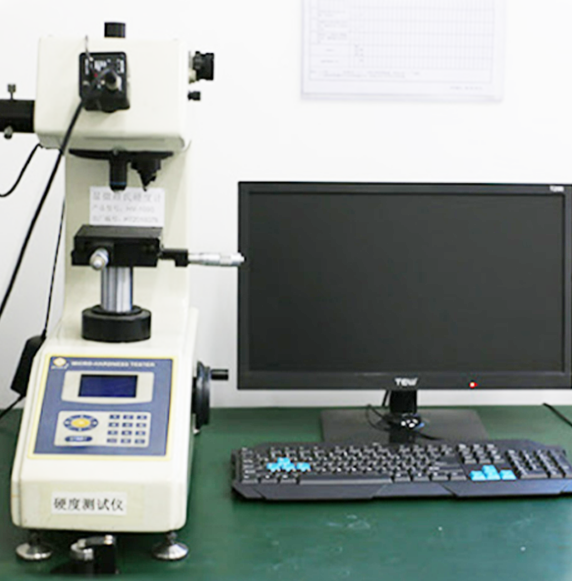
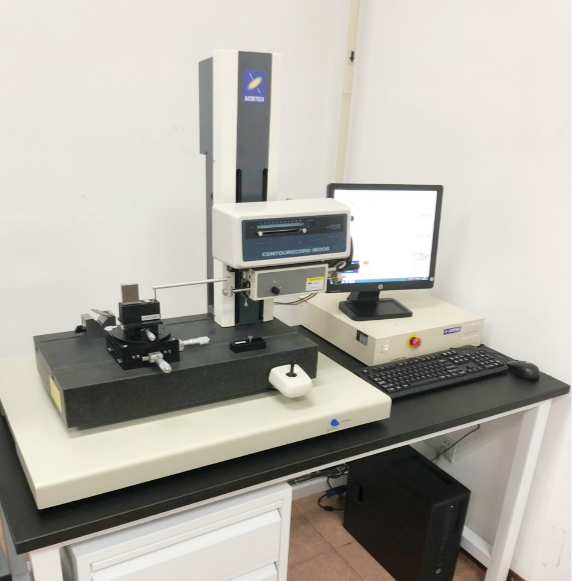
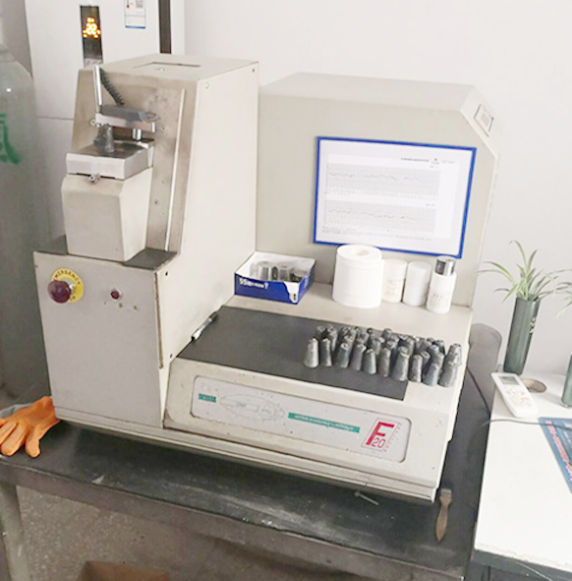
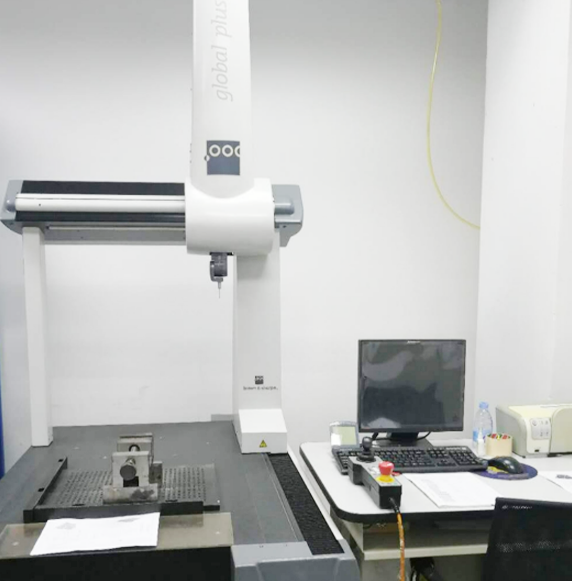
Vickers hardness instrument.
Profile measuring instrument.
Spectrograph instrument.
Three coordinate instrument.
Shipment Picture
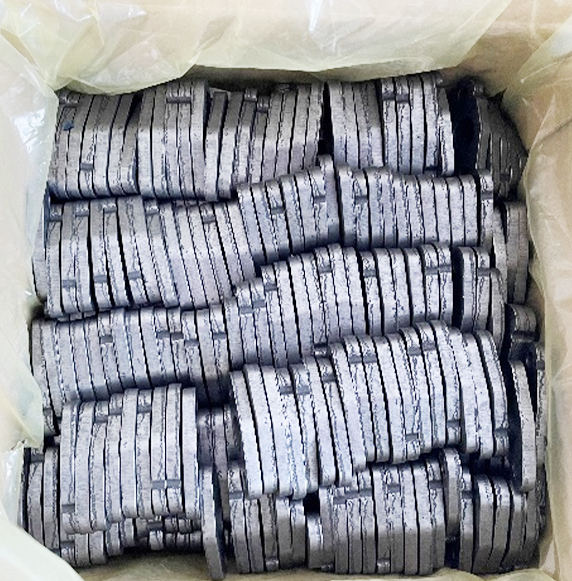
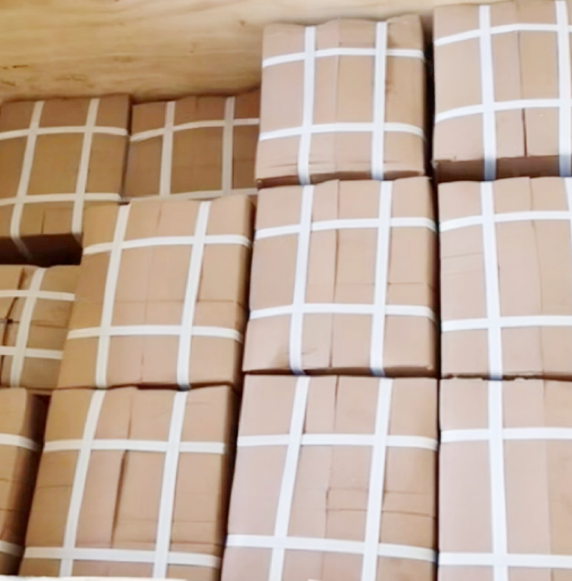
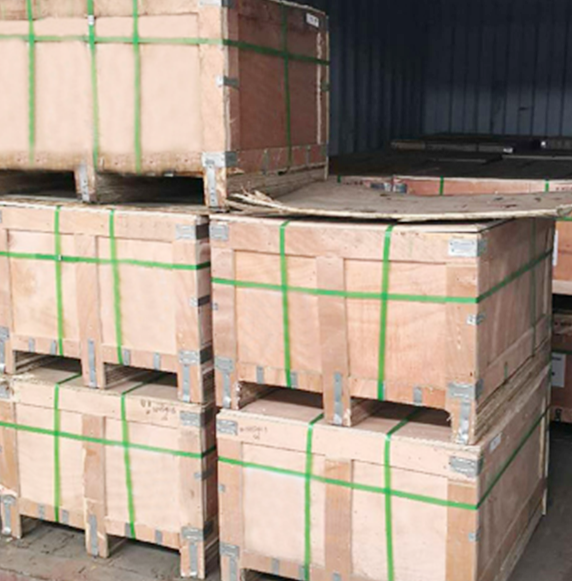
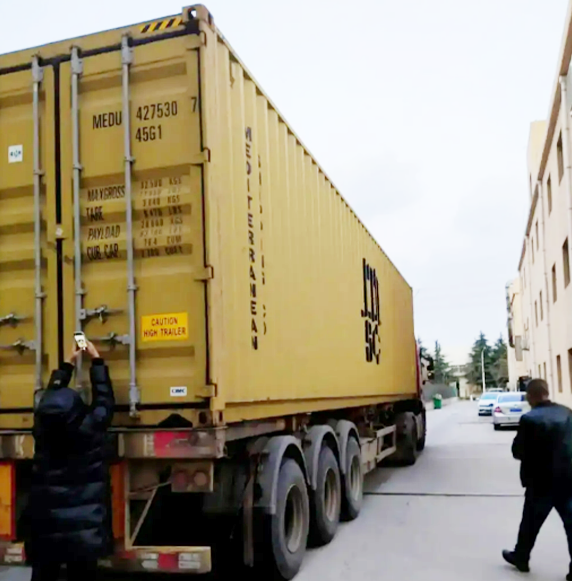
Production Process
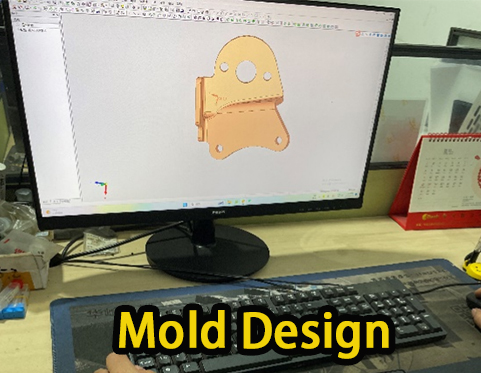
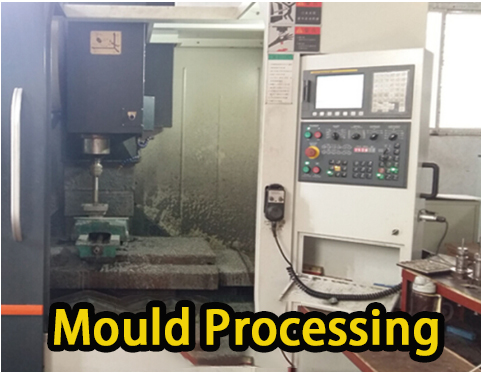
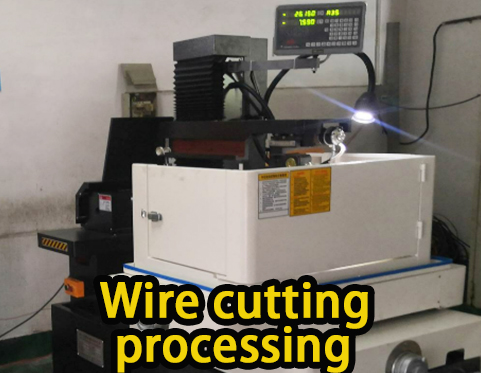
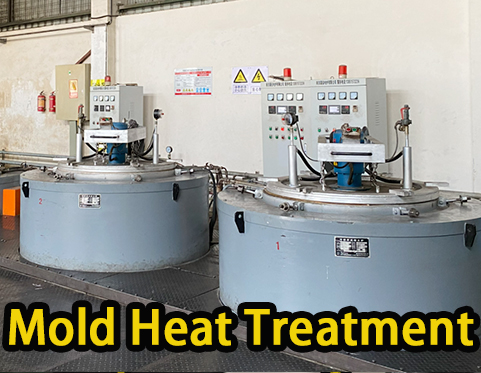
01. Mold design
02. Mould Processing
03. Wire cutting processing
04. Mold heat treatment
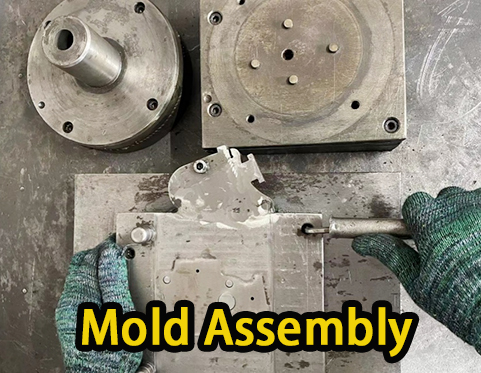
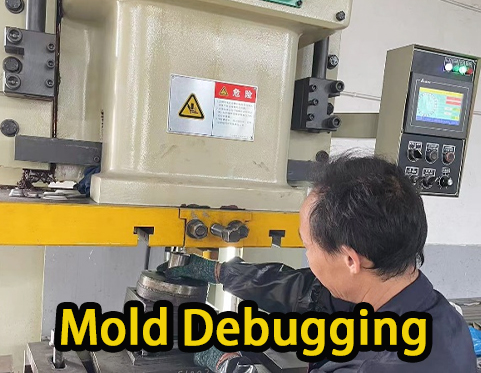
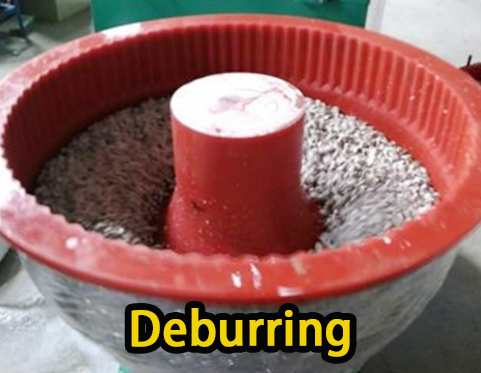

05. Mold assembly
06. Mold debugging
07. Deburring
08. electroplating
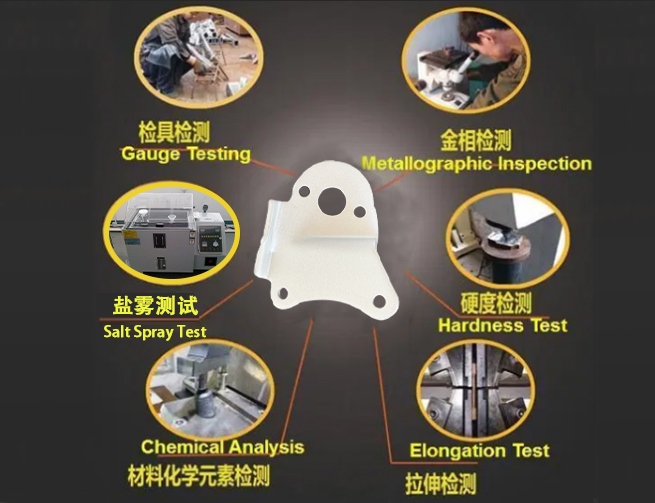
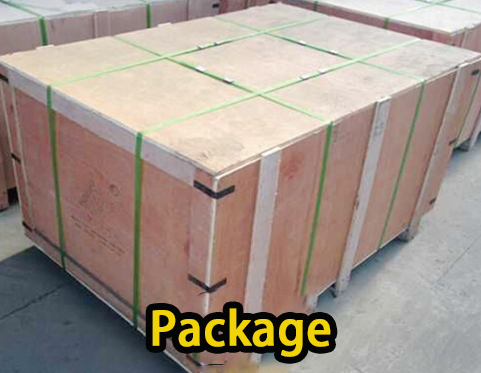
09. Product Testing
10. Package
Advantages of metal stamping
Stamping is suitable for mass, complex part production. More specifically, it offers:
- Complex forms, such as contours
- High volumes (from thousands to millions of parts per year)
- Processes such as fineblanking allow for forming of thick metal sheets.
- Low cost-per-piece prices
Metal stamping design process
One of the more complicated processes in metal stamping is punching, which might involve bending, punching, blanking, and other metal forming techniques.
Blanking is the process of cutting a product's general shape or outline. This step's goal is to reduce and eliminate burrs, which can raise the part's price and cause a delay in delivery. The hole diameter, geometry/taper, edge to hole spacing, and first punch insertion location are all determined in this stage.
Bending: When you design bends in stamped metal components, it is crucial to set enough material aside - make sure you design the part and its blank so that there is enough material to complete the bend.
Punching is the process of tapping a stamped metal part's edges to remove burrs or flatten them. This produces smoother edges in the part's cast areas, increases the strength of the part's localized areas, and can be used to forego secondary processing like deburring and grinding.