Custom Perforating Bend Stamping Component Part Galvanized Sheet Metal
Description
Product Type | customized product | |||||||||||
One-Stop Service | Mold development and design-submit samples-batch production-inspection-surface treatment-packaging-delivery. | |||||||||||
Process | stamping,bending,deep drawing,sheet metal fabrication,welding,laser cutting etc. | |||||||||||
Materials | carbon steel,stainless steel,aluminum,copper,galvanized steel etc. | |||||||||||
Dimensions | according to customer's drawings or samples. | |||||||||||
Finish | Spray painting, electroplating, hot-dip galvanizing, powder coating, electrophoresis, anodizing, blackening, etc. | |||||||||||
Application Area | Auto parts, agricultural machinery parts, engineering machinery parts, construction engineering parts, garden accessories, environmentally friendly machinery parts, ship parts, aviation parts, pipe fittings, hardware tool parts, toy parts, electronic parts, etc. |
Galvanizing process types
1. Cyanide galvanizing: Despite being prohibited owing to environmental concerns, cyanide galvanizing has several uses. The product quality is good when using low cyanide (micro cyanide) plating solution, and it is particularly appropriate for color galvanizing.
2. Zincate galvanizing: This technique developed from cyanide galvanizing and is categorized into two main groups: the Radio and Television Institute's "DE" series and Wuhan Material Protection Institute's "DPE" series. The coating lattice structure is suited for color galvanizing, has good corrosion resistance, and is columnar.
3. Chloride galvanizing: up to 40% of the electroplating sector uses this widely. Ideal for silver or blue white passivation, and particularly well suited for surface treatment subsequent to the application of water-soluble varnish.
4. Sulfate galvanizing is inexpensive and appropriate for continuous plating of wires, strips, and other simple, thick, and large items.
5. Hot-dip galvanizing: To ensure that the zinc liquid adheres to the plated parts uniformly and densely, pickle the parts first to remove the oxide layer. Then, submerge them in the zinc liquid in the hot-dip plating tank.
6. Electro-galvanizing: The plated components' surface is cleaned to eliminate impurities, pickled, and oil and dust removed before being submerged in a zinc salt solution. The plated portions are covered in a zinc layer thanks to an electrolytic reaction.
7. Mechanical galvanizing: A coating is created by mechanically colliding and chemically adsorbing zinc powder to the plated components.
8. Molten galvanizing: The steel is coated with a layer of molten zinc by dipping it in the melt of aluminum alloy, which increases wear and corrosion resistance.
All of the aforementioned procedures have benefits and drawbacks of their own, and they are appropriate for certain application scenarios and requirements.
Quality management
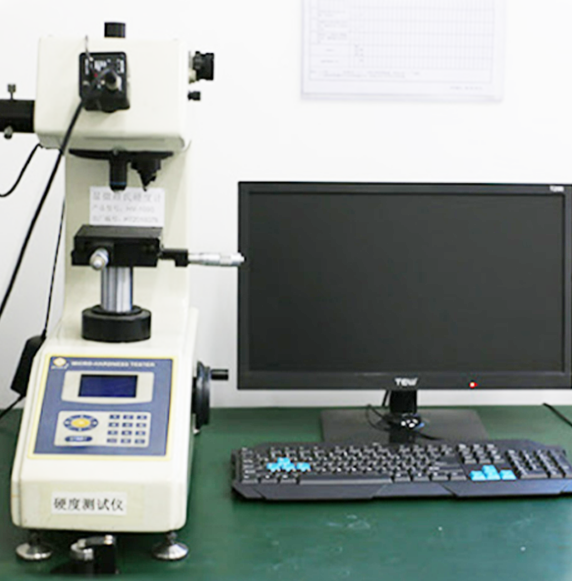
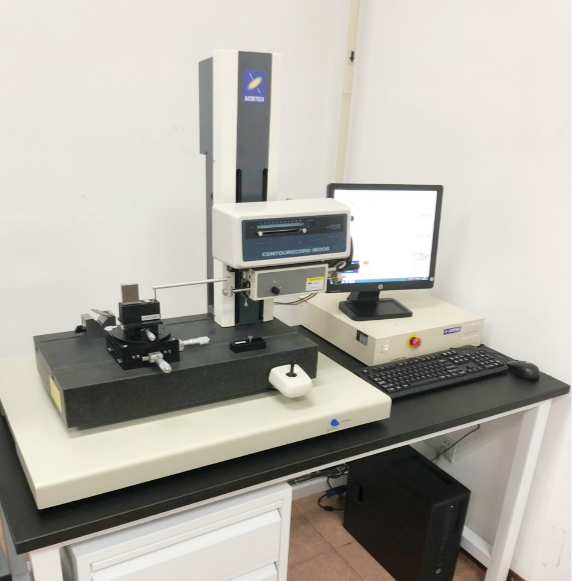
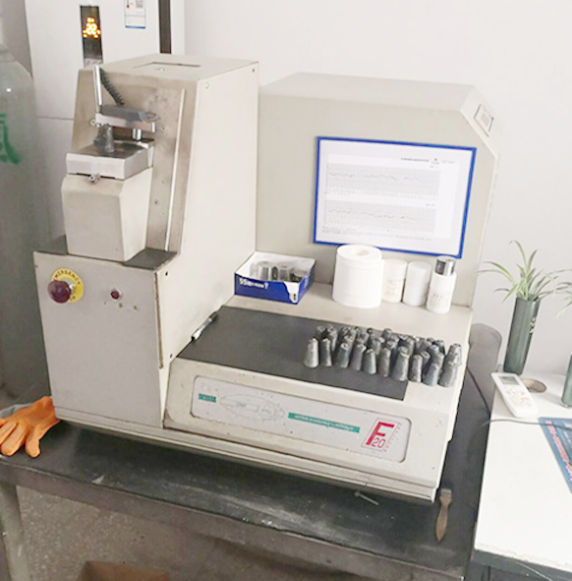
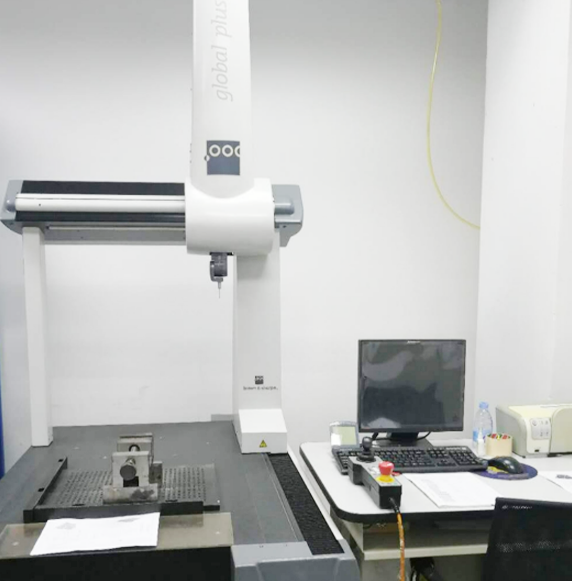
Vickers hardness instrument.
Profile measuring instrument.
Spectrograph instrument.
Three coordinate instrument.
Shipment Picture
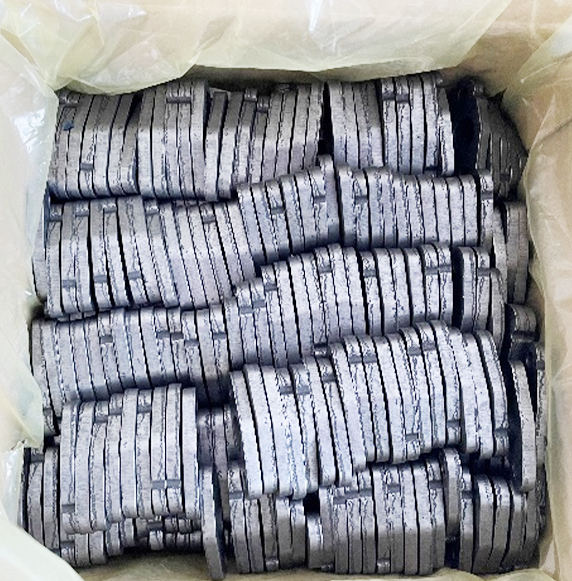
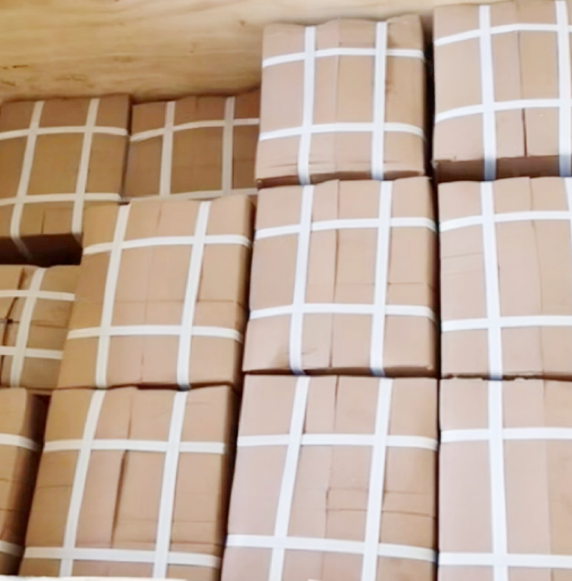
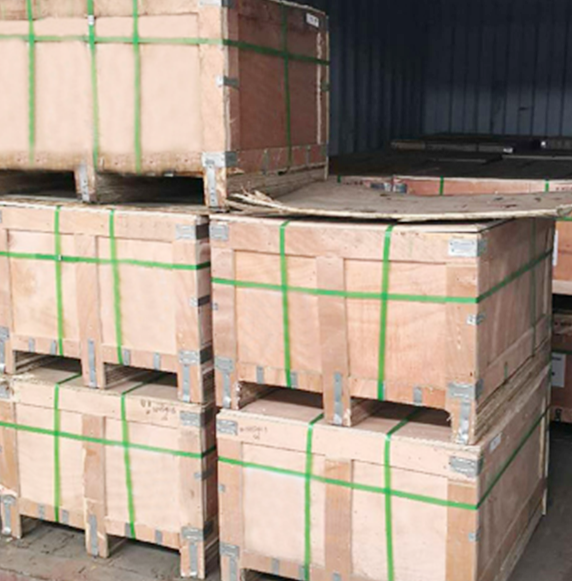
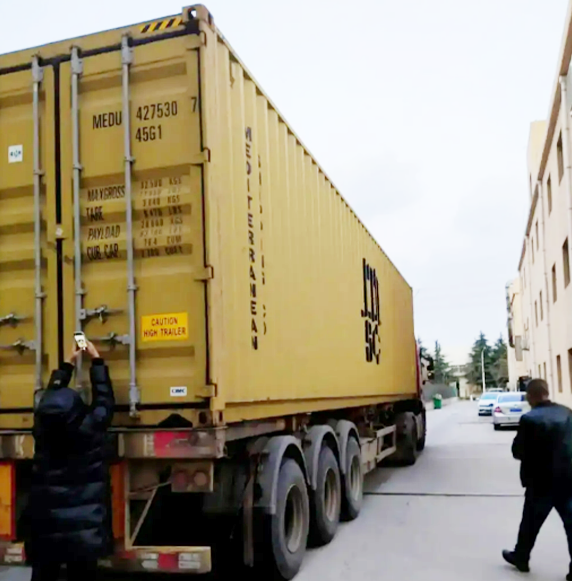
Production Process
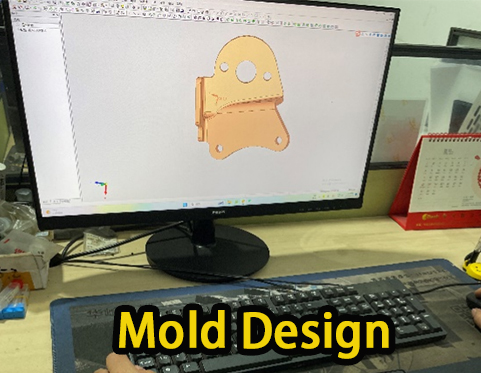
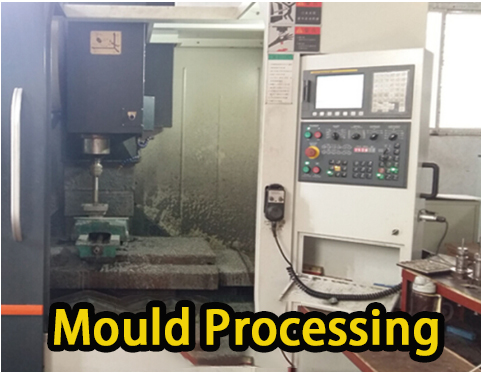
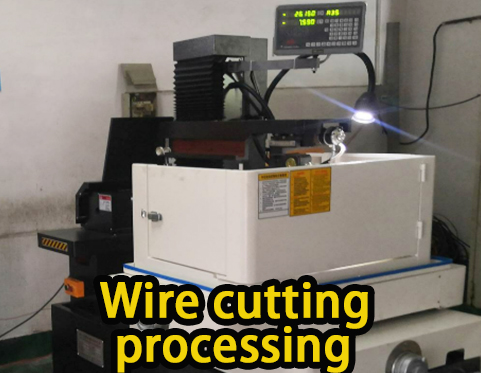
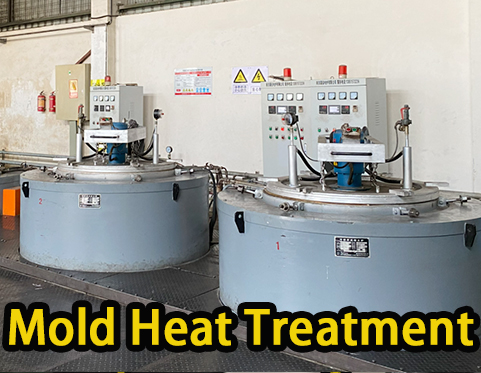
01. Mold design
02. Mould Processing
03. Wire cutting processing
04. Mold heat treatment
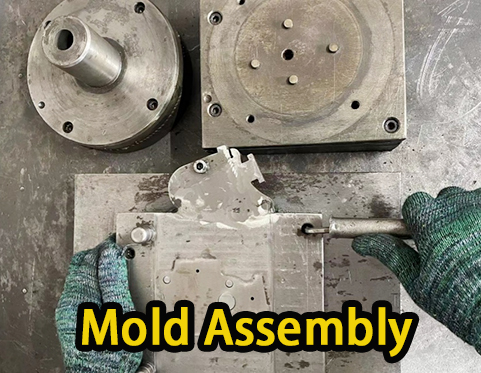
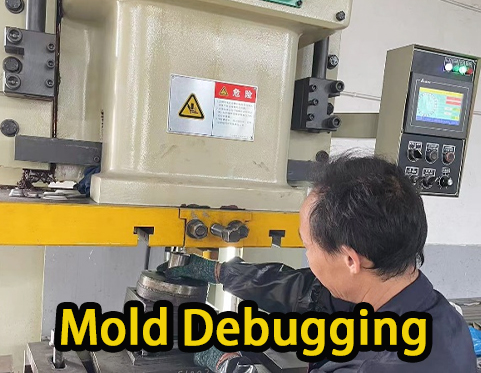
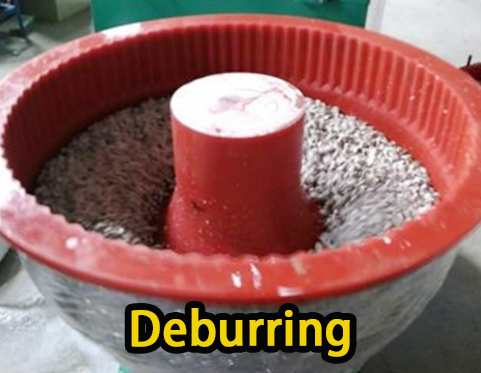

05. Mold assembly
06. Mold debugging
07. Deburring
08. electroplating
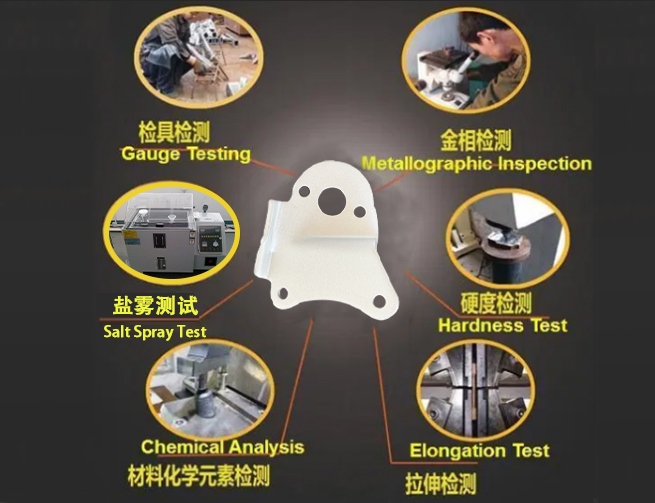
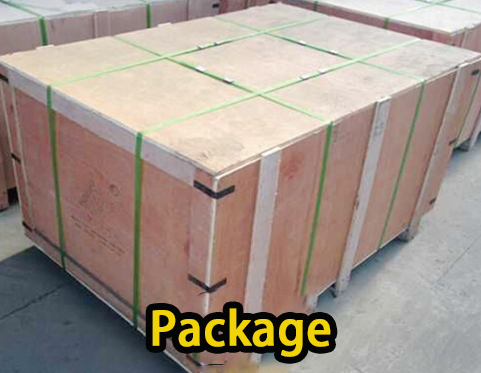
09. Product Testing
10. Package
Hot dip galvanizing process
Galvanizing is a surface treatment technique used to prevent corrosion and add aesthetic appeal by applying a layer of zinc to the surface of metal, alloys, and other materials. Hot dip galvanizing is the principal technique.
Zinc is referred to be an amphoteric metal since it dissolves readily in both acids and alkalis. Dry air causes little change in zinc. On the zinc surface, a thick layer of basic zinc carbonate will develop in humid air. Zinc has a low corrosion resistance in sulfur dioxide, hydrogen sulfide, and marine atmospheres. The zinc coating is easily eroded, especially in environments with high temperatures, high humidity, and organic acids.
Zinc has a typical electrode potential of -0.76 V. Zinc coating is an anodic coating for steel substrates. Its primary purpose is to stop steel from corroding. Its ability to protect is directly correlated with the coating's thickness. The zinc coating's decorative and protective qualities can be greatly enhanced by passivating, dying, or applying a gloss protectant coating.
FAQ
Q: Are you a trading company or manufacturer?
A: We are manufacturer.
Q: How to get the quote?
A: Please send your drawings (PDF, stp, igs, step...) to us by email , and tell us the material, surface treatment and quantities, then we will make a quotation to you.
Q: Can I order just 1 or 2 pcs for testing?
A: Yes, of course.
Q. Can you produce according to the samples?
A: Yes, we can produce by your samples.
Q: How long is your delivery time?
A: 7~ 15 days, depends on the order quantities and product process.
Q. Do you test all your goods before delivery?
A: Yes, we have 100% test before delivery.
Q: How do you make our business long-term and good relationship?
A:1. We keep good quality and competitive price to ensure our customers benefit ;
2. We respect every customer as our friend and we sincerely do business and make friends with them, no matter where they come from.