precision cold stamping process supplier
Description
Product Type | customized product | |||||||||||
One-Stop Service | Mold development and design-submit samples-batch production-inspection-surface treatment-packaging-delivery. | |||||||||||
Process | stamping,bending,deep drawing,sheet metal fabrication,welding,laser cutting etc. | |||||||||||
Materials | carbon steel,stainless steel,aluminum,copper,galvanized steel etc. | |||||||||||
Dimensions | according to customer's drawings or samples. | |||||||||||
Finish | Spray painting, electroplating, hot-dip galvanizing, powder coating, electrophoresis, anodizing, blackening, etc. | |||||||||||
Application Area | Auto parts, agricultural machinery parts, engineering machinery parts, construction engineering parts, garden accessories, environmentally friendly machinery parts, ship parts, aviation parts, pipe fittings, hardware tool parts, toy parts, electronic parts, etc. |
Advantags
1. More than 10 years of overseas trade expertise.
2. Provide one-stop service from mold design to product delivery.
3. Fast delivery time, about 30-40 days. In stock within one week.
4. Strict quality management and process control (ISO certified manufacturer and factory).
5. More reasonable prices.
6. Professional, our factory has more than 10 years of history in the field of metal stamping sheet metal.
Quality management
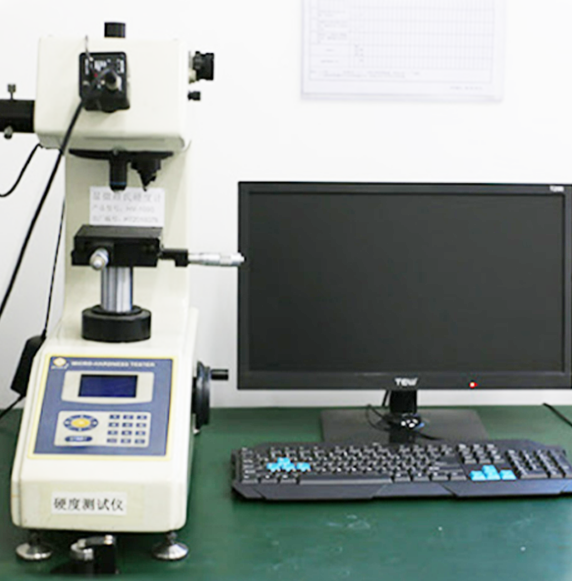
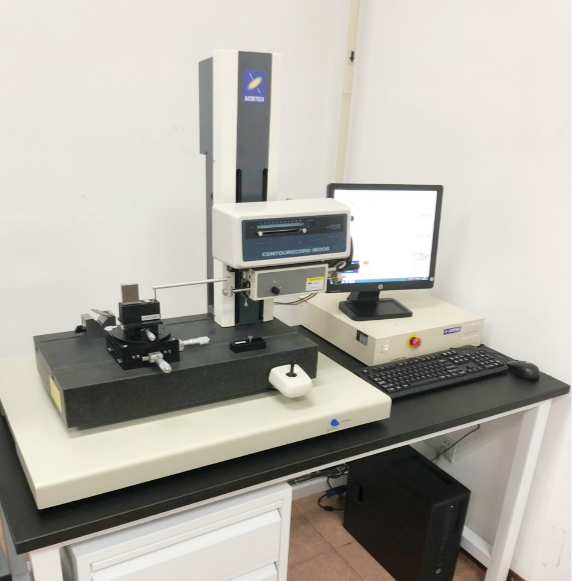
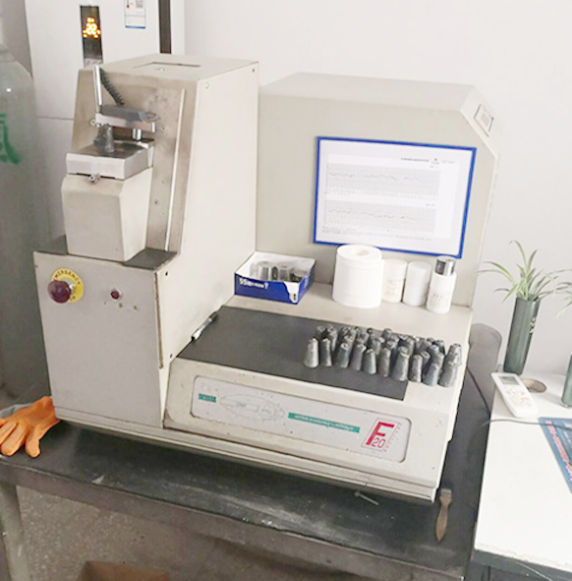
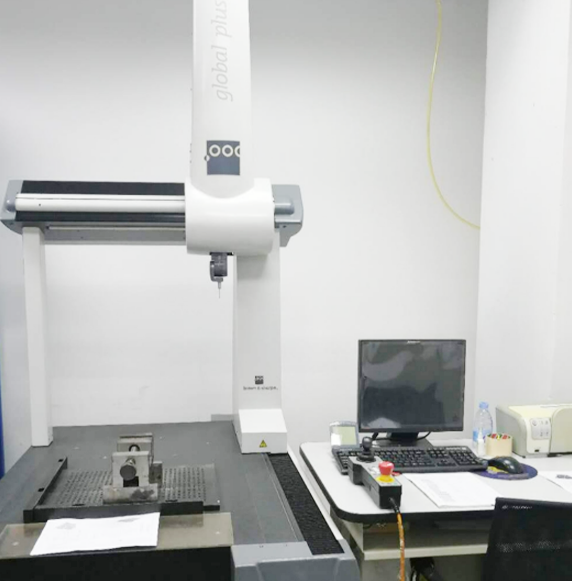
Vickers hardness instrument.
Profile measuring instrument.
Spectrograph instrument.
Three coordinate instrument.
Shipment Picture
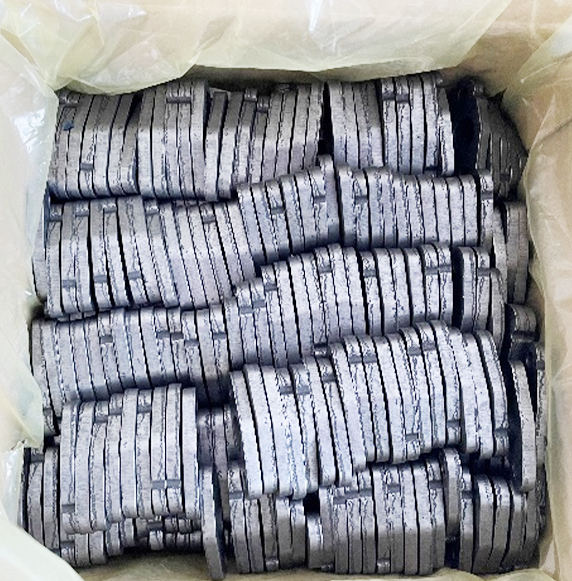
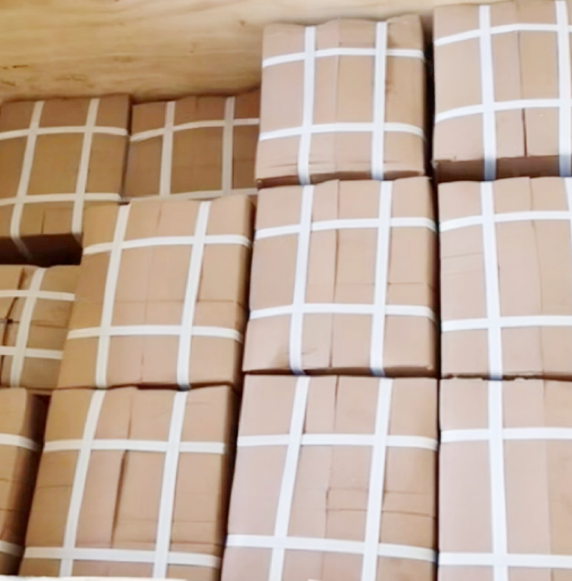
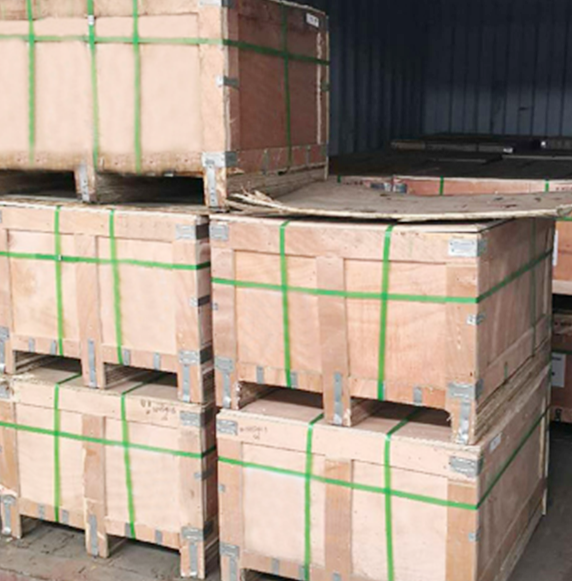
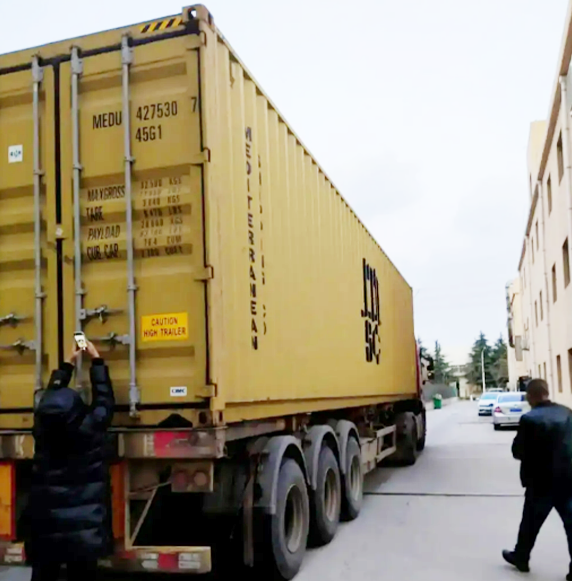
Production Process
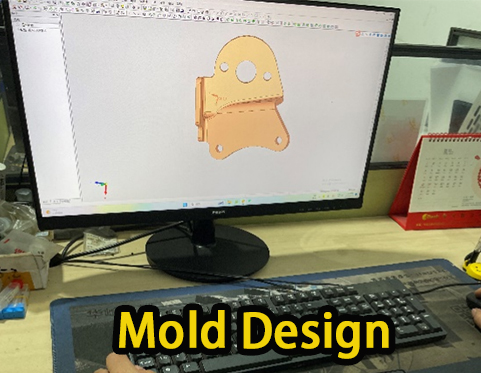
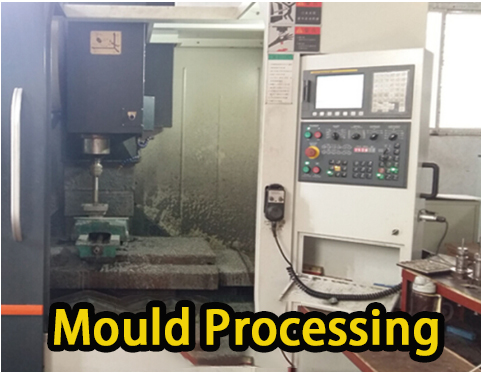
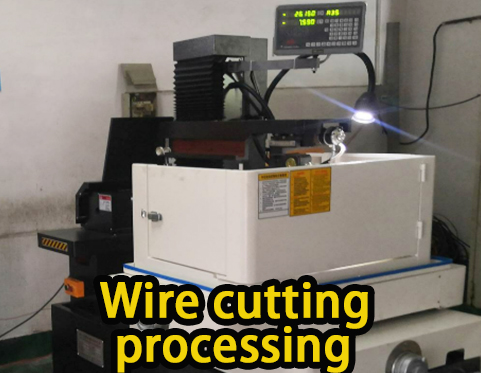
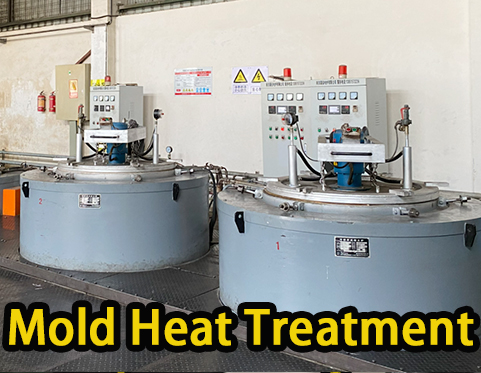
01. Mold design
02. Mould Processing
03. Wire cutting processing
04. Mold heat treatment
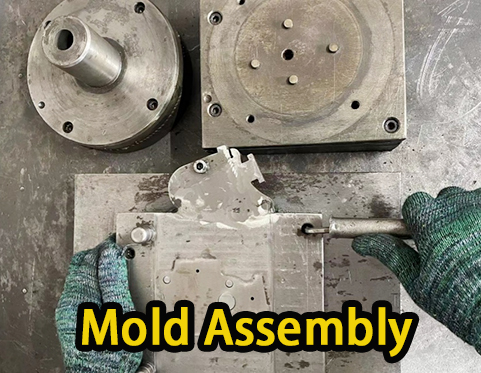
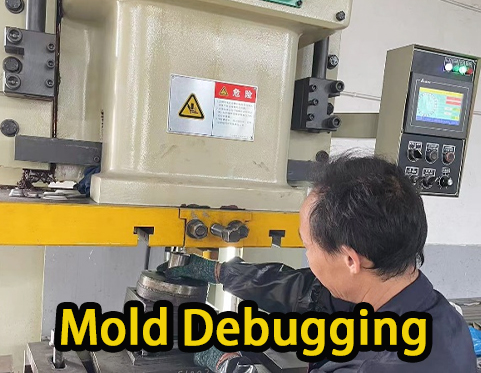
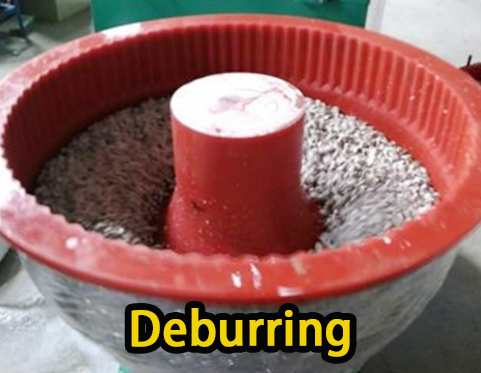

05. Mold assembly
06. Mold debugging
07. Deburring
08. electroplating
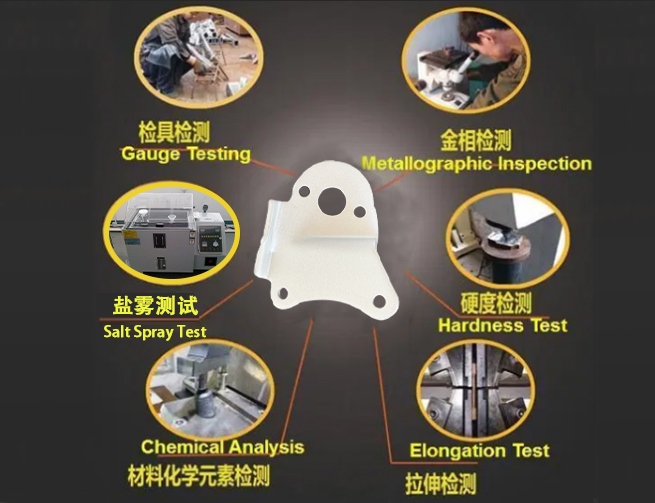
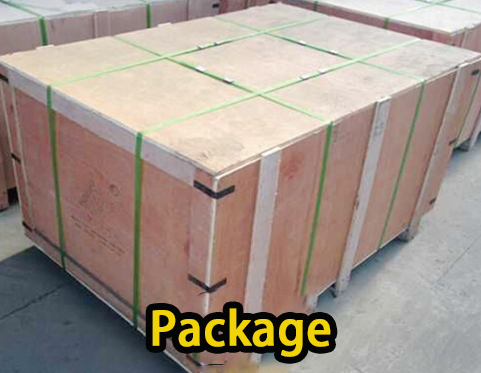
09. Product Testing
10. Package
Stamping basics
Stamping (also called pressing) involves placing flat metal in coil or blank form into a stamping machine. In a press, tool and die surfaces shape metal into the desired shape. Punching, blanking, bending, stamping, embossing and flanging are all stamping techniques used to shape metal.
Before the material can be formed, stamping professionals must design the mold through CAD/CAM engineering. These designs must be as precise as possible to ensure proper clearance for each punch and bend for optimal part quality. A single tool 3D model can contain hundreds of parts, so the design process is often quite complex and time-consuming.
Once a tool's design is determined, manufacturers can use a variety of machining, grinding, wire-cutting, and other manufacturing services to complete its production.
Metal stamping design process
Metal stamping is a complex process that may include a variety of metal forming processes - blanking, punching, bending and punching, among others.
Blanking: This process involves cutting the rough outline or shape of a product. The purpose of this stage is to minimize and avoid burrs, which can increase the cost of the part and extend delivery time. This step is to determine the hole diameter, geometry/taper, edge to hole spacing and where to insert the first punch.
Bending: When you design bends in stamped metal parts, it is important to leave enough material aside - make sure you design the part and its blank so that there is enough material to perform the bend.
Punching: This operation is when the edges of a stamped metal part are tapped to flatten or break off burrs; this creates smoother edges in the cast areas of the part geometry; this also adds extra strength to localized areas of the part, and Can be used to avoid secondary processing such as deburring and grinding.