Custom Carbon steel sheet metal stamping products factory
Description
Product Type | customized product | |||||||||||
One-Stop Service | Mold development and design-submit samples-batch production-inspection-surface treatment-packaging-delivery. | |||||||||||
Process | stamping,bending,deep drawing,sheet metal fabrication,welding,laser cutting etc. | |||||||||||
Materials | carbon steel,stainless steel,aluminum,copper,galvanized steel etc. | |||||||||||
Dimensions | according to customer's drawings or samples. | |||||||||||
Finish | Spray painting, electroplating, hot-dip galvanizing, powder coating, electrophoresis, anodizing, blackening, etc. | |||||||||||
Application Area | Auto parts, agricultural machinery parts, engineering machinery parts, construction engineering parts, garden accessories, environmentally friendly machinery parts, ship parts, aviation parts, pipe fittings, hardware tool parts, toy parts, electronic parts, etc. |
Types of stamping
We offer single and multistage, progressive die, deep draw, fourslide, and other stamping methods to ensure the most effective method for manufacturing your products. Xinzhe’s experts can match your project with the appropriate stamping by reviewing your uploaded 3D model and technical drawings.
- Blanking cuts pieces out from the sheet as an initial step before forming. Fineblanking, a variation of blanking, makes precise cuts with smooth edges and a flat surface.
- Coining is another type of blanking that creates small round workpieces. Since it involves significant force to form a small piece, it hardens the metal and removes burrs and rough edges.
- Punching is the opposite of blanking; it involves removing material from the workpiece instead of removing material to create a workpiece.
- Embossing creates a three-dimensional design in the metal, either raised above the surface or through a series of depressions.
- Bending happens on a single axis and is often used to create profiles in U, V, or L shapes. This technique is accomplished by clamping one side and bending the other over a die or pressing the metal into or against a die. Flanging is bending for tabs or parts of a workpiece instead of the whole part.
Quality management
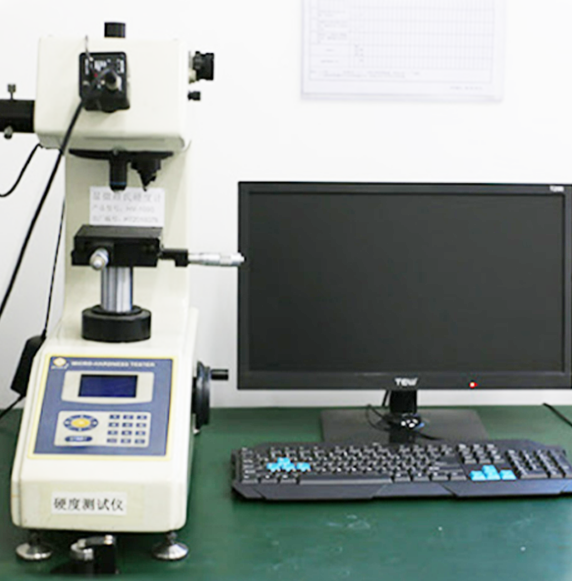
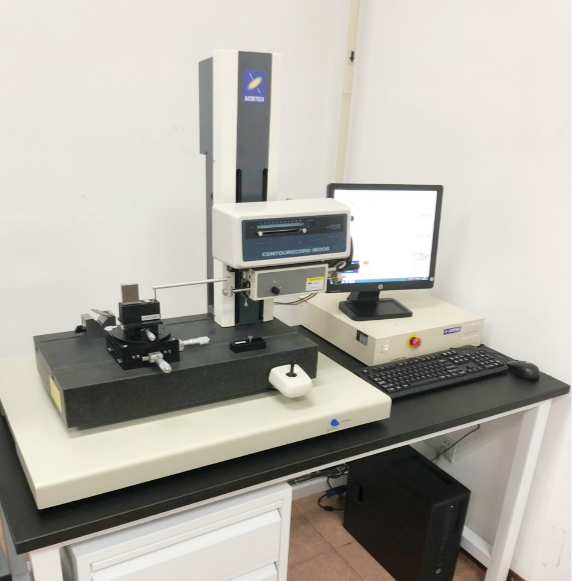
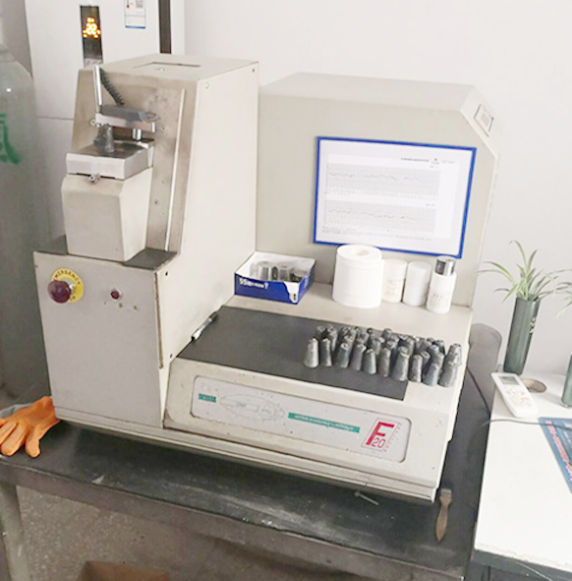
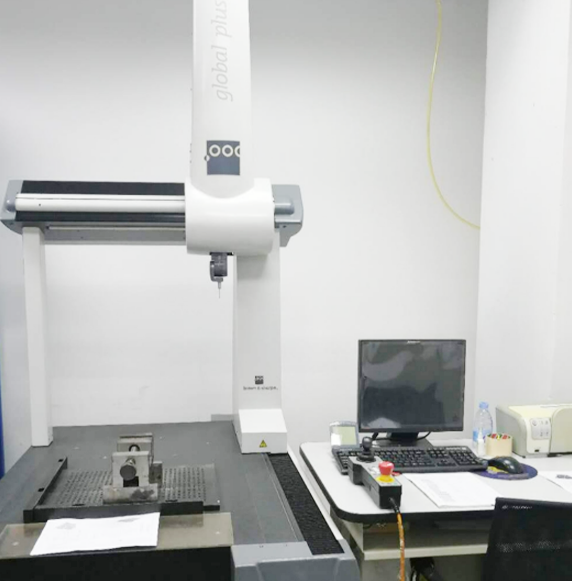
Vickers hardness instrument.
Profile measuring instrument.
Spectrograph instrument.
Three coordinate instrument.
Shipment Picture
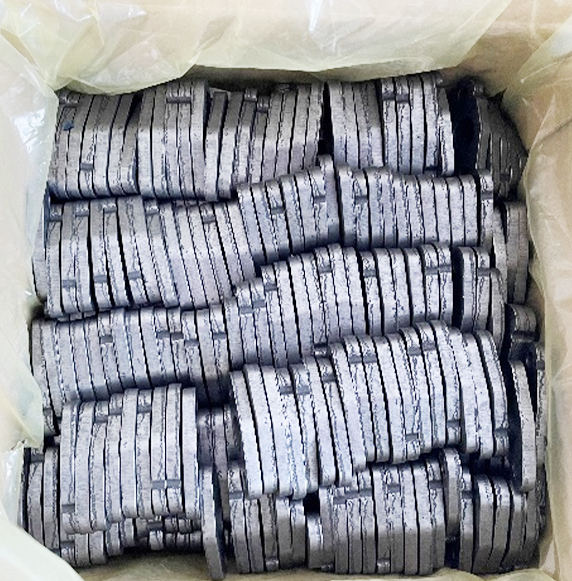
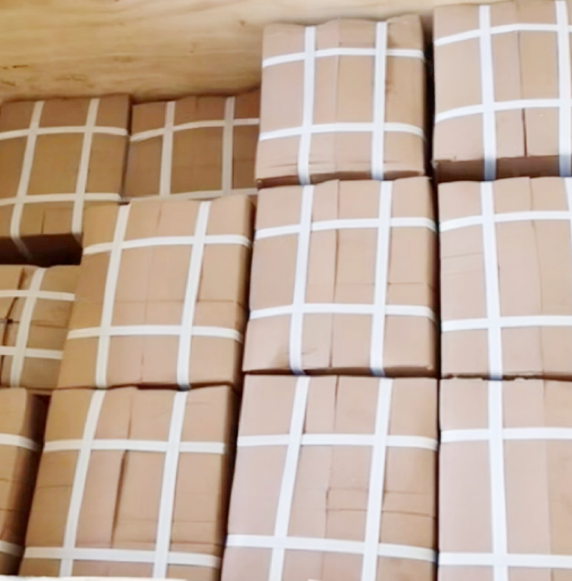
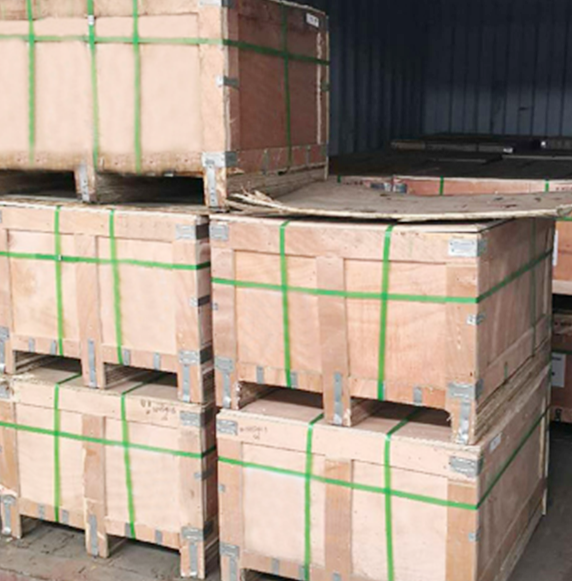
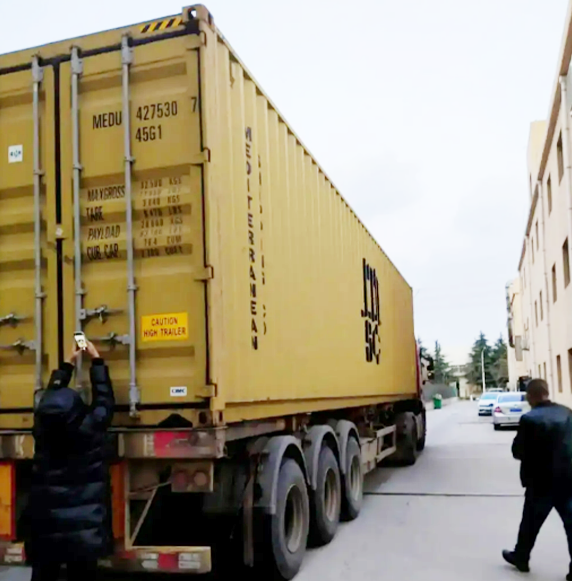
Production Process
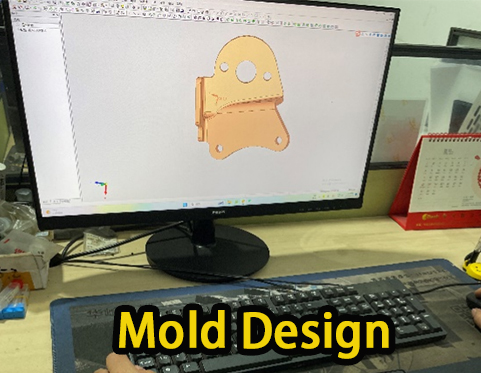
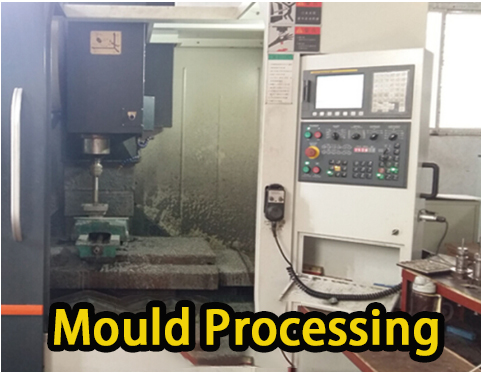
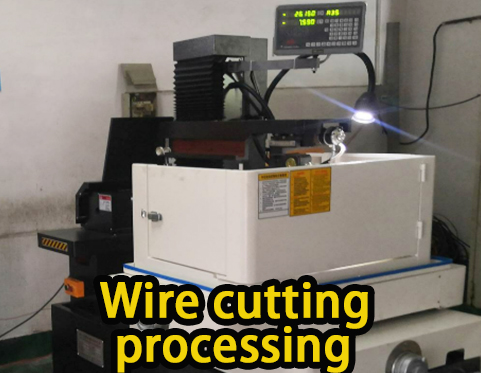
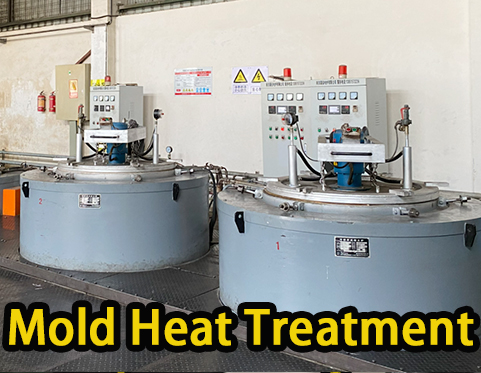
01. Mold design
02. Mould Processing
03. Wire cutting processing
04. Mold heat treatment
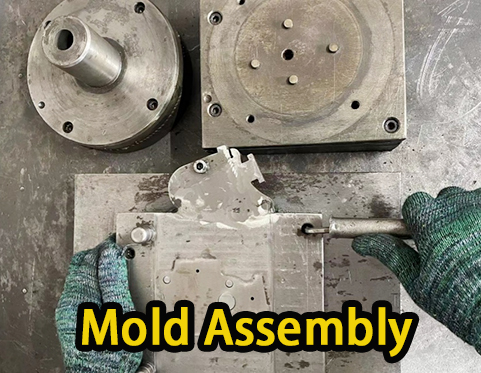
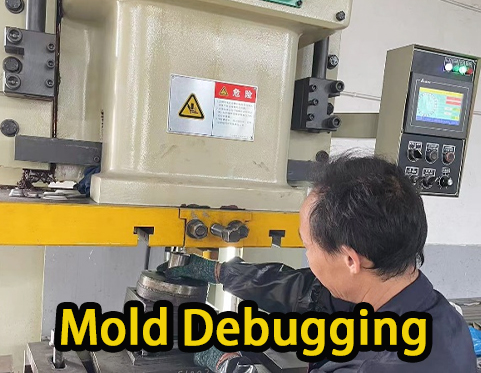
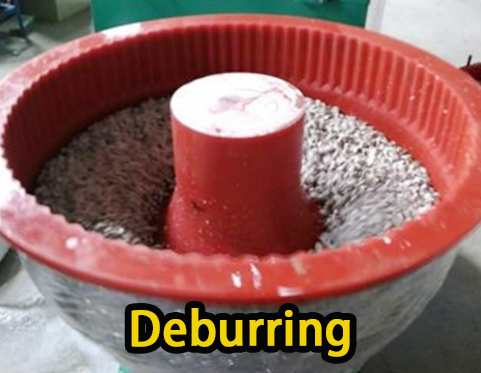

05. Mold assembly
06. Mold debugging
07. Deburring
08. electroplating
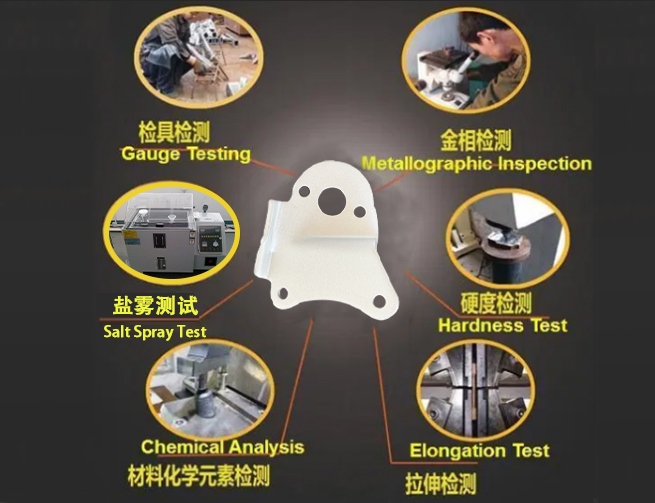
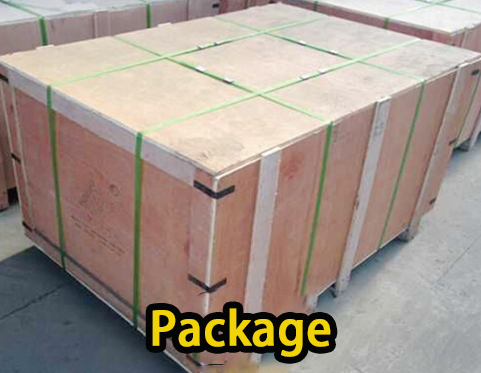
09. Product Testing
10. Package
The Stamping Process
Metal stamping is a manufacturing process in which coils or flat sheets of material are formed into specific shapes. Stamping encompasses multiple forming techniques such as blanking, punching, embossing, and progressive die stamping, to mention just a few. Parts use either a combination of these techniques or independently, depending on the piece’s complexity. In the process, blank coils or sheets get fed into a stamping press which uses tools and dies to form features and surfaces in the metal. Metal stamping is an excellent way to mass-produce various complex parts, from car door panels and gears to small electrical components used in phones and computers. Stamping processes are highly-adopted in automotive, industrial, lighting, medical, and other industries.
Stamping basics
Stamping (also called pressing) involves placing flat metal in coil or blank form into a stamping machine. In a press, tool and die surfaces shape metal into the desired shape. Punching, blanking, bending, stamping, embossing and flanging are all stamping techniques used to shape metal.
Before the material can be formed, stamping professionals must design the mold through CAD/CAM engineering. These designs must be as precise as possible to ensure proper clearance for each punch and bend for optimal part quality. A single tool 3D model can contain hundreds of parts, so the design process is often quite complex and time-consuming.
Once a tool's design is determined, manufacturers can use a variety of machining, grinding, wire-cutting, and other manufacturing services to complete its production.